
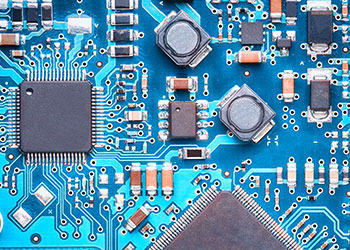
Why to preheat before PCBA processing
The importance of temperature distribution in PCB processing and welding environment in mass production has been widely understood The slow heating and preheating phases help to start the flux, prevent thermal shock and improve the quality of solder joints during SMT placement However, when it comes to rework, prototype design, or PCBA first artICle proofing project, it is easy to forget the importance of the warm-up phase. Even if the equipment is not damaged, it may also lead to equipment damage So, for this important step, why is it often forgotten in the actual operation of SMT processing plants? What are the consequences of omitting this stage?
Reflow soldering preheating zone
What was the previous preheating for PCBA welding?
When technicians and practitioners hear the words "temperature curve" or "temperature curve", they will think of smt reflow. The four main temperature control zones can be easily seen along the huge length of the weld zone, which will eventually produce a perfect weld joint, hopefully. Carefully control and improve each stage through the experience and repeated tests of scientific and technical personnel. Each stage plays a role in improving the quality of solder joints and reducing defects. But other industrial welding machines may not have such fine temperature control. But what they have in common is the warm-up phase.
Flux Combustion in Selective Wave Soldering
pcba board
The function of preheating stage is to steadily increase the temperature of the whole assembly from room temperature to a holding temperature lower than the melting point of solder paste (about 150 ℃). Adjust the temperature change to maintain a constant slope of several degrees per second. After the preheating phase is the soaking phase, which will maintain the temperature for a period of time to ensure that the circuit board is heated evenly. Then the reflow phase begins to form solder joints. During preheating and soaking, the volatile solvent in the solder paste is burned off and the flux is started.
Medical electronic PCBA electronic manufacturing capacity
The medical electronic equipment manufacturing industry is facing fierce competition at all levels of the MARKet. The industry has made a high degree of innovation in product layout/manufacturing, and has upgraded medical care to a new level through technological progress.
Experience in the following projects:
1. PCB circuit board manufacturing of medical diagnostic equipment;
2. Production of interconnection between Flexible circuit board (Flex) and rigid flexible board (Rigid Flex);
3. Manufacturing of medical electronic equipment imaging system and imaging electronic equipment circuit board;
4 PCBA components for the circuit board of the medical motion control system;
5. PCB processing of high-tech temperature measurement equipment for security inspection and epidEMIc prevention;
6. Used for patch processing of control circuit board of medical optical instruments;
7. Processing of medical power control panel for SMAll dental equipment;
8. Hardware manufacturing of 3D high-resolution scanner;
9. PCB packaging materials for digital X-ray;
Extensive PCBA component/packaging manufacturing capacity, and the use of the latest technology PCBA project provides personalized service You can go directly to the site to have in-depth communication with the engineering team and ensure that the communication between the manufacturer and the engineer is improved
然后
聯(lián)系
電話熱線
13410863085Q Q
微信
- 郵箱