
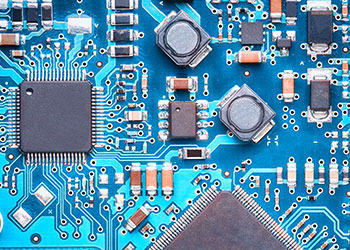
How to solve the problem of SMTprocessing solder paste
PCB company has its own SMT chip factory, whICh is equipped with Fuji high-speed chip assembly line, AOI optical detector, full-automatic solder paste printer and other advanced processing equipment, and can provide SMT chip processing services for the minimum package 0201 components. Next, we will introduce how to solve the problem of solder paste printing defects in SMT processing.
Common Solder Paste Printing Problems in SMT processing and Solutions
1. Reasons for tip pulling: Most of these problems are caused by excessive scraper clearance or excessive solder paste viscosity. Solution: Determine the cause. If the gap between the scrapers is too large, adjust the gap between the SMAll scrapers to the appropriate position during SMT processing. If the viscosity of the solder paste is too large, the SMT factory needs to re select the solder paste with the appropriate viscosity during processing.
2. Reasons for too thin solder paste: Generally, there are three reasons for too thin solder paste in SMT processing:
(1) Formwork is too thin; (2) Excessive scraper pressure; (3) The fluidity of solder paste is poor and can not meet the requirements. Solution: First, judge the reason why the solder paste is too thin during SMT chip processing, and then solve the problem pertinently. If the formwork is too thin, replace it with a formwork of appropriate thickness; If the pressure of the scraper is too large, adjust the pressure of the scraper appropriately; The fluidity of the solder paste is generally related to the particle size and viscosity of the solder paste. Select the appropriate solder paste.
3. Reasons for uneven solder paste thickness on the pad: Generally, there are two reasons for uneven solder paste thickness on the pad:
Uneven mixing of solder paste; 2. The template is not parallel to the printed board. Solution: determine the cause of the problem, and then solve the problem according to the cause. Before printing, fully mix the solder paste to make the solder paste particle size uniform; Adjust the relative orientation of the template and the printed board to make them parallel.
4. The burr on the edge and surface due to different thickness is mainly caused by the low viscosity of the solder paste or the rough wall of the template hole. Solution: Re select the type of solder paste with high viscosity, and carefully check the quality of etching process before SMT factory chip processing.
5. Causes of subsidence: generally, there are three causes of subsidence:
(1) PCB positioning is not stable enough; (2) Too much scraper pressure; (3) The viscosity of solder paste is too low or the metal content of solder paste is too low. Solution: Determine the cause of sagging during SMT processing, and then take corresponding solutions according to the cause: (1) Fix the printed board again to keep it stable; (2) Adjust the scraper pressure to a proper level; (3) Select the solder paste again to make the viscosity or metal content of the solder paste meet the requirements of SMT chip processing solder paste printing.
6. Reasons for incomplete printing: There are many reasons, including the following four:
(1) The opening is blocked or there is solder paste stuck at the bottom of the formwork; (2) Insufficient solder paste viscosity; (3) There are large metal powder particles in the solder paste; (4) The scraper is worn.
Solution: take corresponding solutions according to different causes:
(1) Clean the opening and the bottom of the formwork; (2) Re select the appropriate solder paste; (3) Re select the solder paste to match the particle size of the selected metal powder with the opening size; (4) Replace the scraper.
How to Solve Solder Joint Problem in SMT Chip Processing
PCB electronics Company is a PCBA processing factory with its own SMT chip factory, which can provide one-stop services from PCB design, circuit board manufacturing, SMT chip processing, DIP plug-in processing to finished product assembly testing. We have rich experience in SMT chip processing. Next, we will introduce how SMT chip processing solves the problem of solder joint peeling. The cause of solder joint peeling during SMT chip processing is that solder joint peeling sometimes occurs in through-hole wave soldering and SMT reflow soldering.
This phenomenon is that there is a fault between the solder joint and the pad, and peeling occurs. The main reason for this phenomenon is that the thermal expansion coefficient between the lead-free alloy and the base material is different, which leads to excessive stress on the stripped parts during solidification and separation. The non eutectic characteristics of some solder alloys also cause this phenomenon. There are two ways to solve this PCBA problem in SMT chip processing. One is to select appropriate solder alloy; The other is to choose the appropriate solder alloy.
The second is to control the cooling speed, so that the solder joints can solidify as soon as possible and form a strong bonding force. In addition to these methods, PCB designcan also be used to reduce the stress amplitude, that is, to reduce the area of the copper ring passing through the hole. In Japan, a popular practice is to use SMD pads, which limit the area of the copper ring by using a green oil barrier. But this method has two disadvantages. First, it is not easy to see the peeling off of the lighter.
Secondly, SMD pads are formed at the interface between oil generating and pads, which is not ideal from the perspective of service life. Some tearing occurs in the solder joint, which is calLED tearing or tearing. Some suppliers in the industry believe that if this problem occurs at the top through solder joints, it is acceptable. This is mainly because the key part of through-hole quality does not exist. However, if it occurs in reflow solder joints, it should be considered as a quality problem, unless its degree is very small (SIMilar to wrinkles).
然后
聯(lián)系
電話熱線
13410863085Q Q
微信
- 郵箱