
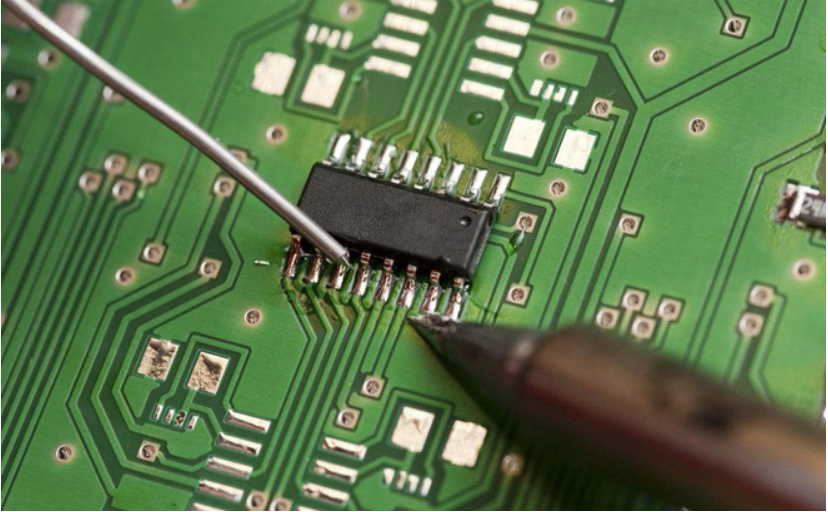
BasIC information of special chEMIcals for PCB photoresist
Dry film photoresist is a kind of film photoresist that is uniformly coated on the carrier polyester film (PET film) by a pre prepared liquid photoresist on a precise coating machine and under the condition of high cleanliness. After drying and cooling, it is coated with polyethylene film (PE film) and rolLED into rolls.
The dry film photoresist of the circuit board is pressed on the copper clad plate, and the circuit pattern on the negative (mask plate or negative plate) is copied to the dry film photoresist through exposure and development. Then, the copper clad plate is etched using the anti etching performance of the dry film photoresist to form a fine copper circuit of the PCB printed circuit board. The performance of dry film photoresist is mainly determined by the chemical composition of the photoresist layer.
Dry film photoresist layer is composed of three main chemicals: resin, photoinitiator and monomer. As a film-forming agent, the resin can bond each component of the photoresist to form a film. The resin is required to have good mutual solubility with each component, have good adhesion with the processed metal surface, be easy to remove from the metal surface with alkaline solution, and have good corrosion resistance, electroplating resistance, cold flow resistance, heat resistance and other properties.
Photoinitiators absorb UV light of a specific wavelength (generally 320-400nm) and then self decompose to produce free radicals, which further lead to the cross-linking of photopolymer monomers. Photoinitiators play a decisive role in the performance of dry film photoresist, such as sensitivity, exposure time tolerance and deep curing. With the continuous progress and change of light source technology, and the increasing requirements of customers for the photosensitivity of dry film photoresist, the requirements for the type, chemical structure, performance and quality of photoinitiators are also changing.
The function of optical imaging solder resist ink is to prevent short circuit caused by solder bonding, form a permanent protective layer of the circuit, and ensure the safety and electrical performance invariance of PCB board in production, transportation, storage and use. Photoimaging solder resist ink is one of the key materials in PCB manufacturing. In the 1960s, the first generation of solder resistance -- two-component thermosetting solder resistance accelerated the development of PCB industry. Subsequently, in order to adapt to the change of MARKet demand, after continuous improvement and updating, the second generation of solder resist, namely, UV curable solder resist, appeared and was widely used. In recent years, in order to meet the needs of manufacturing high-density PCB, the third generation of solder resist, namely liquid light imaging solder resist ink, has been developed. Its main components are epoxy resin, monomer, prepolymer, photoinitiator (including photosensitizer), pigment, etc. Since the structure of prepolymer includes both photopolymerization and thermal crosslinking groups, fine patterns with high registration accuracy can be obtained through exposure and development, After heating and cross-linking, the solder mask is more compact and smooth, and its physical and electrical properties, such as heat resistance and insulation, are better. It is currently the mainstream application product. Photoinitiators play an important role in imaging performance.
This article introduces the basic situation of PCB photoresist special chemicals industry in the development of PCB industry
然后
聯(lián)系
電話熱線
13410863085Q Q
微信
- 郵箱