
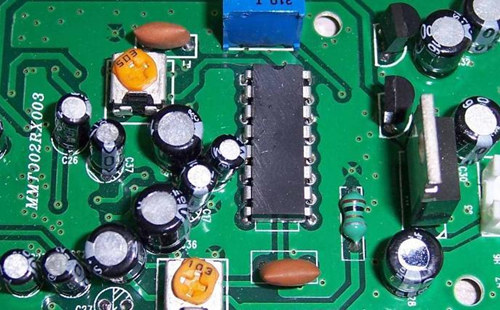
How to implement PCBA quality standards? And PCBA workshop management
Almost all electronIC processing manufacturers will implement the PCBA quality standard, namely IPC-A-610, to control the quality of PCBA production. Of course, PCBA quality standards are sometimes only for reference, and electronic processing participates in formulating more detaiLED standards based on customer requirements.
1. ElectronIC components: when components are purchased, components and materials should be purchased from the correct channels to ensure processing quality;
2. Automatic optical detection: ensure PCBA surface defect inspection during production, such as scratches and stains, open circuit, short circuit, solder thinning and missing parts, incorrect parts, and incorrectly placed components;
3. Manual visual inspection: conduct manual inspection between the production process and the last step. Particular attention is given to controlling the correct placement and placement of all components and the proper wetting of solder.
4. PCBA function test: function test is used as the final manufacturing step to SIMulate the product operating environment. It provides a pass/fail determination before the finished PCBA leaves the factory. The manufacturing purpose is to verify that the product hardware is free from defects, otherwise it may adversely affect the normal function of the product in the system application. The test procedure varies greatly according to PCBA and system, and should be provided by the customer during OEM production.
5. Cleaning and packaging: PCBA shall be separated in a SMAll box in a standard large carton. Internal protective bubble bag. All circuit boards are stored in RoHS compliant storage packaging to prevent moisture. If any unopened packaging is expired or opened, these parts will need to be properly baked to remove excess moisture.
How to manage personnel and equipment in PCBA workshop management
PCBA workshop management is mainly to manage the production of PCBA processing plant, so that each employee can improve product quality, increase production efficiency, reduce production costs and ensure production safety while earnestly implementing various rules and regulations of the company. PCBA workshop management includes the management of employees, workshop equipment and production site environment. Then, how should PCBA workshop management manage people and equipment.
First of all, the management of workshop personnel must strictly abide by the labor discipline formulated by the supervisor, and comply with their own post requirements. Without special circumstances, man and machine cannot be separated. At the same time, basic 5S must be achieved for the requirements of the working environment. It is suggested that the workshop can achieve positioning management, and each item in the workshop has its own location, so that each item can be returned to its original location after use. The most important thing is to do a good job in safe operation management. Employees without licenses are not allowed to operate the machine. Employees must wear electrostatic bracelets when working.
At the same time, equipment is particularly important for the control of the entire PCBA process, which can effectively reduce human intervention and improve quality control. Therefore, manufacturers need to invest money to purchase some auxiliary equipment to improve efficiency. In addition, regular equipment maintenance is essential, and the establishment of maintenance registration is one of the effective management methods.
PCB manufacturers, PCB designers and PCBA manufacturers explain how to implement PCBA quality standards? And PCBA workshop management.
然后
聯(lián)系
電話熱線
13410863085Q Q
微信
- 郵箱