
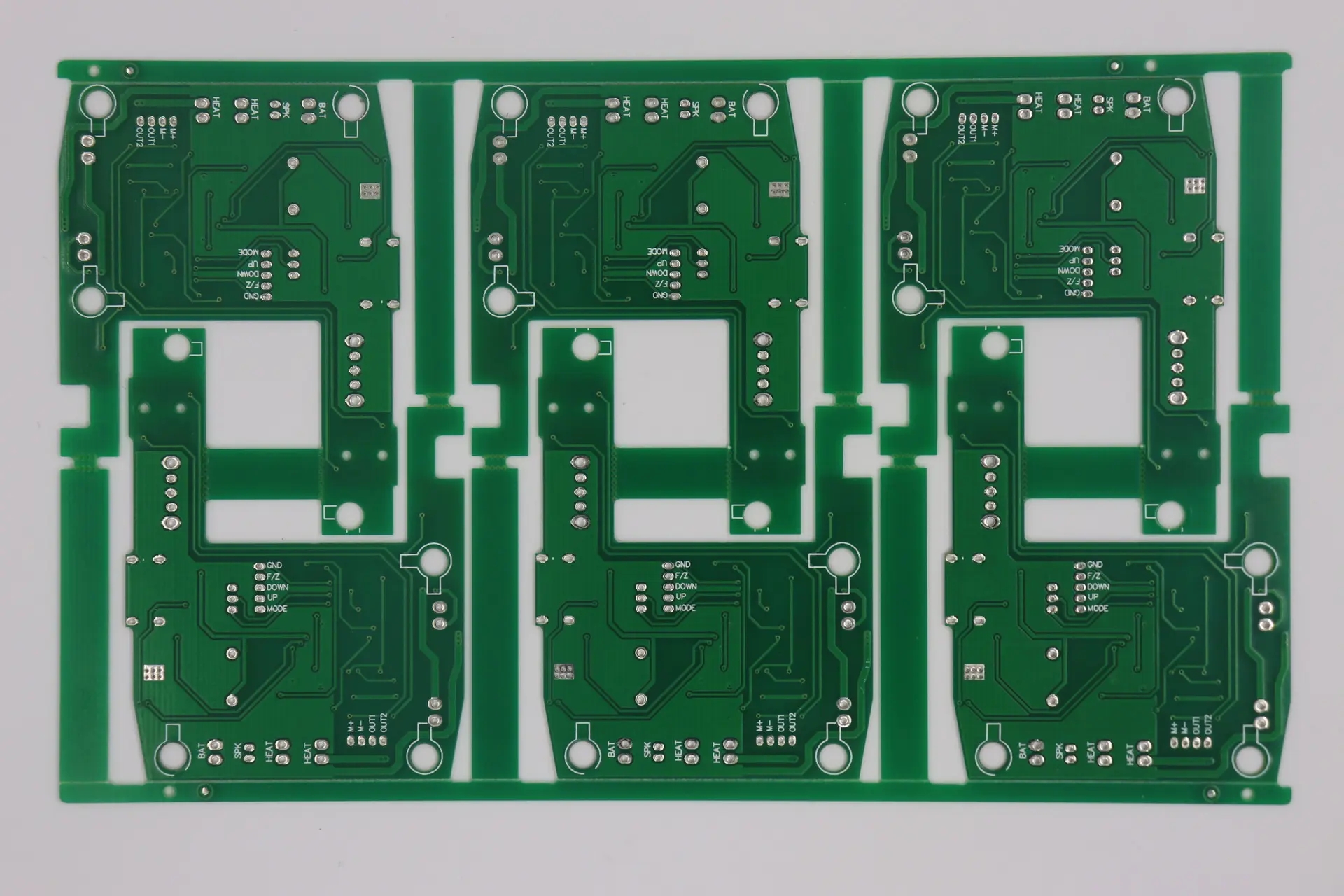
Six Skills for Selecting components in Circuit Board Design
Best PCB design method: Six things to consider when selecting PCB components based on component packaging. All the examples in this artICle were developed in the MultiSIM design environment, but even if different EDA tools are used, the same concept still applies.
1. Consider the selection of component packaging
In the whole schematic drawing phase, the component packaging and pad pattern decisions that need to be made in the layout phase should be considered. Here are some suggestions to consider when selecting components based on component packaging.
● Remember that the package includes the electrical bonding pad connection and mechanical dimensions (X, Y and Z) of the component, that is, the shape of the component body and the pins connecting the circuit board. When selecting components, you need to consider any installation or packaging restrictions that may exist on the top and bottom layers of the final circuit board. Some components (such as polar capacitors) may have high headroom restrictions, which need to be considered in the component selection process. At the beginning of the design, you can draw a basic outline shape of the circuit board, and then place some large or location critical components (such as connectors) that you plan to use. In this way, you can see the virtual perspective of the circuit board (without wiring) intuitively and quickly, and give relatively accurate relative positioning and component height of the circuit board and components. This will help ensure that the components of the circuit board can be properly placed into the outer packaging (plastic products, chassis, frame, etc.) after assembly. Call 3D preview mode from the Tools menu to browse the whole circuit board.
● The pad pattern shows the actual pad or via shape of the soldered components on the circuit board. These copper patterns on the circuit board also contain some basic shape information. The dimensions of the pad pattern need to be correct to ensure correct welding and the correct mechanical and thermal integrity of the connected components. When designing the layout of the circuit board, it is necessary to consider how the circuit board will be manufactured, or how the bonding pad will be welded if it is manually welded. Reflow soldering (flux melting in a controlLED high-temperature furnace) can handle a wide range of surface mounted devices (SMDs). Wave soldering is generally used to solder the reverse side of the circuit board to fix through hole devices, but it can also handle some surface mounted components placed on the back of the circuit board. Usually, when using this technology, the bottom surface mounting devices must be arranged in a specific direction, and in order to adapt to this welding method, the pads may need to be modified.
● The selection of components can be changed in the whole design process. It will be helpful for the overall planning of the circuit board to determine which devices should use electroplated through-hole (PTH) and which should use Surface Mount Technology (SMT) early in the design process. Factors to be considered include device cost, availability, device area density and power consumption. From the manufacturing point of view, surface mounted devices are generally cheaper than through hole devices, and generally have higher availability. For SMAll and medium-sized prototype projects, it is better to select larger surface mount devices or through hole devices, which is not only convenient for manual welding, but also conducive to better connection of bonding pads and signals during error checking and debugging.
● If there is no ready-made package in the database, it is generally to create a customized package in the tool.
2. Use good grounding method
Ensure that the design has sufficient bypass capacitance and ground plane. When using integrated circuits, make sure to use appropriate decoupling capacitors near the power supply end to the ground (preferably the ground plane). The proper capacity of the capacitor depends on the specific application, capacitor technology and operating frequency. When the bypass capacitor is placed between the power supply and ground pins and close to the correct IC pin, the electromagnetic compatibility and susceptibility of the circuit can be optimized.
3. Assign Virtual Element Packages
Print a bill of materials (BOM) for checking virtual components. The virtual component has no relevant package and will not be transferred to the layout stage. Create a bill of materials and view all virtual components in the design. The only items should be power and ground signals, because they are considered as virtual components, which are only processed in the schematic environment and will not be transmitted to the layout design. Unless used for simulation purposes, components displayed in the virtual part should be replaced by components with encapsulation.
4. Make sure you have complete bill of materials data
Check whether there is enough complete data in the bill of materials report. After the bill of materials report is created, it is necessary to carefully check and complete the incomplete component, supplier or manufacturer information in all component entries.
5. Sort according to the component label
To facilitate the sorting and viewing of the bill of materials, ensure that the component labels are numbered consecutively.
6. Check the redundant door circuit
In general, all redundant gate inputs should have signal connections to avoid the input end hanging in the air. Make sure that you have checked all redundant or missing gate circuits, and that all non wired inputs are fully connected. In some cases, if the input is in the suspended state, the whole system cannot work correctly. Take the dual op amp that is often used in design. If only one of the dual op amp IC components is used, it is recommended to either use the other op amp, or ground the input end of the unused op amp, and lay a suitable unit gain (or other gain) feedback network to ensure that the entire component can work normally.
In some cases, ICs with floating pins may not work properly within the indicator range. Generally, only when the IC device or other gates in the same device are not working in the saturation state - the input or output is close to or in the component power rail, can the IC meet the index requirements when working. The simulation usually cannot capture this situation, because the simulation model generally does not connect multiple parts of the IC together to model the suspension connection effect
然后
聯(lián)系
電話熱線
13410863085Q Q
微信
- 郵箱