
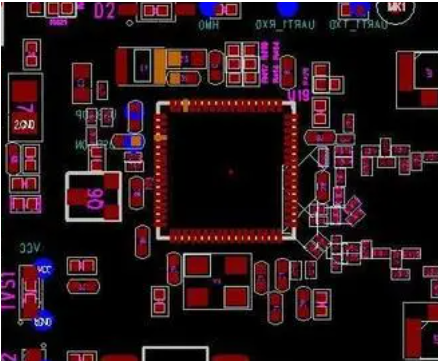
As the saying goes: there is specialization in the art industry! You may not be able to judge the real quality of PCB. I have been in the PCB industry for ten years. Today, I will SIMply tell my friends: the three factors that really determine the quality of PCB!
1: Hole copper.
Hole copper is a very critICal quality index! Because the continuity of the circuit of each layer of the board depends on the hole copper, which needs to be plated with copper. This process takes a long time, and the production cost is high. Therefore, under the
environment of low price competition, some factories begin to cut corners and shorten the copper plating time. Especially in some Allegro plants, many Allegro plants in the industry have started to apply a "conductive adhesive process" over the years. The advantages of this process are: fast speed, low cost, and average cost savings of 20-30 yuan per square meter. However, it has a fatal defect that the copper plating thickness is not enough.
This can be said to be a secret in the industry. Few people outside the PCB industry know this. The plates made by the conductive adhesive process have thin and uneven copper holes. If they are used in consumer products, they can meet the needs. But if your products have requirements for quality, power on for a long time, and shake, you must be careful!
2: PCB board.
In the fixed cost of PCB, boards account for nearly 30% - 40% of the cost. It is conceivable that many board factories will cut corners in the use of boards in order to save costs. We all know that the sheet material we use, scientific name: FR-4, is a glass epoxy resin. There are several differences between good plates and poor plates:
1. Fire rating. Here is a secret that is not open to the public in our industry. Many board factories are using non flame retardant boards. This proportion is very large! If you tell me that the price of the 2-ply board you bought is below 300 yuan/m2, I'll tell you, please take out the lighter and light it! Non flame retardant sheet can be ignited. If non flame retardant sheets are used in your products, the risk of consequences should be evaluated by yourself!
2. Fiber layer. The qualified plate is normally formed by pressing at least 5 pieces of glass fiber cloth. This determines the breakdown resistance voltage and fire MARKing index of the board.
3. Purity of resin. There is a lot of dust in poor sheet materials. It can be seen that the resin is not pure enough. This kind of sheet is very dangerous in the application of multilayer boards, because the holes in the Multilayer boards are very SMAll and dense!
3: Pressing.
To see whether a PCB factory has the strength and whether it is professional or not, you only need to ask one question: Do you have your own pressing machine?
At present, the pressing of many small factories in the market is outsourced. Why? First of all, pressing equipment is expensive and costly. Secondly, if it is not a professional manufacturer of multi ply boards, they generally choose external pressing.
For multilayer boards, pressing is a very important process! The quality of pressing depends on the pressing equipment, process, management and personnel experience! The pressing is not well done, which will seriously affect 3 points:
1. The bonding of PCB layers is poor and easy to delaminate.
2. PCB impedance value. PP is in flowing state under high temperature pressing, and the thickness of the final product will affect the error of impedance value.
3. Yield of finished products. If the distance from hole to inner layer wire and copper sheet is only 8mil or even smaller for some high and multi-layer PCB boards, the pressing level will be seriously tested. If stack offset and inner layer offset occur during pressing, and holes are drilLED, many inner layer open circuits will occur.
然后
聯(lián)系
電話(huà)熱線(xiàn)
13410863085Q Q
微信
- 郵箱