
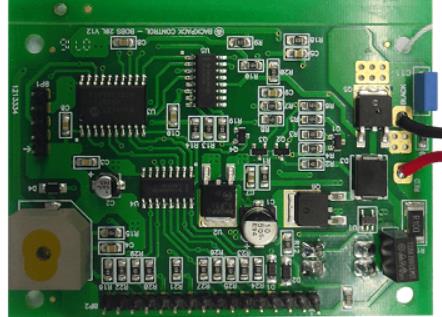
Faults related to lead-free PCBA and nozzles made of lead-free PCBA
PCB manufacturersusually have two manufacturing technologies for SMT Chip Manufacturing, one is lead-free PCB manufacturing process, and the other is lead manufacturing technology. Everyone knows that lead is harmful to people. Therefore, lead-free manufacturing technology meets environmental requirements, whICh is the trend of the times
1. Alloy composition is different: 63/37 of tin lead component in lead-free alloy is common, namely SAC305, Sn: 96.5%, Ag: 3%, Cu: 0.5%. Lead free manufacturing technology cannot guarantee lead free absolutely. Only SMT patches have very low lead content, such as lead below 500PPM.
2. Different melting points: lead tin melting point 180 ~ 185, working temperature 240 ~ 250, lead-free tin melting point 210 ~ 235, working temperature 245 ~ 280. According to experience, the melting point will increase every time the tin content increases by 8% - 10%
3. Different costs: tin is more expensive than lead. When SMT chip manufacturers convert solder of equal importance to tin, the cost of solder will increase significantly. Recall that the cost of lead-free manufacturing technology is much higher than that of lead-free manufacturing technology. Statistics show that no matter peak welding or manual welding, lead-free manufacturing technology is 2.7 times of lead-free manufacturing technology. The cost of solder paste for reflow soldering has increased by about 1.5 times.
4. PCB manufacturers have different manufacturing technologies: this can be seen from the names of lead manufacturing technology and lead-free manufacturing technology, but when it comes to manufacturing technology, it refers to the solder, components and equipment used, such as wave soldering patch furnaces, solder paste printers, hand soldering irons, etc.
Polychlorinated biphenyls
Each stage of the placement process must be repeated and must not fail, and a careful review of these processes identified the following five major issues related to improper nozzle maintenance and/or the use of inferior nozzles.
Vacuum loss, vacuum loss may be the cause of some problems, because it blocks the nozzle to pick up parts from the feeder. It may also cause parts to move on the nozzle during transport. One of the main reasons for SMT manufacturers to lose less suction and vacuum power is that they cannot maintain the nozzle quality during the manufacturing process. The quality and structure of the nozzle must match its designed parts. Another problem associated with vacuum loss is poor pickup position on the part. Poor quality nozzles may cause additional fatigue to the pickup because they must constantly adapt to the environment to maintain efficiency.
Short circuited or worn nozzles, short circuited or worn nozzles may cause poor pickup and may cause parts not to be properly embedded in solder. When the part is not placed correctly in the solder, the replacement equipment does not have enough surface tension to maintain the part when moving the PCBA. The part moves on the plate. One advantage of monitoring nozzle head length is that it allows for regular preventive maintenance. Prevent quality problems caused by nozzle tip.
The wear of the nozzle tip will also lead to a decrease in the vacuum, which will lead to the fall or displacement of electrical components during transportation. New developments in ceramics, electrostatic discharge data and special coatings enable nozzle manufacturers to design nozzles with excellent durability and toughness, especially when operating under extreme conditions.
The above is the explanation given by the editor of pcb circuit board company.
If you want to know more about PCBA, you can go to our company's home page to learn about it.
In addition, our company also sells various circuit boards,
High Frequency Circuit Board and SMT chip are waiting for your presence again.
然后
聯(lián)系
電話熱線
13410863085Q Q
微信
- 郵箱