
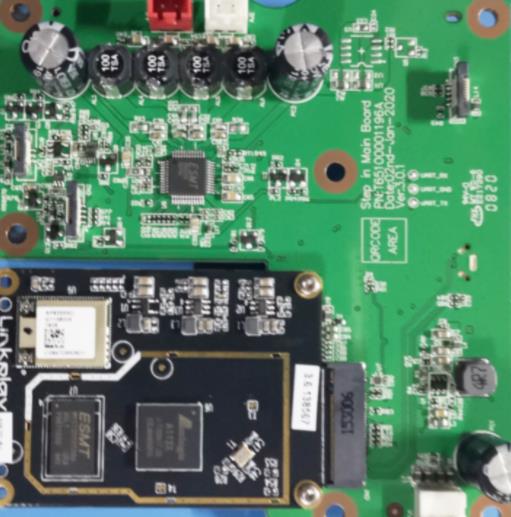
Surface Mount Technology is a complex and common processing problem
SMT patch processing is very complICated, and many people have seen this opportunity After learning the SMT chip processing process, they opened a factory, especially a very mature enterprise in the electronics industry SMT patch processing has been caused In an industry that is taking shape, many organizations that need fine technology will choose SMT chip processing plants What are the precautions for SMT chip processing?
Pay attention to electrostatic discharge measures during chip processing. It mainly includes the design of SMT patch and the re established standard. In order to be sensitive to the electrostatic discharge during the processing of SMT patch, the corresponding treatment and protection are carried out. Measures are critical. If these standards are not clear, you can refer to the relevant documents for learning.
Circuit board
SMT wafer processing must fully comply with the above welding procedure qualification standards. During welding, common welding and manual welding are usually used. For the welding technology and standards required for processing SMT chips, refer to the Welding Technology Evaluation Manual. Of course, some high-tech chip processing plants also carry out 3D construction for the products to be processed, so that the effect after processing will reach the standard and the appearance will be more perfect.
After that, SMT wafer processing and welding technology is a cleaning measure. Cleaning must be carried out in strict accordance with the standards, otherwise the safety of SMT wafer processing will not be guaranteed Therefore, the type and nature of detergent are required during cleaning, and the integrity and safety of equipment and process need to be considered during cleaning
Common problems in SMT patch processing?
Common problems of tin bead in SMT wafer processing and welding technology: insufficient preheating of PCB during reflow soldering; The setting of reflow welding temperature curve is unreasonable, and there is a large gap between the plate surface temperature and the welding area temperature before entering the welding area; Solder paste cannot be completely recovered to room temperature when it is taken out of the cold storage; Solder paste is exposed to air for a long time after opening; Tin powder splashes on PCB surface when mounting; During printing or transfer, oil or water sticks to PCB; The flux itself in the solder paste is unevenly distributed, and there are solvent or liquid additives or activators that are not easy to evaporate.
The first and second reasons above can also clarify why new solder pastes are easy to cause such doubts. The main reason is that the current set temperature curve does not match the solder paste used.
The third, fourth and sixth reasons may be caused by improper operation of the user; The fifth reason may be improper storage of solder paste or the solder paste becomes invalid after expiration. Solder paste is not sticky or too sticky. Low, tin powder splashes during placement; The seventh reason is the solder paste supplier's own production technology.
After that, there are more residues on the board surface SMT welding: after welding, there are more residues on the PCB board surface, which is also a problem frequently reported by customers More residues on the circuit board surface will affect the brightness of the circuit board surface It also has an inevitable impact on the power characteristics of PCB itself; The main reasons for the formation of more residues are as follows: when implementing solder paste, the situation of the customer's board of directors and customer needs are unknown, or other reasons caused by wrong selection; There is too much rosin resin in the solder paste or the quality is poor
然后
聯(lián)系
電話熱線
13410863085Q Q
微信
- 郵箱