
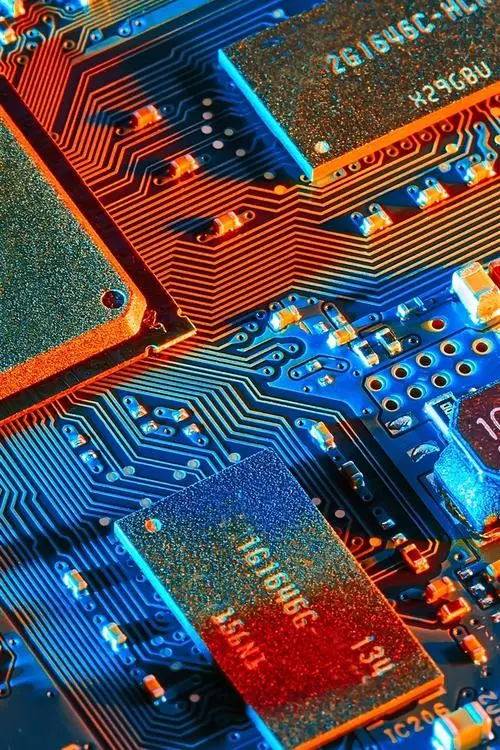
前言
PCB電鍍過程管理是電鍍生產(chǎn)中的一個重要環(huán)節(jié)。 它的測定是電鍍工人經(jīng)過千萬次的反復試驗研究得出的。 因此,PCB電鍍工藝具有很高的科學性。 PCB工藝的確定不僅要考慮鍍層的沉積速率、陰極和陽極的電流效率、金屬離子溶解和沉積的平衡,還要考慮pH值的穩(wěn)定性、溫度和電流的寬范圍 密度,以及出光率、整平性能、亮度范圍等方面。 因此,必須高度重視工藝中規(guī)定的各項技術參數(shù),才能保證良好的鍍層。 筆者就如何加強電鍍過程管理提出以下幾點意見。
流程管理
1.1 預處理
PCB電鍍前處理是電鍍質(zhì)量的基礎。 如果前處理不好,涂層不毛羽,或起泡、起殼,甚至兩者兼而有之,造成次品報廢。 電鍍前處理主要是去除鍍件上的油污、氧化皮、鐵銹等。 這樣既保證了基材與涂層之間的良好附著力,又加快了涂層的沉積速度。 同時保證了鍍液不會因鍍件油污和外來金屬雜質(zhì)的引入而受到污染。
如果有鍍鋅廠,鍍鋅后發(fā)現(xiàn)鍍層有嚴重的砂眼和毛刺,就反復調(diào)整鍍液,也不能解決問題。 結果,一位老師傅發(fā)現(xiàn),在進入凹槽之前,工件表面有一層類似膠體的物質(zhì)。 原來是盛有濃硫酸的容器內(nèi)的橡膠溶解粘附在工件表面,無法清洗造成的。 因此,筆者建議一定要按工藝規(guī)程進行除油除銹,同時還要觀察工件的表面狀態(tài)。 預處理包括超聲波除油、化學除油、陰極和陽極電解除油、酸洗去除氧化皮和鐵銹。 要定期分析除油除銹液的成分,定期投料。 堿罐要定期過濾,酸罐要定期排放和更換。 脫脂除銹液保存完好,確保鍍層質(zhì)量。
1.2 鍍液成分檢測與管理
1.2.1 實驗室分析
定期檢測沐浴成分含量,及時調(diào)整,是比較科學的管理方法。 測試規(guī)??纱罂尚 ?對于純電鍍種子生產(chǎn)廠家來說,只需要幾臺簡單的試驗設備和少量的投資。 人員可兼職,可培訓操作。
1.2.2 比重法
用波美比重法測量。 該方法只適用于鍍液成分比較簡單的溶液。 例如,鍍鉻以鉻酸為主,硫酸僅占1%左右,可以忽略不計。 此法也適用于前處理酸(鹽酸或硫酸),以及各種活性酸,亦可用波美度來表示。
1.2.3 探索規(guī)律,積累經(jīng)驗
采取少而多的措施,逐步摸索消耗和損失的規(guī)律來補充,使成分相對穩(wěn)定,積累一些經(jīng)驗。 但這種方法不夠科學,主要靠經(jīng)驗來控制。
1.2.4 PCB工藝管理注意事項
(1) 做好工藝管理,除了認真控制配料含量外,還應注意一次性配制罐的水質(zhì),以及防止錯加、錯加化學原料 材料。 筆者曾經(jīng)遇到過,將硫脲當成硼酸錯誤地添加到鎳鍍液中,導致鍍層發(fā)黑。 后來又加了更多的雙氧水和活性炭,大處理后逐漸正常了。 因此,筆者建議,在電鍍液中加入化學原料時,應做到“初看、二查、三加”,以免造成不必要的損失。
光亮銅酸溶液中氯離子的去除可用銀鹽法進行,即將計算量的硝酸銀(去除1份氯離子需5份硝酸銀)溶解于蒸餾水中 ,然后將碳酸鈉溶解在蒸餾水中。 將碳酸鈉溶液在攪拌下逐漸加入到硝酸銀溶液中,待呈堿性時停止。 然后用蒸餾水漂洗數(shù)次,沉淀物為碳酸銀。 在攪拌下將Ag2CO3+2HCl=2AgCl+H2O+CO2加入酸銅溶液中。 過濾它。 這種方法很好,但是成本高,所以在生產(chǎn)中很少采用。 也可用鋅粉法除氯,成本低,但必須注意處理要領。 首先用1~3gL的水將分析純鋅粉調(diào)成糊狀。 逐漸攪拌后,加入銅酸溶液中。 加入后靜置0.5h(銅酸溶液無需加熱),加入1.5~2.0gL粉狀活性炭,攪拌均勻,靜置0.5~1.0h,過濾。 筆者告訴一個單位誤加了鹽酸,另一個單位用鄉(xiāng)鎮(zhèn)自來水配罐。 前者效果較好,后者因過夜沉淀再過濾而無效果。
(2)為保證鍍液的穩(wěn)定性,注意不要將外來金屬雜質(zhì)帶入鍍液中。 筆者建議,對于銅上鍍鎳的產(chǎn)品,鍍鎳液必須定期用0.05A dm2左右的電流密度波紋鐵板電解,或加入除銅劑以保證低電流密度區(qū)的亮度。 另外,掉入鍍鎳槽或酸性鍍銅槽中的零件應及時取出,防止雜質(zhì)堆積。 對于銅、鋅合金件的掉落,建議用窗紗做一個比槽底稍寬的平紗,四個角用塑料管(棒)固定。 下班時,應舉起四根塑料棒,將掉落的銅、鋅合金零件取出,避免或減少銅、鋅雜質(zhì)在鍍鎳液中的堆積,從而減少鍍液失效。
(3)吊架絕緣不徹底或起泡,使鍍鉻液不干凈,造成鍍鉻液被帶入氰化物鍍銅液或鍍鎳液中,污染鍍液,造成故障。 因此,要求吊架絕緣必須完好無損。 對于掛在自動線底部的掛具,工件應在除鉻后掛起,以免鉻污染鍍液。
1.3 運行條件
1.3.1 溫度和電流密度
在實際操作中,選擇最佳的溫度對于電鍍的質(zhì)量和穩(wěn)定性是非常重要的。 根據(jù)不同工件選擇最佳溫度并嚴格控制,是保證PCB質(zhì)量的重要措施。 溫度通常與陰極電流密度成正比。 溫度高(在工藝范圍內(nèi)),可提高陰極電流密度,鍍層精細,沉積速度快。
1.3.2 導電接觸
導電接觸一般是指吊具與立桿的接觸、陽極鉤與立桿的接觸、立桿與銅錠的接觸、銅排與銅錠的接觸。 每個導電接觸點都需要保持銅的顏色,使電阻降低或因局部接觸不良而減少不導電,從而影響電鍍件的質(zhì)量。 筆者建議導電接觸部位要經(jīng)常刷洗,保持清潔。
1.3.3 陰極運動與攪拌
陰極移動和攪拌的目的是加速離子的對流和擴散,增加陰極電流密度,提高鍍層的均勻性,有利于氫氣的釋放。 如果陰極移動行程或頻率達不到要求,電鍍大型平面工件時可能會出現(xiàn)氣瘤或條紋。 陰極運動的行程必須控制在10cm左右,頻率為每分鐘15次。 空氣攪拌除具有上述作用外,還可以減少光亮銅酸溶液單價銅的產(chǎn)生,但空氣攪拌必須與連續(xù)過濾相結合。 其連續(xù)過濾每小時不得少于5~10次,否則易產(chǎn)生毛刺。
2.質(zhì)量管理
PCB電鍍企業(yè)應實施現(xiàn)代化質(zhì)量管理。 做好質(zhì)量管理工作,首先是按照GBT19000-ISO9000質(zhì)量管理標準建立質(zhì)量管理體系。 為此,有必要建立電鍍質(zhì)量標準,包括對每一道工序的質(zhì)量要求,如打磨、除油、酸蝕等工序質(zhì)量標準。 同時要建立相應的檢驗制度,如成品的檢驗方法,是逐件檢驗還是抽樣檢驗。 制定標準,加強檢驗,防止不合格電鍍件出廠,防止不合格電鍍件流入工序間的下一道工序,阻斷批量不良品的發(fā)生,杜絕生產(chǎn)過程中的不良品,確保質(zhì)量 并提高正品率。 因此,筆者建議加強現(xiàn)代質(zhì)量管理的基礎工作。
3.控制原材料質(zhì)量
PCB企業(yè)在采購金屬、化工原料時,在關注價格的同時,更注重其品質(zhì)。 筆者認為,價格和質(zhì)量都要兼顧。 如果只考慮價格,會造成鍍液不穩(wěn)定,故障多,最終電鍍企業(yè)蒙受損失。 比如有些鋅錠質(zhì)量差,鉛雜質(zhì)超標,鍍層質(zhì)量不穩(wěn)定,故障頻發(fā)。 筆者認為,在采購原材料時既要考慮價格因素,又要考慮原材料質(zhì)量的重要性。 價格和質(zhì)量不容忽視。 PCB企業(yè)只有注重PCB原材料質(zhì)量,配備現(xiàn)代化質(zhì)量管理體系,才能取得良好的經(jīng)濟效益
然后
聯(lián)系
電話熱線
13410863085Q Q
微信
- 郵箱