
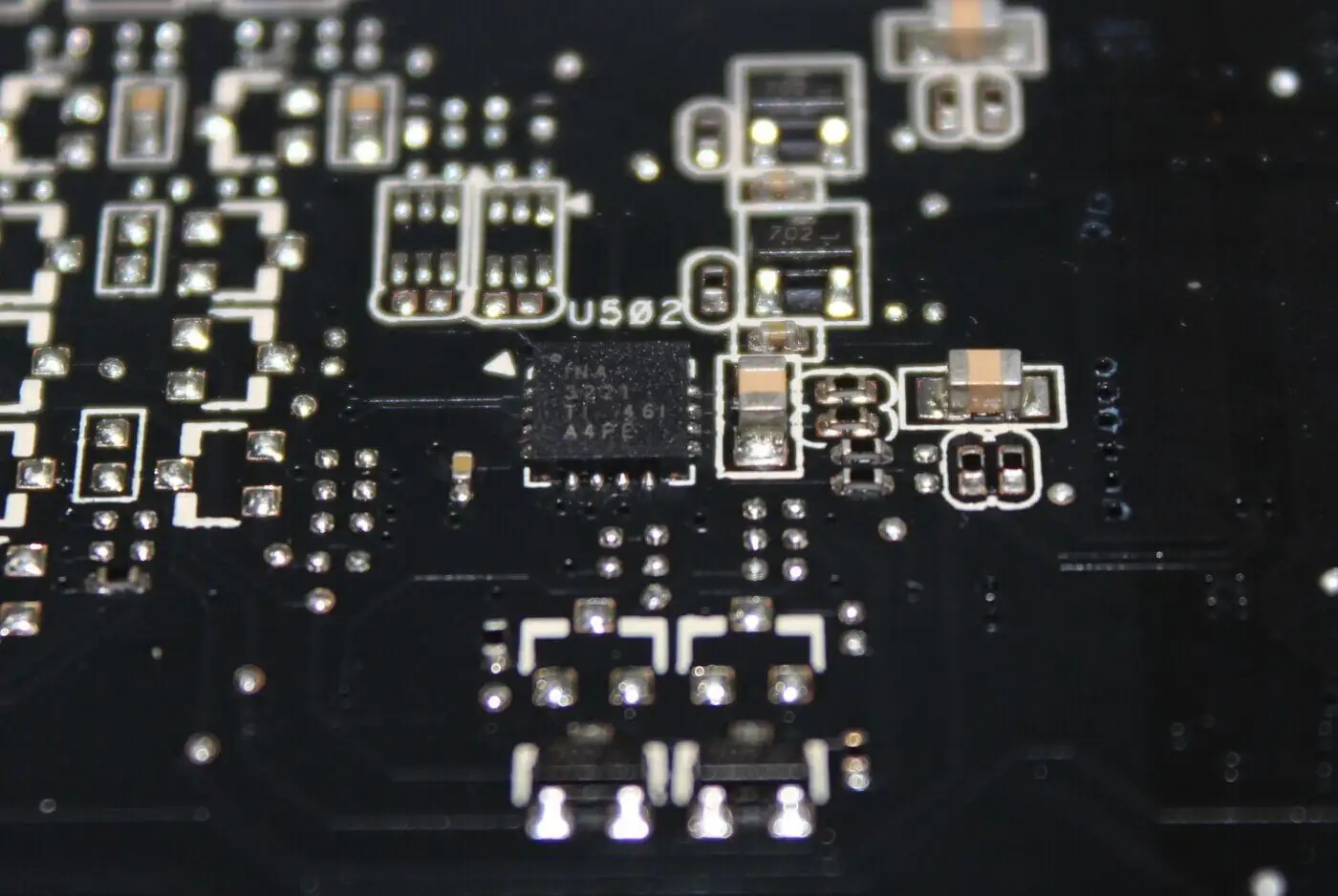
Precautions for PCBA assembly process flow
1、 Purpose
Standardize the key process methods and requirements for PCB production, ensure the stability and accuracy of PCBA assembly process, and avoid man-made damage and unnecessary rework caused by improper assembly process and operation method, so as to ensure quality and improve production effICiency!
2、 Scope of application
All PCBAs provided by the Company to customers.
3、 Precautions for PCBA assembly process
The following procedures shall be followed when assembling finished products:
Warehouse → production line → production line upgrade software (* note) → assembly of complete machine → QC test → write IMEI number → QA full inspection → restore factory settings → warehousing (station settings may vary depending on the model, according to customer project or engineering guidance). If the software needs to be upgraded before assembly, it is not allowed to assemble the finished machine and then upgrade the software. It may not be upgraded due to improper welding, short circuit, operation process problems, etc., and the assembly plant misjudges that PCBA is defective.
4、 Upgrade before assembly
1 When PCBA needs to be upgraded, there are items that need to be changed in the process of mainboards. Mainboards of normal batches in different time periods cannot be mixed with afterMARKet mainboards to avoid mixing boards due to changes in mainboard hardware. The assembly plant confirms with the customer whether the software is the final software required by the customer
2. In the mobile phone upgrading work area, the operators should wear electrostatic rings and take other anti-static measures.
3. To prevent errors in upgrading and writing IMEI numbers, please use the professional tools provided by our company to download upgrading tools and write IMEI numbers.
4. When the mobile phone is upgraded, the power supply voltage cannot exceed 4.2V. In order to avoid the high voltage causing the cell phone motherboard to be burned, resulting in high current when the phone is not turned on. The software should be matched with the font library to avoid not starting up after upgrading or causing other abnormalities. Before production, it shall be debugged in advance to teach the operators how to be artificial. For production.
5. Whether the upgrade is formatted (in principle, the upgrade is not formatted. If the PCBA calibration file is formatted and upgraded, it will be lost, resulting in a series of problems such as no signal, weak signal, etc.), unless the customer specifically tells the customer to format the upgrade, the assembly plant will format the upgrade software again. (Note: The project manager is required to confirm this problem with the customer before trial production and mass production, and inform our company and technical support personnel by phone, email, etc.). Before production, the identification of the PCBA outer packaging box must be checked: the software and hardware versions are consistent with the software and hardware versions to be produced, and different versions must be distinguished from each other; If the old version needs to be upgraded before it is put into production, the production line engineers should arrange the upgrade according to the above requirements before it is put into production. * Note: For those that do not need to be upgraded, confirm whether the software and hardware versions meet customer requirements.
5、 Notes on assembly
1. The whole stay wire must have anti-static function, and each operator is required to wear electrostatic ring.
2. Tools such as welding tools and tweezers must have anti-static function.
3. The operation station area shall be clean and free of sundries to avoid scratches, oil and dust on the main board.
4. The operator shall take the edge of the machine board or wear anti-static gloves to avoid gold finger prints on the main board, so as to avoid the poor function of a key after installation or in the hands of the user.,.
5. Before assembling the whole machine, if there are fingerprints and dirt on the golden finger, wipe the fingerprints and dirt with a dust-free cloth and alcohol once to avoid poor function of a key after installation or oxidation in the user's hand.
6、 Requirements for welding and maintenance station
1. Electrostatic protection detection: all static ground wires shall be connected to the ground wire (the DC resistance from the ground ground point to the end of each pull wire shall be measured quarterly, which shall be less than 10 ohms), and shall not be connected to the power ground; Personnel exposed to PCBA must wear wired electrostatic bracelets, electrostatic clothes and shoes. Before wearing the electrostatic bracelet, check the electrostatic bracelet to ensure that it is a good product. Cordless electrostatic ring does not have the function of discharging static electricity. It is prohibited to purchase and use it! Measure the surface resistance of the anti-static table surface every quarter, which is between 9 and 10 to the 10th power.
2. Solder iron detection: leakage detection: measure the voltage between the shell of the soldering iron and the ground wire with the AC voltage of the multimeter. The voltage should be less than 3V, indicating that the soldering iron is well grounded to ensure that the soldering iron does not leak. The welding position shall be equipped with an ion fan, which shall be turned on during welding. Soldering iron temperature shall be measured with a soldering iron temperature tester in each shift: (the temperature of electric soldering iron at welding stations such as motor, horn, wire, etc. is 330 ± 10 ℃ (with lead), 350 ± 10 ℃ (without lead), the welding time is controlLED within 2~3s, and the special stations are implemented according to the operation instructions or the requirements of technicians. LCD screen welding station, the welding temperature is 350 ± 20 ℃, and the tin dragging welding time is controlled within 6s.
3. PCBAs at all posts shall not be stacked on top of each other. PCBAs shall be handled with care when they are taken and placed, and boards shall not be thrown away to prevent PCBAs from being deformed or damaged, materials from being knocked off, pads from falling off, etc.
4. Finger cots should be worn for special posts (all gold plated components that touch gold fingers and reed contacts, such as PCBA, key board, motor with reed, receiver, horn, headphone socket, antenna thimble, antenna); When taking the PCBA, try to use your fingers to take the edge of the PCBA board.
Precautions and inspection during welding:
1. No tin tip or excessive tin shall be left.
2 Flux containing conductive components shall not be used to avoid poor contact and short circuit caused by residual after welding and environmental changes during use.
3. No false welding is allowed during welding (causing abnormal function)
4. The welding station shall not have the main board stacked (to avoid dropping parts or the main board dropping pads)
5. During welding, too much flux should not cause oxidation of the main board and malfunction.
6. Soldering shall be free of tin (to avoid poor function of mobile phone)
7. Operators must pass the self inspection before entering the next operation link.
7、 Paste key film
1. Wear rubber finger cots during operation (replace them every 2-4 hours, or replace them when they are removed from the fingers and are no longer used). Do not touch the gold finger keys and the DOME keys with bare hands.
2. The dust-free cloth shall be replaced in time according to the actual situation (generally 2H replacement)
3. Do not use too much force to clean the golden finger of the key to avoid damaging the PCBA.
4. The keyboard membrane positioning hole and the PCBA positioning hole (or the key FPC) should correspond one by one
5. The key film must be pasted flat without wrinkles. The grounding ear should be folded according to the requirements of the operation instructions and pasted on the corresponding grounding copper foil. It should not exceed the edge of the PCBA.
6. When the main board is closed, the internal wires of PCBA must be placed according to the process, and the opening handle must be moved to align with the button clamping position before closing the shell. Avoid breaking wires and pulling the switch head handle, or causing the main board to deform.
7 The conductive foam is pasted at the correct position according to the customer's model and the customer's prototype to avoid the surrounding components, so as to avoid short circuit of components and poor function of the main board.
The above basic manufacturing process should be strictly followed by the assembly plant to avoid PCBA damage and function and appearance damage due to poor operation; Operation methods of other aspects The assembly plant shall arrange by itself according to its own conditions.
8、 Analysis and treatment of defective PCBA
1. If the function is poor, it should be analyzed and confirmed by the professional maintenance personnel or technicians of the Circuit board manufacturer first. If the assembly process is poor (components are damaged during assembly, soldering is connected, false soldering, and assembly is not in place), the production and technical personnel should implement control;
2. If it is confirmed that the PCBA is defective, remove the peripheral components of the PCBA directly within 2% (2% does not include the cumulative number of defective motherboards in multiple batches) of the single batch of motherboards with defective functions to avoid soldering copper foil, tin bonding of other components, false soldering, and lack of parts, and mark each defective PCBA as defective. For the missing parts without copper foil and complete bonding pad, within 2% of the defective plates, they shall be repaired free of charge (limited to SMAll materials). If this ratio is exceeded, the repair cost shall be 10 yuan/piece based on the component cost+maintenance labor cost. The motherboard without damage and poor function shall be repaired free of charge according to normal after-sales service.
If the assembly plant causes that the mainboard cannot be repaired due to copper foil falling or deformation, the assembly plant shall scrap the mainboard itself. The statistical quantity shall be returned every 50~200PCS (according to the unit quantity and the cleaning progress), so that we can carry out maintenance in a timely manner.
3. After confirming that the function defect exceeds 2%, we will directly notify our project or technical support factory to analyze the cause of the defect and provide a long-term solution in a timely manner.
然后
聯(lián)系
電話熱線
13410863085Q Q
微信
- 郵箱