
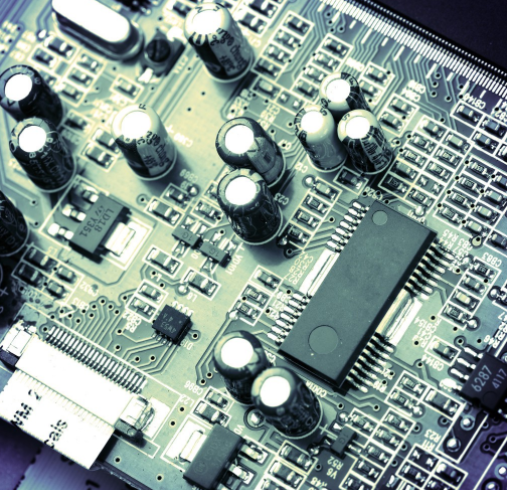
Analysis of the influence of SMT on reflow quality
Reflow soldering is one of the key processes of surface mounting, and the result of reflow soldering directly reflects the quality of surface mounting However, the welding quality problems in reflow soldering are not entirely caused by the reflow soldering process, because the quality of reflow soldering is not only directly related to the temperature curve, but also related to the equipment conditions of the production line, the productivity design of PCB pads, and the solderability of components performance, solder paste quality, PCB processing quality and process parameters of each process of surface mounting are closely related to the operating habits of operators
(1) The influence of production materials on reflow quality.
1. Impact of components. When the welding end or weld leg of the component is oxidized or contaminated, welding defects such as poor wetting, faulty soldering and voids will occur during reflow soldering. Poor coplanarity of components can also lead to welding defects, such as virtual welding during welding.
Circuit board
2. Impact of PCB The assembly quality of SMT has a direct and very important relationship with PCB pad design Whether the PCB pad design is correct, due to the surface tension of molten solder, a SMAll amount of tilt during installation can be corrected during reflow soldering; On the contrary, if the PCB pad design is incorrect, even if the installation position is very accurate, on the contrary, after reflow soldering, welding defects may occur, such as component position deviation and tombstone formation The quality of PCBA components is also related to the quality of PCB pads When PCB pad is oxidized, it is polluted or wet, and there are welding defects, such as poor wetting, false soldering, and solder balls. Voids will appear during reflow soldering
3. The influence of solder paste. The content of metal powder in solder paste, the oxygen content of metal powder, viscosity, thixotropy and printability have certain requirements. If the metal powder content in the solder paste is high, when the reflux temperature rises, the metal powder will splash as the solvent evaporates. If the oxygen content of the metal powder is high, it will aggravate the spatter, form the solder ball, and cause defects such as non wetting. In addition, if the viscosity of the solder paste is too low or the thixotropy of the solder paste is poor, the solder paste pattern will collapse after printing, or even cause adhesion, and welding defects such as solder balls and bridges will be formed during reflow soldering. If the printing suitability of the solder paste is not good, the solder paste will only slide on the template during the printing process, and the solder paste will not be printed at all. If the solder paste is taken out of the freezer and used directly, it will cause condensation. When the reflux temperature rises, the water vapor will evaporate and carry out the metal powder. At high temperatures, water vapor will oxidize metal powders and splashes to form solder balls, whICh will also lead to problems such as poor wetting.
Surface mounting and patch processing 012
(2) Influence of production equipment on reflow quality. The quality of reflow soldering is closely related to the production equipment. The main factors affecting reflow quality are as follows:
1. Printing equipment. The printing accuracy and repeatability of the printer will play a role in printing results, and ultimately affect the quality of reflow soldering; The quality of the template will eventually affect the printing result, that is, the welding quality. The thickness of the template and the size of the opening determine the number of solder pastes to be printed. Too much solder paste will lead to bridging, and too little solder paste will lead to insufficient solder or faulty soldering. The shape of the template opening and whether the opening is smooth will also affect the printing quality. The opening of the template must be flared downward, otherwise the solder paste will remain on the chamfer of the flared opening when demoulding.
2. Reflow soldering equipment. The temperature control accuracy of reflux furnace shall reach ± (0.1 ~ 0.2) Y; The transverse temperature difference of the conveyor belt of the reflux furnace should be less than ± 5Y, otherwise it is difficult to ensure the welding quality; The width of the conveyor belt of the reflux furnace shall meet the requirements of the maximum PCB size; The longer the heating zone in the reflux furnace is, the more the number of heating zones is, and the easier it is to adjust the temperature curve. For medium and small batch production, 4 to 5 temperature zones are selected, and the heating zone is about 1.8 meters long, which can meet the requirements. The upper and lower heaters shall have independent temperature control to adjust and control the temperature curve; The maximum heating temperature of reflux furnace is generally 300-350. Considering lead-free solder or metal substrate, you should choose 350 dragons or more; The conveyor belt of the reflux furnace shall run smoothly and vibrate. It leads to welding defects, such as displacement, tombstone, cold welding, etc.
然后
聯(lián)系
電話熱線
13410863085Q Q
微信
- 郵箱