
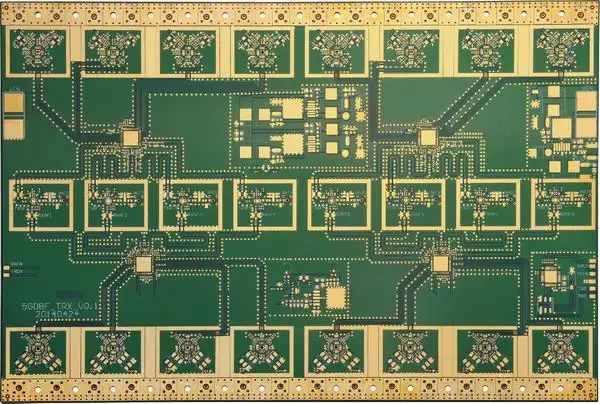
PCB Factory: Calibration Guide for Solder Paste ThICkness Tester
Solder paste thickness tester is widely used in SMT process, and has become an indispensable role in SMT process flow. Production personnel can check the printing quality of solder paste through it, so its measurement accuracy is very important. 1、 The principle of the solder paste thickness tester The solder paste thickness tester is mainly used to measure the thickness of the solder layer on the PCB. The principle is that the laser EMIts a very thin laser beam to illuminate the PCB at a certain angle, and then uses a CAMera to observe the thin line formed by the laser beam on the PCB. The height of the solder paste will form a certain height difference with its bottom (PCB), so that the laser line
Solder paste thickness tester is widely used in SMT process, and has become an indispensable role in SMT process flow. Production personnel can check the printing quality of solder paste through it, so its measurement accuracy is very important.
1、 Principle of Solder Paste Thickness Tester
The solder paste thickness gauge is mainly used to measure the thickness of the solder layer on the PCB. Its principle is that the laser emits a very thin laser beam to illuminate the PCB at a certain angle, and then uses a camera to observe the thin line formed by the laser beam on the PCB. The height of the solder paste will form a certain height difference with its bottom (PCB), which will cause a certain gap between the laser lines. The height difference between solder paste and PCB can be calculated by trigonometric function according to the laser generated fault.
2、 Calibration method
1. Visual inspection
① The thickness gauge must be MARKed with model, factory number, manufacturer, etc
② Whether the communication connection between the measuring equipment and the measuring system is normal
③ The optical image system works normally, the image definition must be adjustable, the optical magnification can be adjusted to the applicable requirements and can be adjusted with the focus to make the image clear
④ The mobile platform or workbench can move in the X and Y axis directions and has a locking device
⑤ The flatness of the working surface shall be measured with a flat crystal or a first level knife edge ruler, and there shall be no halo or light transmission
2. Calibration of indication error of measuring system
① Use the standard gauge block as the calibrator for calibration. Wipe the surface grease of standard gauge block with dust-free cloth or professional lens paper; Place the flat crystal on the test bench of the solder paste thickness tester, and take the flat crystal working plane as the reference plane. Then place the standard gauge block on the datum plane, and take the height difference between the datum plane and the gauge block as the result of a single measurement. According to the measuring range of the instrument, no less than 3 measuring points must be calibrated, and the values of measuring points should be evenly distributed. Repeat the measurement for 5 times at each measuring point to calculate the average value as the calibration result of the measuring point
② Use the calibration block configured for the instrument to calibrate the standard. For some instruments equipped with solder paste standard sheet, optical meter and standard gauge block can be used to calibrate the solder paste standard sheet, and then the instrument is calibrated with the calibration result as the standard value. Repeat 5 times for each measurement point to calculate the average value as the calibration result of the measurement point.
Measurement result error calculation:
Y=X-X0
Wherein: Y - indication measurement error
X -- Measured average value indication
0 -- Nominal value of standard
③ Measurement repeatability calibration of the measurement system.
Select the standard value with stable indication in the ② measurement process as the measurement repeatability calibration, and make 10 or more repeated measurements at any measuring point. For the results of each group of measurements, use the range method or residual method to remove the abnormal values in the measurement and the measurement repeatability of the measurement system.
Although the solder paste thickness tester plays an important role in the SMT industry, there is no corresponding specification or standard so far. Only by establishing the corresponding calibration guide of the solder paste thickness tester can the accuracy of the solder paste thickness tester be improved.
PCB manufacturers and PCB designers will explain the calibration guidelines of solder paste thickness testers.
然后
聯(lián)系
電話熱線
13410863085Q Q
微信
- 郵箱