
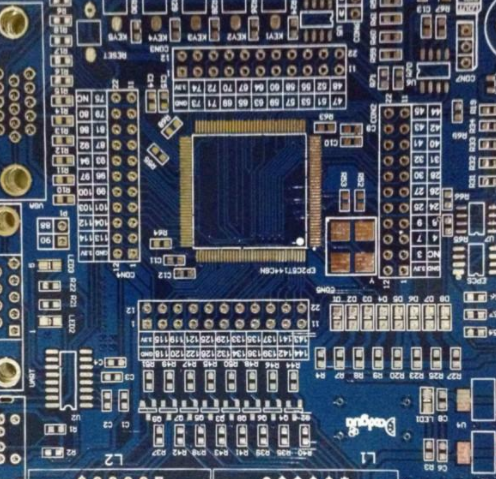
How to Enhance the ESD Function of PCB
In the design of PCB board, the anti-statIC design of PCB can be realized by layering, and the correct layout and installation can be achieved During the design process, most design modifications can be limited to adding or removing components through prediction ESD can be well protected by adjusting PCB layout Static PCB copy power from human body, environment and even internal PCB copy sub equipment will cause various damages to precision transistor chips, such as penetrating the thin insulation layer inside the module; Destroy the gate of MOSFET and CMOS components; The trigger in the copy board of the CMOS device PCB is locked; Short circuit of reverse biased PN junction; PN junction of positive PCB copy board is short circuited to offset; PCB copy board melts the welding wire or aluminum wire of PCB copy board in active equipment In order to eliminate the interference and damage to electronic equipment caused by electrostatic discharge (ESD), various scientific and technological measures need to be taken to prevent it In the design of PCB board, the anti-statIC design of PCB can be realized through the layering and proper layout of PCB copy board and PCB copy board wiring and installation During the design process, most design modifications can be limited to adding or removing components through prediction By adjusting the PCB layout and wiring, the PCB copy board can well prevent electrostatic discharge Here are some common precautions
PCB board
Try to use multi-layer PCB Compared with double-sided PCB, the ground plane and power plane, closely arranged signal line ground spacing can reduce the common mode impedance and inductive coupling to 1/1 double-sided PCB 10 to 1/100. Try to keep each signal layer close to the power layer or ground plane For high-density PCB with components on the top and bottom surfaces, with very short interconnects, and many ground fillers, consider using an inner layer For double-sided PCB, tightly interwoven power supply and grounding grid shall be used The power cord is close to the ground wire, and as many connections are made between the vertical and horizontal conductors or pads as possible The size of one side grid PCB copy board is less than or equal to 60mm If possible, the grid size should be less than 13 mm Ensure that each Circuit PCB copy board is as compact as possible Place all connectors aside as far as possible. If possible, route the power PCB through the center of the card and away from the area directly affected by electrostatic discharge Place wide chassis grounds or polygon-filLED grounds on all PCB layers below the connectors leading out of the chassis (easy PCB copy boards are directly hit by ESD) and connect them with vias at intervals of about 13mm together. Place the mounting hole of the PCB copy board on the edge of the card, and connect the top and bottom pads of the PCB copy board with non blocking flux to the main housing around the mounting hole for grounding During PCB assembly, do not use any solder on the top or bottom PCB pads Use screws with embedded PCB washers to achieve close contact/mask or ground plane support between the PCB and the copy of the metal main housing PCB The same "isolation zone" shall be set between chassis grounding and circuit grounding of each layer; If possible, maintain a separation distance of 0.64 mm On the top layer and bottom layer of the card near the mounting hole of the PCB copy board, connect the chassis grounding and circuit grounding with 1. Lay 27mm wide lines every 100mm along the chassis grounding wire Close to these connection points, place a bonding pad or mounting hole for installation between the chassis grounding and the circuit grounding PCB These ground connections can be cut with a blade to keep them open, or with ferrite bead jumpers/high-frequency capacitors If the circuit board will not be placed in the metal host shell or PCB copy board mask device, the grounding wires on the top and bottom chassis of the circuit board should not use solder resist. In addition, they can be used as the discharge electrode of the electrostatic discharge arc
To set a ring ground around the circuit in the following PCB layout:
(1) Except that the edge is connected to the PCB copying device and the chassis ground
(2) Make sure that the annual width of all layers is greater than 2.5 mm
(3) Connect the rings with via holes every 13mm.
(4) Connect the ring ground to the common ground of the multi-layer PCB copy board circuit.
(5) For double sided PCB copy boards installed in metal chassis or shielding devices, the ring ground should be connected to the circuit common ground For unshielded double-sided circuits, the ring ground should be connected to chassis ground Solder resistance flux shall not be used for ring grounding. In summary, ring grounding can be used as the discharge rod of ESD Place at least one place on the ring ground (all layers). 0.5 mm wide gap to avoid PCB forming a large loop The distance between signal line and ring grounding shall not be less than 0.5mm
然后
聯(lián)系
電話熱線
13410863085Q Q
微信
- 郵箱