
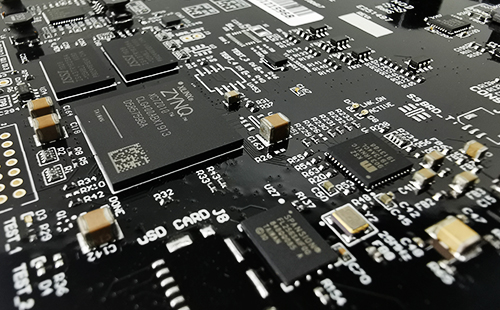
How to choose a reliable PCB processing factory
Now it is easy to find an electronIC processing factory, but it is not easy to find a reliable electronic processing factory. What conditions should a reliable pcb processing factory have? In the process of factory review, we can pay attention to the following points:
1. Quality Management System QM
1.1 Is the quality management system certified and planned by a third party? (Conform to ISO9001, TS16949 or other internationally recognized quality management systems)
1.2 Is there a documented quality manual that describes in detail the scope, structure, and interaction between system processes of the quality management system?
1.3 Is there a documented quality policy that has been effectively communicated and understood at all levels of the organization?
1.4 Does the supplier have a management representative who has the responsibility and authority to ensure that the quality management system is introduced, implemented and maintained?
1.5 Does each department of the company establish clear and measurable quality objectives? And regularly review the achievement of objectives and take improvement actions?
1.6 Is there a risk management system to identify, analyze and control various potential risks?
1.7 Is there an emergency procedure to prevent loss as much as possible in case of emergency? Formulate corresponding measures and exercise plans and conduct regular exercises.
1.8 Is there a documented procedure that specifies the responsibilities and requirements for audit planning, implementation, reporting audit results and record keeping?
1.9 Is the internal audit standard, audit scope, frequency and method defined?
1.10 Does the supplier conduct internal review at planned intervals?
1.11 Does the selection of internal auditors and the conduct of internal audit ensure that the internal audit process is objective and fair? (For example, the auditor is not allowed to audit the work content of the department.)
1.12 Are the nonconformities reviewed last closed within the specified time? Whether the improvement measures are effective (the nonconformities do not occur again)?
1.13 Is the audit report recorded and communicated with the company's leadership?
1.14 Are internal auditors qualified?
1.15 Does the supplier conduct management review on the effectiveness and adaptability of the quality management system at appropriate intervals (such as: the quality system meets customer requirements)?
1.16 Are management review input items confirmed?
1.17 The output of management review shall include any decisions and measures related to the following aspects:
Improvement of quality management system and its process effectiveness
Improvement of products related to customer requirements
Resource requirements.
1.18 Is the implementation of measures from management review tracked?
1.19 Are management review records maintained?
2. Document Control SCM
2.1 The Supplier has established and documented the following procedures:
Quality Manual
Procedures supporting the quality system are defined in the quality manual
design documents and technical specifications/drawings?
Process control documents?
Work instructions?
Audit documents?
2.2 Have procedures and work instructions been consistently and effectively implemented?
2.3 Are there any documents that define the design documents/technical specifications, drawings/process control documents/procedures and the preparation guidelines of work instructions in detail?
2.4 Is there a document control procedure to ensure that valid versions of applicable documents are available where they are used?
2.5 Are there procedures to ensure that documents are clear and easy to identify?
2.6 Are there procedures to ensure that external documents are identified and distributed under control?
2.7 Is there a procedure to ensure that all obsolete documents are withdrawn from the distribution site in a timely manner?
2.8 If obsolete documents are retained for any reason, are there procedures to ensure that these documents are properly identified?
2.9 If paperless documents are used, is there a system to ensure that the version, identification, storage and distribution of documents are well controlLED?
2.10 Are quality documents fully reviewed and approved by authorized personnel before issuance?
2.11 Is the service life and control process of temporary documents (such as handwritten documents) defined?
3. Design and Development RD
3.1 Is a documented product development process established to standardize the planning, process, control, etc. of product development?
3.2 Are plans prepared and responsibilities clarified for each design project? Is the plan updated as the design work progresses?
3.3 Is the input and output review of product development conducted to ensure the integrity of input and output data?
3.4 Is the design and development verified and confirmed to ensure compliance with input and customer requirements?
3.5 Is there a procedure to identify, document, review and approve design and development changes and modifications?
3.6 Are records of design control, review, verification and validation activities properly documented and maintained?
3.7 Whether DFMEA analysis has been conducted for new product development, and whether corrective measures have been taken for risks with high risk priority value (RPN)?
3.8 Is the production process verified to ensure the stability of mass production?
3.9 Is the formal written approval of the customer obtained before mass production? Are physical samples and records kept well?
3.10 Are important process parameters clearly specified? Are the actual parameters consistent with the specifications?
3.11 Are process parameter records saved? Is there an authorized person to deal with any abnormality in time?
3.12 Are customer data managed effectively? (Acknowledgment, drawings, etc.)
3.13 Is there a procedure to manage engineering changes?
3.14 Are engineering changes reviewed and approved by authorized personnel before implementation?
3.15 Once approved, are engineering changes distributed to all affected functional areas?
3.16 Is there a system to ensure that ECNs are implemented?
3.17 Is there a system to ensure that engineering changes are implemented only after the necessary training/tools and equipment are ready and the work instructions are updated?
3.18 Is there a system to verify and feedback the effectiveness of engineering changes?
4. Supplier Development and Management SCM
4.1 Is there a procedure document to specify the selection and evaluation of suppliers? Are there alternative suppliers for key components?
4.2 Are there procedures and checklists for quality system audit and in-process quality analysis?
4.3 Are only materials from qualified suppliers used? Is AVL effectively maintained and regularly updated?
4.4 Is there an annual supplier audit plan, and has the supplier been audited according to the plan?
4.5 Is the price, quality, technology and service of the sub suppliers evaluated regularly?
4.6 Whether to feed back the evaluation results and exceptions to suppliers and urge them to improve?
4.7 Is there a mechanism to ensure that all customer requirements are met and properly documented, and that these requirements have been communicated to sub tier suppliers?
4.8 Is there a sample approval procedure (such as mold approval, product approval, etc.)?
4.9 Whether agreements on quality and hazardous substances have been signed with suppliers?
4.10 Is there a procedure for improvement and elimination of the manufacturer with poor evaluation?
4.11 Are inspection/test records/reports reviewed and approved by authorized personnel for product release?
4.12 If there is a nonconforming Lot, whether to send a Quality Improvement Request (CAR) to the supplier and require the supplier to reply to the corrective measures within the specified time and verify the effectiveness of the corrective measures?
4.13 Are records provided to prove that the product has passed the inspection and/or test of defined acceptance standards?
5. Quality inspection and testing QM
5.1 Is there a documented process definition inspection and test method that meets the product specification?
5.2 Does the supplier ensure that the incoming materials will not be used and processed before being inspected and verified to meet the specified requirements?
5.3 Does the supplier inspect, test and identify products according to the quality plan or documented procedures?
5.4 Does the supplier carry out the first inspection, final inspection and test?
5.5 Does the supplier have extended reliability/safety test using rules? (e.g. drop/vibration, EMI, reliability, safety regulations, etc.)
5.6 Can the inspection and test process ensure that the delivered products meet the customer's objectives?
5.7 Is there a procedure describing product inspection and test status?
5.8 Is there a procedure and actual operation to ensure the traceability of products at all stages of production?
5.9 Are product inspection or test qualified and unqualified conditions identified? (Use MARKs, labels, inspection records, test software, object location, etc.)
5.10 Is there a system to ensure that only materials passing the specified inspection or test can be used and sold?
5.11 Are records provided to prove that the product has passed the inspection and/or test of the defined acceptance standard?
5.12 Is GR&R implemented before mass production or after process change?
5.13 Are standard parts/sheaths available for inspection/testing?
5.14 Are standard parts/sheathing plates properly identified (part number, version, serial number), inspected and stored?
5.15 Are inspection/test records/reports reviewed and approved by authorized personnel for product release?
5.16 Does the coverage of supplier testing meet the minimum requirements of customers?
5.17 Are tests established sufficiently and adequately to ensure product quality? (e.g. hardware, equipment, software/version, fixture, etc.)
6. Correction RD
6.1 Is there documented process control inspection, measurement and test equipment? Including: "General Equipment List", "Calibration Interval", "Calibration Schedule", "Recycling List", "Calibration Record/Report"
6.2 Is the calibration conducted under specified environmental conditions?
6.3 Is there a document defining how to deal with equipment that fails verification?
6.4 Is the equipment verified or recalibrated at appropriate intervals?
6.5 Is the measuring equipment protected from unauthorized adjustment or readjustment?
6.6 Is there a formal approved control system for all equipment to determine accuracy and precision?
6.7 Is the school free equipment clearly marked?
6.8 Is the reference device (standard equipment) used for benchmark calibration (zero point, manufacturer's scale, etc.) correctly stored, managed and calibrated according to American measurement standards?
6.9 For internal calibration, is there a general standard to describe the sufficient capacity of (instrument/equipment) (such as resolution of more than 10 times)?
6.10 Is there an appropriate method to store measuring equipment, tools and jigs?
6.11 When it is found that the requirements are not met, is the measuring and testing equipment recalibrated?
6.12 If it is found that the equipment does not meet the calibration requirements, is there a process to dispose of the products that have been manufactured/tested?
6.13 Have the personnel in charge of calibration been trained and formally certified?
The above is how to choose a reliable PCB processing factory as explained by PCB design, PCB manufacturing and PCB processing factory.
然后
聯(lián)系
電話熱線
13410863085Q Q
微信
- 郵箱