
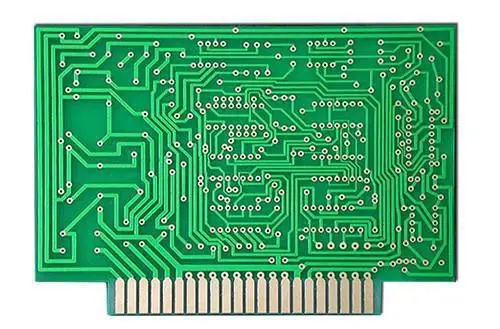
Methods of Preventing Welding Porosity in PCBA Factory
Bubbles are generally generated during reflow and wave soldering of SMT chip processing. Bubbles will not only affect the beauty of PCBA, but also affect the quality of our products. So what is the method of PCBA factory to prevent welding porosity in production? The following is a brief introduction by the circuit board manufacturer.
1. Baking
PCBA substrates and components that have not been used for a long time and are exposed to air may have moisture. Bake them after a period of time or before use to prevent moisture from affecting PCBA processing.
2. Solder paste
Solder paste is also very important for the processing of PCBA factory, and if the solder paste contains water, it is easy to produce such undesirable phenomena as pores or solder beads during welding.
In the selection of solder paste, we should not cut corners. We must select high-quality solder paste, and before using solder paste, we must strICtly follow the processing requirements for mild mixing and other processing processes. In the early PCBA processing, it is better not to expose the solder paste to the air for a long time. After printing the solder paste in the SMT chip processing link, it is necessary to seize the time for reflow soldering.
3. Workshop humidity
The humidity of the processing workshop is also a very important environmental factor for PCBA processing, which is generally controlLED at 40-60%.
4. Furnace temperature curve
Carry out furnace temperature detection in strict accordance with the standard requirements of the electronic processing factory, and optimize the furnace temperature curve in a planned way. The temperature of the preheating zone shall meet the requirements, so that the flux can be fully volatilized, and the speed of furnace passing cannot be too fast.
5. Flux
During wave soldering in PCBA processing, the flux shall not be sprayed too much.
然后
聯(lián)系
電話熱線
13410863085Q Q
微信
- 郵箱