
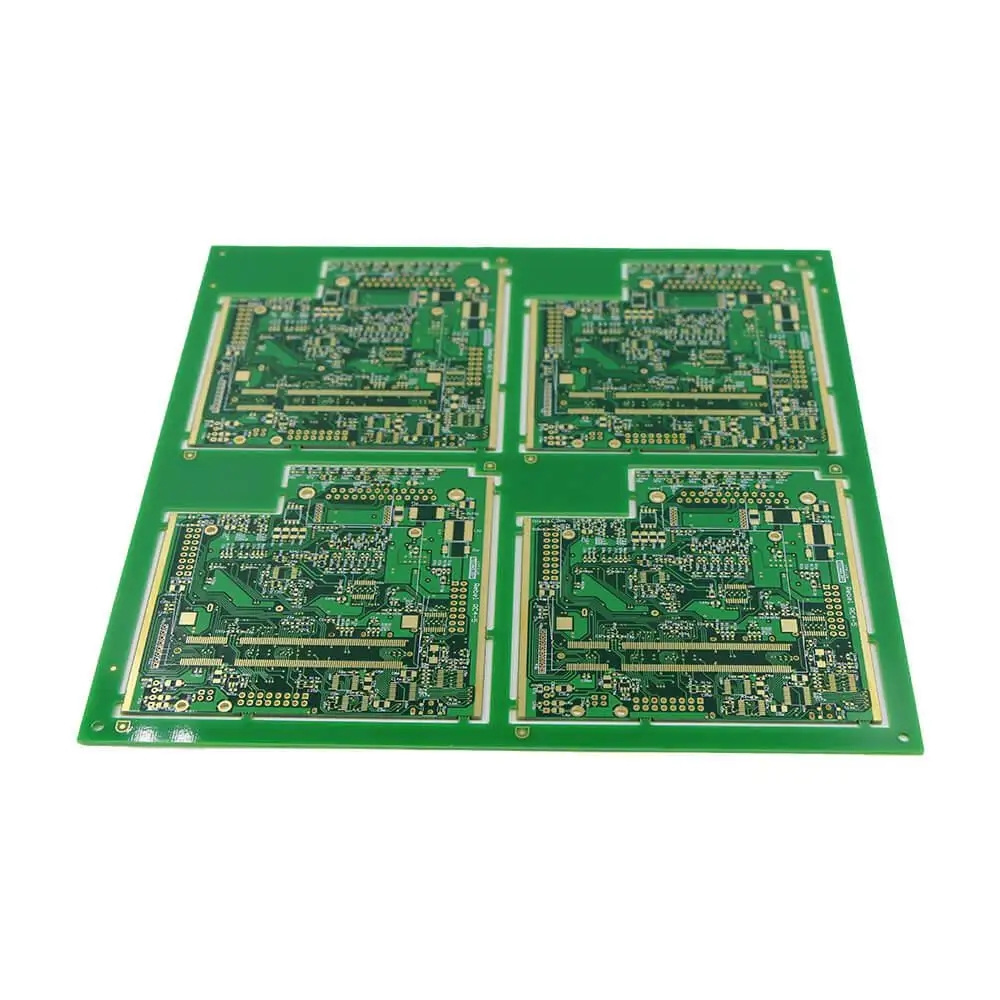
Analysis of the reasons for the viscosity reduction of solder paste for circuit boards
The phenomenon of low viscosity of solder paste refers to the phenomenon that parts cannot be stuck by solder paste during or after the process of printing. Possible reasons for low viscosity include: insuffICient solder paste coating, insufficient flux viscosity, improper metal content, too rough particle size, rapid movement of the circuit board during printing, poor support of the circuit board during printing, humidity influence, etc.
If the printing amount of the solder paste circuit board is insufficient, it is understandable that the solder paste cannot hold the parts printed on the circuit board. Flux is the decisive factor for the adhesion of solder paste. Low viscosity solder paste will naturally be produced by low viscosity solder flux. Because tin powder itself cannot provide viscosity, excessive powder particles are detrimental to the maintenance of viscosity. However, the relationship between metal content and viscosity is quite complex. With the increase of metal content, the viscosity gradually decreases. At the beginning, the viscosity drops rapidly, and then the speed of reduction gradually slows down. The decreasing trend is probably related to the thickness of the test sample.
Generally speaking, the SMAller the powder content is, the more solder paste will be squeezed during the viscosity test period, and the smaller the gap between the test probe and the substrate, which is conducive to maintaining the integrity of the printing and preventing leakage. When the metal content exceeds about 40%, according to the test experience value of a solder paste, the viscosity will increase slightly and then decrease with the increase of the metal content.
The increase of viscosity should be due to the increase of cohesion generated by the reinforcement effect of filler. When the metal content exceeds a certain critical value, the viscosity will continue to decline, which is due to the insufficient coating and adhesion of solder flux to tin powder, and the insufficient adhesion will gradually increase. The viscosity is proportional to the adhesive force and cohesion of the solder paste, and the adhesive force is dominated by a single element of the flux. Cohesion will increase with the decrease of powder size, which is due to the increase of solder paste viscosity, thus leading to the increase of viscosity.
The firmness of the stamping parts is determined not only by the viscosity of the solder paste, but also by the complex problems involved in the stamping equipment. For a piece printing device, a certain solder paste is in good condition, but unfortunately, a problem occurs when the device is replaced. One of the important factors affecting the maintenance capability of parts is the movement of circuit boards. If the circuit board moves fast during the printing phase, the inertia of the part may exceed the adhesive force of the solder paste, which will cause the part to slide.
Another influencing factor is the stability of the circuit board itself when printing. If the circuit board is not well supported and fixed, when it is impacted by the placement arm, the circuit board will shake greatly, so there will be the problem of dropping and throwing parts. Proper process design should include a reasonable supporting mechanism and a solid fixture for clamping the circuit board.
Viscosity is an important characteristic function of flux. Some fluxes will quickly absorb moisture, and humidity will inevitably affect the viscosity of solder paste. High humidity may cause surface crusting, solder paste thinning and viscosity reduction, which should be avoided.
When the solder paste is just exposed to the air, there will be an appropriate or high viscosity. However, the viscosity of printed circuit boards decreases rapidly with time, which will narrow the scope of PCB processing operations.
The possible reasons for the short viscosity time include: high metal content, high solvent volatility, coarse powder particle size, hard skin on the printed solder paste surface, large air flow in the operating environment, improper humidity, high ambient temperature, and too thin steel plate.
The problem of metal content has been discussed again and again. The time to maintain the viscosity will shorten with the increase of metal content. It is obvious that if the flux content is increased, the time for the solder paste to maintain its viscosity will inevitably increase, which can also be explained as the effect of the increase of solvent content. In this way, it can be understood that many circuit board manufacturers or literature statements have reasons to keep the solder paste metal content below the recommended 90%.
The increase of the surface area of the powder particles will help the solvent to remain for a long time, which is due to the enhanced surface adsorption between the powder particles and the solvent. However, if the powder particles are small, the chEMIcal reaction between the flux and the powder particles will increase and speed up, which may also result in surface scaling and reduce the viscosity time.
PCB manufacturers, PCB designers, and PCBA processors will explain the reasons for the viscosity reduction of PCB solder paste.
然后
聯(lián)系
電話熱線
13410863085Q Q
微信
- 郵箱