
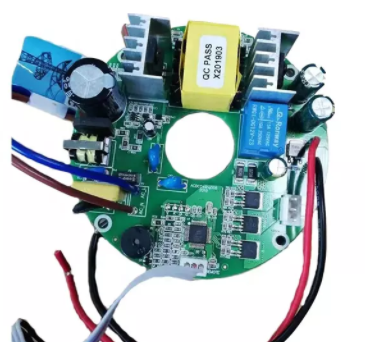
Car battery charging is a devICe that supplies direct current (DC) to the battery to restore spent electrolyte, in addition to improving safety and adding new features, it is also necessary to reduce the risk of battery failure and ensure a safe and reliable power supply for all the vehicle's It is necessary for components to function properly, and automotive battery charging systems must overcome harsh environments including temperature, humidity, rain, acid smoke, vibration, electromagnetic interference (EMI), and current surges.
When designing a car battery charging PCB, it is necessary to pay attention to the inductor orientation, lead coupling, grounding vias, grounding and filling, etc. The inductor orientation requires the inductor space should be as large as possible and the inductor arrangement should be set at right angles; comprehensive grounding should be Arranged under the lead, the through hole of the sensitive area should be provided with an inductance module, and a continuous grounding of the impedance should be provided in terms of grounding and filling, and the terminal of the filling line should be grounded using an array of through holes.
Kingford battery charger PCB has high transmission power, wide range, low loss, stable performance, etc. The car battery charging PCB we designed has passed the quality test of load output, no-load output, full-load efficiency, short circuit, circuit protection and so on.
Car battery charging PCB assembly performance parameters:
Number of layers: 1, 2, 4 to 6 layers, up to 18 layers
Solder mask color: white black yellow green red
Copy Punching: Routing, V-CUT, Chamfering
board cutting: Shear, V-score, Tab-routed
Minimum Drilling Diameter: 0.01", 0.25mm, or 10mils
Copper Weight Tolerance: +/-0.25 oz
Plate Thickness Tolerance: +/-10%
Copper Thickness: 3 oz
Substrate: FR4, CEM3, FR1, Taconic, Rogers
然后
聯(lián)系
電話熱線
13410863085Q Q
微信
- 郵箱