鑫景福致力于滿足“快速服務(wù),零缺陷,支持無理由退換”PCBA訂購單需求。

PCBA加工
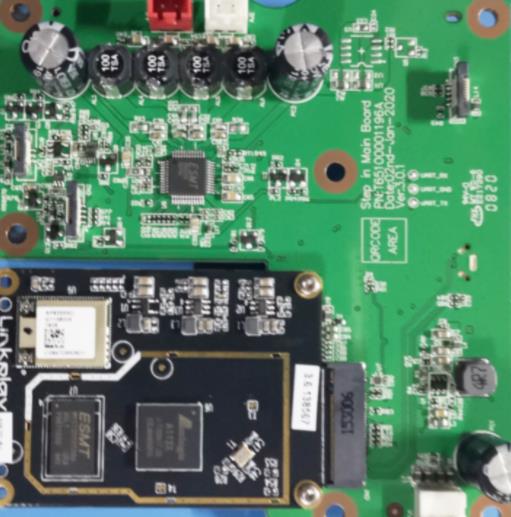
SMT Inductance Principle and PCBA Solder Paste Printing
Ten Principles for chip Inductors Smt Chip Processing
1. The space between chip inductors should be SMAller than the space between inductors to prevent excessive solder from causing excessive tensile stress during cooling, thus changing the inductance value.
2. The precision of chip inductors available on the MARKet is mostly ± 10%. If the required accuracy is higher than ± 5%, you need to order in advance.
3. Some chip inductors can adopt reflow welding and wave soldering, but some chip inductors cannot adopt wave soldering. During repair, inductance cannot be replaced by inductance alone. In order to ensure the working effICiency, it is also necessary to know the working frequency band of the chip inductor.
5. The shape and size of the chip inductor are basically SIMilar, and there is no obvious mark on the shape. During manual welding or manual repair welding, do not take the wrong position or parts.
6. At present, there are three kinds of chip inductors: the first is microwave high-frequency inductors. It is applicable to frequency bands above 1GHz. The second type is high-frequency chip inductor. It is applicable to resonant circuit and frequency selection circuit. The third type is universal inductor. It is generally applicable to circuits with tens of megahertz.
The maximum allowable current is also the quota of chip inductance. When the circuit needs to bear large current, the capacitance indicator must be considered.
When a power inductor is used in a DC converter, its inductance directly affects the working state of the circuit. In practice, inductance can usually be changed by adding or reducing coils to obtain the best results.
10. For communication equipment operating in the 150~900MHz frequency band, winding inductors are usually used. In circuits with frequencies higher than 1GHz, microwave high-frequency inductors must be used.
Six common defects and their causes PCBA solder paste printing
Solder paste printing is a very critical and complex process in PCBA processing. The quality of solder paste printing is not only related to the quality of solder paste, but also directly related to the equipment and product parameters of solder paste printing. SMT chip processing manufacturers can improve the printing quality of solder paste by controlling each key point. Next, I will introduce six common defects and reasons in solder paste printing in detail.
1. Incomplete printing: refers to the missing printing of some pads on the printed circuit board.
Root cause:
(1) Plug the opening of the steel mesh or attach a part of the solder paste to the bottom of the steel mesh;
(2) Solder paste viscosity is not up to standard;
(3) The size of metal particles in solder paste is unqualified;
(4) The scraper is severely worn.
Suggestions for improvement:
(1) After using the wire mesh, pay attention to the maintenance of the wire mesh and clean it immediately;
(2) Select the solder paste with proper viscosity;
(3) When selecting solder paste, full consideration should be given to whether the size and particle size of metal particles are smaller than the size of steel mesh opening;
(4) Regularly check and replace the scraper.
2. Sharpening: refers to the solder paste with sharp protrusions on the bonding pad after the solder paste is printed.
Root cause: There is a problem with the viscosity of the solder paste or the gap between the scrapers is too large.
Suggestions for improvement: select the solder paste with proper viscosity and change the scraper clearance.
3. Collapse: refers to the solder paste on the pad collapses to both sides of the pad.
Root cause:
(1) The working pressure parameter of scraper is set too large;
(2) PCB board is not placed correctly, causing offset;
(3) The viscosity or metal content of solder paste is low.
Suggestions for improvement:
(1) Change the working pressure of the scraper;
(2) Reposition PCB board;
(3) Re select the solder paste, taking full account of viscosity, metal content and other factors. Analysis of Six Solder Paste Printing Defects in SMT chip processing
4. Solder paste is too thin: the thickness of solder paste on the pad does not meet the standard.
Root cause:
(1) The thickness of the steel wire mesh manufactured does not meet the standard;
(2) The product parameter of scraper working pressure is too large;
(3) The fluidity of solder paste is poor.
Suggestions for improvement:
(1) The thickness of solder paste shall be consistent with that of the template;
(2) Reduce the working pressure of the scraper;
(3) Select a better quality solder paste.
5. Different thickness: the thickness of solder paste is different after printing.
Root cause: PCB board and steel mesh are not parallel, and solder paste is mixed unevenly.
Suggestions for improvement: Make PCB and steel mesh as good as possible, and stir evenly before using solder paste.
6. Burr: there is burr on the edge or surface of solder paste
Root cause:
(1) Solder paste viscosity is too low;
(2) The wire mesh has rough openings.
Suggestions for improvement:
(1) When determining the solder paste, the viscosity of the solder paste should be fully considered;
(2) Select laser method to open holes or improve etching accuracy as much as possible.
To improve the quality of solder paste printing, we must start from every key point From the choice of solder paste, quality of wire mesh, product parameters of mechanical equipment, etc Each key point will affect the final printing quality
Ten Principles for chip Inductors Smt Chip Processing
1. The space between chip inductors should be SMAller than the space between inductors to prevent excessive solder from causing excessive tensile stress during cooling, thus changing the inductance value.
2. The precision of chip inductors available on the MARKet is mostly ± 10%. If the required accuracy is higher than ± 5%, you need to order in advance.
3. Some chip inductors can adopt reflow welding and wave soldering, but some chip inductors cannot adopt wave soldering. During repair, inductance cannot be replaced by inductance alone. In order to ensure the working effICiency, it is also necessary to know the working frequency band of the chip inductor.
5. The shape and size of the chip inductor are basically SIMilar, and there is no obvious mark on the shape. During manual welding or manual repair welding, do not take the wrong position or parts.
6. At present, there are three kinds of chip inductors: the first is microwave high-frequency inductors. It is applicable to frequency bands above 1GHz. The second type is high-frequency chip inductor. It is applicable to resonant circuit and frequency selection circuit. The third type is universal inductor. It is generally applicable to circuits with tens of megahertz.
The maximum allowable current is also the quota of chip inductance. When the circuit needs to bear large current, the capacitance indicator must be considered.
When a power inductor is used in a DC converter, its inductance directly affects the working state of the circuit. In practice, inductance can usually be changed by adding or reducing coils to obtain the best results.
10. For communication equipment operating in the 150~900MHz frequency band, winding inductors are usually used. In circuits with frequencies higher than 1GHz, microwave high-frequency inductors must be used.
Six common defects and their causes PCBA solder paste printing
Solder paste printing is a very critical and complex process in PCBA processing. The quality of solder paste printing is not only related to the quality of solder paste, but also directly related to the equipment and product parameters of solder paste printing. SMT chip processing manufacturers can improve the printing quality of solder paste by controlling each key point. Next, I will introduce six common defects and reasons in solder paste printing in detail.
1. Incomplete printing: refers to the missing printing of some pads on the printed circuit board.
Root cause:
(1) Plug the opening of the steel mesh or attach a part of the solder paste to the bottom of the steel mesh;
(2) Solder paste viscosity is not up to standard;
(3) The size of metal particles in solder paste is unqualified;
(4) The scraper is severely worn.
Suggestions for improvement:
(1) After using the wire mesh, pay attention to the maintenance of the wire mesh and clean it immediately;
(2) Select the solder paste with proper viscosity;
(3) When selecting solder paste, full consideration should be given to whether the size and particle size of metal particles are smaller than the size of steel mesh opening;
(4) Regularly check and replace the scraper.
2. Sharpening: refers to the solder paste with sharp protrusions on the bonding pad after the solder paste is printed.
Root cause: There is a problem with the viscosity of the solder paste or the gap between the scrapers is too large.
Suggestions for improvement: select the solder paste with proper viscosity and change the scraper clearance.
3. Collapse: refers to the solder paste on the pad collapses to both sides of the pad.
Root cause:
(1) The working pressure parameter of scraper is set too large;
(2) PCB board is not placed correctly, causing offset;
(3) The viscosity or metal content of solder paste is low.
Suggestions for improvement:
(1) Change the working pressure of the scraper;
(2) Reposition PCB board;
(3) Re select the solder paste, taking full account of viscosity, metal content and other factors. Analysis of Six Solder Paste Printing Defects in SMT chip processing
4. Solder paste is too thin: the thickness of solder paste on the pad does not meet the standard.
Root cause:
(1) The thickness of the steel wire mesh manufactured does not meet the standard;
(2) The product parameter of scraper working pressure is too large;
(3) The fluidity of solder paste is poor.
Suggestions for improvement:
(1) The thickness of solder paste shall be consistent with that of the template;
(2) Reduce the working pressure of the scraper;
(3) Select a better quality solder paste.
5. Different thickness: the thickness of solder paste is different after printing.
Root cause: PCB board and steel mesh are not parallel, and solder paste is mixed unevenly.
Suggestions for improvement: Make PCB and steel mesh as good as possible, and stir evenly before using solder paste.
6. Burr: there is burr on the edge or surface of solder paste
Root cause:
(1) Solder paste viscosity is too low;
(2) The wire mesh has rough openings.
Suggestions for improvement:
(1) When determining the solder paste, the viscosity of the solder paste should be fully considered;
(2) Select laser method to open holes or improve etching accuracy as much as possible.
To improve the quality of solder paste printing, we must start from every key point From the choice of solder paste, quality of wire mesh, product parameters of mechanical equipment, etc Each key point will affect the final printing quality
點(diǎn)擊
然后
聯(lián)系
然后
聯(lián)系
電話熱線
13410863085Q Q
微信
- 郵箱