
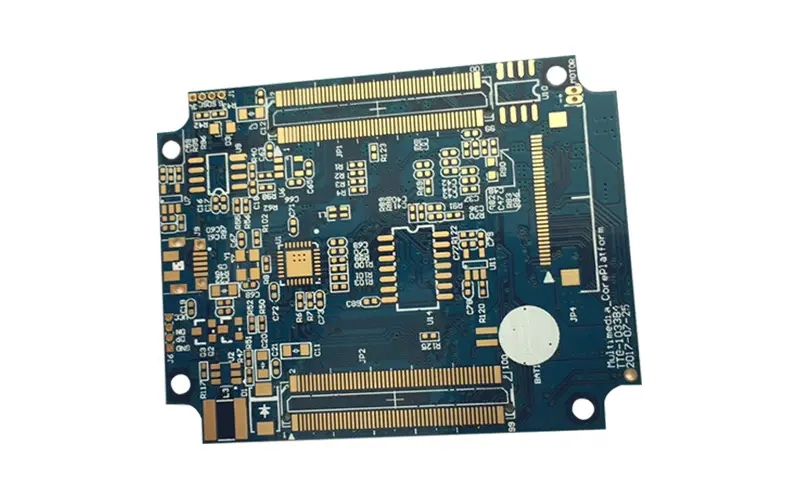
Distinguish PCB dry film and wet film and new energy vehICle charging post PCB
PCB manufacturers, PCB designers and PCBA manufacturers explain how to distinguish PCB dry film and wet film and new energy vehicle charging post PCB
When PCB is made in a circuit board factory, one of the processes requires the use of dry film and wet film. In fact, the functions of dry film and wet film are basically SIMilar. However, if the surface is uneven or it is not necessary to establish a thick height or a very thin film thickness, circuit board manufacturers can consider the use of wet film. If it is a circuit board with holes, the dry film will be more suitable. If the environment is not easy to keep clean, it is easier to control the quality of the dry film operation. Although the material of wet film is relatively cheap, it is not available everywhere. In addition to general considerations, the use should still be considered in accordance with the requirements of the manufacturer's own operating environment.
2. Dry film is easy to operate, but the unit price is slightly higher than that of wet film. However, because it is easy to keep clean and does not need to be baked, it has better workability, so it is more beneficial to use. But for thin film thickness, especially 15 μ Dry film thickness below m is not easy to achieve. In addition, the better filling capacity of the wet film is its advantage, but because there is no protective film, it requires higher exposure energy. Different views have different advantages and disadvantages, which must be carefully compared by the user to obtain a more suitable conclusion.
3. At present, the so-calLED wet film is almost always used in the welding paint. As for the application in the inner layer board, the proportion of wet film is getting higher and higher, because of the low cost and the gradual improvement of technology maturity. But both in the production of inner PCB.
Which circuit board is used for the charging pile of new energy vehicles
Since the emergence of new energy vehicles, the demand for charging piles has been increasing day by day. Many manufacturers or merchants are preparing to install or produce charging piles themselves to obtain a wave of new energy business opportunities. Many merchants have begun to pay attention to their charging piles, and the circuit boards used by charging piles have become their first targets.
The circuit board of the charging pile is generally thick copper circuit board with more than four layers, and the copper thickness is usually more than 1.6. The main reason is that the circuit board of the charging pile has large current and high voltage, and the thin plate cannot bear it. Because the circuit board of the charging pile is a high-voltage power board, although it is made of copper in materials, there are also some differences in grades. The common board materials are below the common TG140, the circuit board materials of the charging pile are generally above the medium TG150, and the high TG is 170. The data are grade parameters. The higher the grade, the better the temperature resistance effect and the higher the quality of the plate.
However, the circuit board itself needs high current and high voltage, so it can be used as the impulse discharge test standard for the battery. The design of the circuit board is particularly important. It is necessary to consider not only the charging pile, but also the demand voltage of the car. Unreasonable design may cause the circuit board to burn.
The charging pile is a supporting type product around the car, and it is not allowed to have damaged lines, or have residual copper on the side of the lines, or have yellow solder resistance on the side of the holes. Some customers implement IPC-III standards and zero defect acceptance specifications, which are much more strict than general consumer PCB boards.
Although the charging pile is a hot industry, the competition is also fierce, and the review of the charging pile is also extremely strict. Therefore, during the production process of the core accessories of the charging pile, we must find a powerful circuit board manufacturer, such as the circuit board, which is the core component that carries the operation of the entire system. Therefore, its importance can be imagined. The quality of the charging pile circuit board must be strictly controlled.
PCB manufacturers, PCB designers and PCBA manufacturers will explain how to distinguish PCB dry film and wet film and new energy vehicle charging post PCBs
然后
聯(lián)系
電話熱線
13410863085Q Q
微信
- 郵箱