
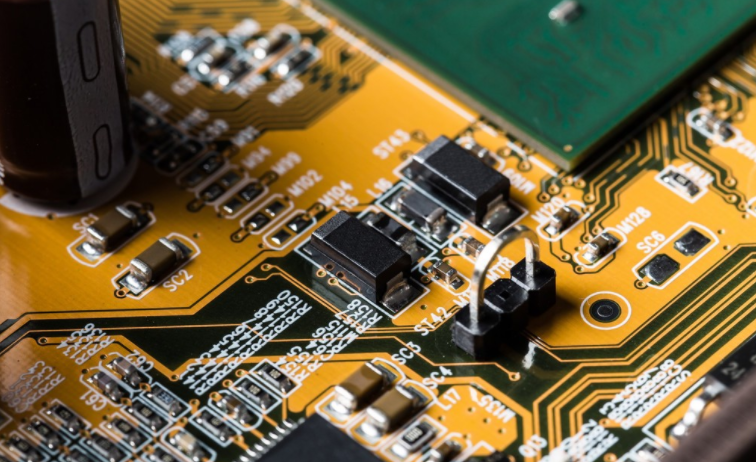
Six Methods to Reduce the Defect Rate of Automobile PCB
The automotive PCB electronics MARKet is the third largest category of PCB applICations, second only to computers and communications With the gradual evolution of automobiles from traditional machine goods to intelligent high-tech goods, informatization and electromechanical integration, electronic technology has been widely used in automobiles Electronic products have been adopted without exception, whether they are starting systems, chassis systems, security systems, information systems and internal environment systems Obviously, the automobile market has become another highlight of the electronic consumer market The development of Automotive electronics naturally drives the development of Automotive PCB
In today's key objects of printed circuit board, automobile PCB occupies an important position. However, due to the special task environment, safety and high current requirements of automobiles, the reliability and environmental compliance requirements for PCB are very high, involving a wide range of PCB technology types, which is a challenge for PCB enterprises; For manufacturers who want to expand the automotive PCB market, they need to do more understanding and analysis of the new market.
Automobile PCB enhances high reliability and low DPPM Can our enterprise accumulate technology and experience in high reliability manufacturing? Can it be different from the direction of future commodity development? In process control, can you do well according to the requirements of TS16949? Have you achieved low DPPM? These should be carefully evaluated Seeing this tempting cake and consciously entering it will damage PCB enterprises themselves
PCB is closely related to consumer electronics, 5G and other concepts. However, with the development of new energy vehicles getting better and better, the application of PCB in automotive electronics has begun to attract market attention.
On the one hand, in the automotive industry, PCB is mainly used for auxiliary drive, vehicle communication, power control and other links. For traditional fuel vehicles, the average consumption of PCB is 1 square meter, while the average consumption of high-end vehicles is 2-3 square meters. The PCB value of each vehicle is about 500-600 yuan.
However, due to the addition of BMS, MCU and other equipment in new energy vehicles, the area of PCB has increased to 3-5 square meters. The PCB value of a single vehicle exceeds 2000 yuan, four times that of traditional fuel vehicles. According to the data of PriSMArk, the PCB output value of the global automotive industry last year was 6.19 billion US dollars. It is estimated that the output value in 2024 will reach 8.75 billion US dollars, accounting for 10.6% of the global PCB output value, and the compound growth rate in 2020-2024 will reach 9%.
On the other hand, it is a subdivision field FPC (Flexible circuit board/flexible board). In traditional fuel vehicles, the consumption of single vehicle FPC exceeds 100 yuan, which is mainly used for electronic control automatic systems such as on-board display group and vehicle electronic equipment, engine system, seats, doors and vehicle control, and automatic safety systems such as vehicle image system and sensors.
Printed circuit board
The following provides some special practices of representative local professional consumer automotive PCB enterprises in the testing process for reference:
1. Secondary test method
Local PCB multilayer board consumer enterprises adopt the "secondary test method" to improve the rate of defective boards after the first high-voltage breakdown.
2. chip anti stupidity test
More and more printed circuit board manufacturers have instalLED "good board marking system" and "bad board error proofing box" on the optical board testing machine to effectively prevent man-made leakage. The good board identification system is used to block the testing machine to identify the qualified boards, which can effectively prevent the test boards or defective boards from flowing into the hands of customers. Defective board error proofing box refers to the signal that the chip input box is opened when the qualified board is tested during the test; On the contrary, when testing a damaged circuit board, the box will be closed so that the operator can correctly place the tested circuit board.
3. Establish ppm quality system
At present, ppm (one millionth) quality system is widely used in PCB manufacturers. Among many of our customers, Hitachi ChEMIcal in Singapore is most worthy of self creation for its use and effectiveness. The factory has more than 20 professionals responsible for statistical analysis of online PCB quality exceptions and PCB quality exception returns. SPC consumption process statistical analysis method is used to classify and analyze each defective circuit board and each returned defective circuit board, and combined with micro slicing and other auxiliary tools to analyze which circuit board is damaged or defective in the manufacturing process. According to the statistical data results, the results presented in the process are processed purposefully.
4. Analogy test method
Some customers use two different brands of PCB boards to stop comparative testing in different batches, and track the PPM status of the corresponding batches, so as to understand the functions of the two testing machines, so as to select a better testing machine to stop testing PCB boards of automobiles
5. Progress test parameters
Select higher test parameters to detect such PCB boards. Because, if higher voltage and threshold value are selected, and high voltage leakage reading times are added, the detection rate of PCB defective boards can be improved. For example, a large Taiwan funded PCB enterprise in Suzhou used 300V, 30m and 20 Ω to stop testing automotive PCBs.
6. Current calibration tester parameters
After the tester is operated temporarily, the internal resistance and other relevant test parameters will deviate Therefore, the machine parameters need to be adjusted regularly to ensure the accuracy of the test parameters A considerable number of test equipment in large printed circuit board enterprises stop the maintenance of parts and the adjustment of external functional parameters within half a year or one year Pursuing "zero defect" automobile PCB Multilayer board is the direction of continuous efforts of PCB people. However, limited by process equipment, raw materials and other aspects, IPCB is still exploring ways to reduce ppm
然后
聯(lián)系
電話熱線
13410863085Q Q
微信
- 郵箱