
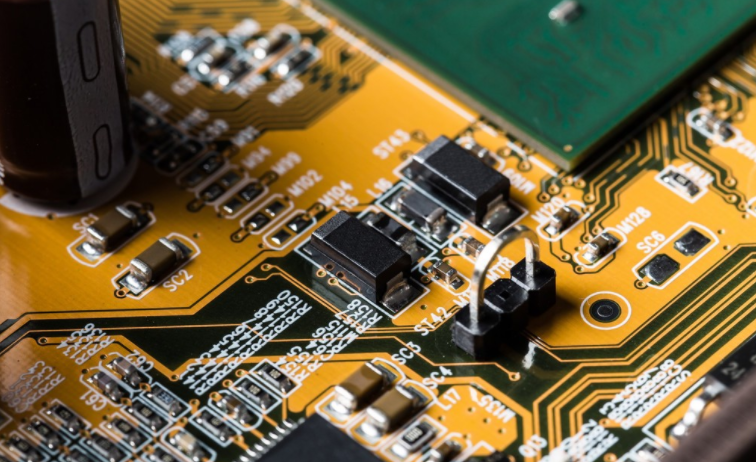
SMT processing test of various test technologies
Comparison of test capabilities of various test technologies PCBA processing
AOI and AXI mainly carry out visual inspection, such as bridging, dislocation, excessive solder joints and SMAll solder joints, but they cannot check the equipment itself and circuit effICiency. AXI can detect hidden solder joints of BGA and other devices, as well as invisible defects such as bubbles and cavities in solder joints.
ICT and flying probe test focus on circuit function and component performance test, such as solder joint, open circuit, short circuit, component failure, error data, etc., but cannot measure defects such as low tin content and high tin content. ICT testing speed is fast, suitable for mass production occasions; For high assembly density, small lead spacing and other occasions, flying pin test is required.
The current PCB is very complex when it has SMDs on both sides At the same time, equipment packaging technology is more and more advanced, and the shape is often the size of the bare chip These are used to detect PCBA board circuit A circuit board with more solder joints and equipment cannot be free from defects All the detection methods described above have their own test characteristics and applications, but none of them can completely detect all the defects in the circuit, so two or more detection methods are required
SMT Keyboard Patch Handling
1)AOI+ICT
Circuit board
The combination of AOI and ICT has become an effective tool for production process control. The use of AOI has many advantages, such as reducing the labor cost of visual inspection and ICT, avoiding ICT becoming the bottleneck of new production capacity, even canceling ICT, and shortening the production cycle of new products.
2) AXI+function test
Replacing ICT with AXI inspection can maintain a high functional test output rate and reduce the burden of fault diagnosis. It is worth noting that AXI can detect many structural defects that can pass ICT inspection, and AXI can also detect some defects that cannot pass ICT inspection. At the same time, although AXI cannot detect power defects in the components, these defects can be detected in the functional test. In short, this combination does not omit any defects in the manufacturing process. Generally speaking, the larger and more complex the board of directors, or the more difficult the exploration, the greater the economic return of Asi.
3)AXI+ICT
The combination of AXI and ICT technology is ideal. One technology can make up for the shortcomings of the other.
AXI is mainly committed to testing the quality of solder joints. ICT can determine the direction and value of components, but cannot determine whether solder joints are acceptable, especially under the packaging of large surface mount components.
By using a dedicated AXI layered detection system, the number of nodes required can be reduced by 40% on average. The reduction of ICT points reduces the complexity and cost of fixtures and also reduces false positives. The use of AXI also increased the one-time pass rate of ICT departments by 20%. Generally, after the shape memory alloy is welded, the command rate cannot reach 100%, and some defects will appear more or less. Some defects are surface defects, which will affect the surface appearance of the solder joint and will not affect the function and life of the product. According to the actual situation. Determine whether maintenance is required; However, some defects, such as dislocation and bridging, will seriously affect the function and life of the product. Such defects must be repaired or reworked.
The above is the explanation given by the editor of PCB circuit board company.
If you want to know more about PCBA, you can go to our company's home page to learn about it.
In addition, our company also sells various circuit boards,
High Frequency Circuit Board and SMT chip are waiting for your presence again.
然后
聯(lián)系
電話熱線
13410863085Q Q
微信
- 郵箱