
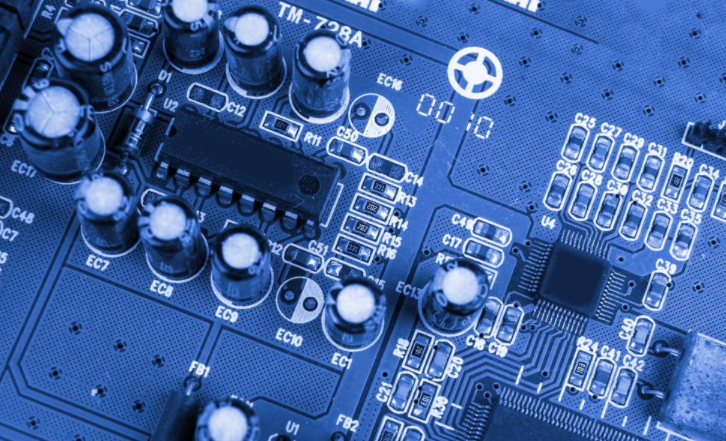
AOI inspection of DIP components before peak welding operation
Dip packaging (dual in line package), also known as two-wire online packaging technology, refers to that the manufacturer of integrated circuit chip PCBA packaged in the form of two-wire serial connection in DIP processing belongs to PCB board Now most SMAll and medium-sized integrated circuits use this packaging method, and the number of pins generally does not exceed 100; Dip packaged CPU chips have two pins, whICh need to be inserted into chip sockets with dip structure or directly inserted into PCB boards with the same number of welding holes and geometric layout of welding
Impregnated package chips must be inserted carefully from the chip socket to avoid SMT technicians damaging the pins during handling. DIP packaging structures include: multi-layer ceramic double line DIP, single-layer ceramic double line DIP, lead frame DIP (including microcrystalline glass seal, plastic packaging structure, ceramic low melting glass packaging), etc.
Automatic optical inspection
Post processing welding of DIP chip is a process after SMT chip processing (except for special cases: PCB boards with only DIP chip). The processing flow is as follows:
1. Component pretreatment
The workers in the pre processing workshop will pick out the materials in the BOM according to the BOM bill of materials, carefully check the type and specification of the materials, sign, pre process according to the model before production, and use the automatic bulk capacitor foot shearing machine and other molding equipment for processing, transistor automatic molding machine and automatic belt molding machine.
requirement:
(1) The pin leveling width of the adjusting part must be the same as that of the locating hole, with a tolerance less than 5%;
(2) The distance between component pin and PCB pad should not be too large;
(3) If required by the customer, molded parts are required to provide mechanical support to prevent PCB pad warping.
2. Paste high temperature adhesive tape, enter the PCB board to paste high temperature adhesive tape, block the tin plated through-hole and the components that must be welded on the back;
3. The DIP parts processing workers must wear electrostatic bracelets to prevent static electricity. Parts shall be processed according to the BOM of parts and components and the dot matrix diagram of parts and components. Smt tip handling operators must be careful not to make mistakes or leaks when inserting.
4. The operator must check the inserted parts, mainly to check whether they are inserted incorrectly.
5. For PCB boards with no problems, the next step is wave soldering. Wave soldering can be used to weld omnidirectional automatic PCB boards and curing components.
6. Remove the high-temperature adhesive tape and check it. In this link, the main step is to visually check whether the welded PCB is well welded.
7. For PCB boards that are not completely welded after inspection, repair them to prevent problems.
8. Post welding is a set of procedures for parts with special requirements, because according to its own process and data limitations, some parts cannot be directly welded by the peak welder, which needs to be manually completed by the operator.
9. For all component PCB circuit board pads on the, this PCB needs to perform a function test after the test. PCB bonding is completed to test whether each function is in a normal state. If a defective function is detected Workers need to identify pending process PCB boards immediately before repair and retest
然后
聯(lián)系
電話熱線
13410863085Q Q
微信
- 郵箱