
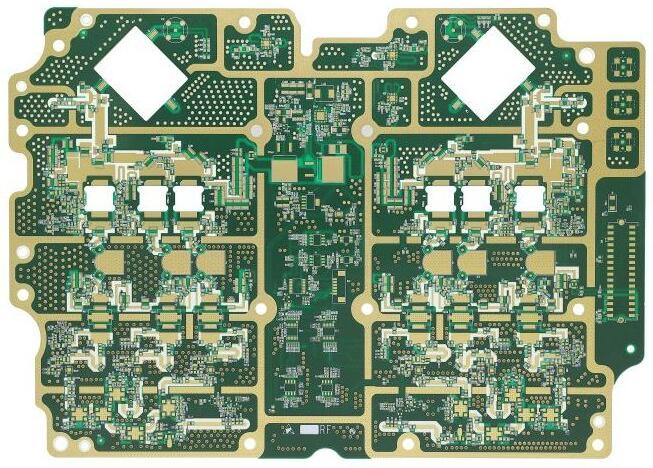
How to eliminate the short circuit fault in PCBA processing
How to eliminate PCBA processing short circuit fault?
PCB company is a PCBA processing factory specialized in providing overall PCBA electronic manufacturing services, including one-stop servICes from upstream electronic component procurement to PCB production and processing, SMT chip processing, DIP plug-in processing, PCBA testing, and finished product assembly. Here is how to remove the short circuit fault in PCBA processing.
Troubleshooting of short circuit in PCBA processing
1、 Open the PCB design drawing on the computer, light up the short circuited network, and see where is the nearest one, which is easiest to connect to one. Pay special attention to the short circuit inside the IC.
2、 If manual welding is used, good habits should be formed:
1. Before welding, visually check the PCB board, and use a multimeter to check whether the key circuits (especially the power supply and ground) are short circuited; 2. Every time a chip is welded, use a multimeter to test whether the power supply and ground are short circuited; 3. Do not throw the soldering iron randomly during welding. If the soldering tin is thrown onto the solder leg of the chip (especially the surface mount components), it will not be easy to find.
3、 A short circuit was found. Take a board to cut lines (especially for single/double layer boards). After cutting lines, power on each function block separately and gradually eliminate it. 4、 Use short circuit positioning analyzer.
5、 If there is a BGA chip, because all the solder joints are covered by the chip and cannot be seen, and it is also a Multilayer board (more than 4 layers), it is better to separate the power supply of each chip during the design, and connect it with a magnetic bead or a 0 ohm resistance. In this way, when the power supply is short circuited to the ground, disconnect the magnetic bead detection, and it is easy to locate a chip. Because BGA is difficult to weld, if it is not automatically welded by the machine, it will short circuit the adjacent power supply and the two welding balls.
6、 Be careful when welding SMAll surface mount capacitors, especially power filter capacitors (103 or 104), which are large in number, can easily cause short circuit between power supply and ground. Of course, sometimes the capacitor is short circuited due to bad luck, so the best way is to check the capacitor before welding.
How to Evaluate Manufacturability in PCB Design
1. DFM review of optical board: whether the production of optical board meets the technical requirements of PCB manufacturing, including line width, spacing, wiring, layout, through-hole, MARKing, wave soldering component direction, etc.
2. Check the consistency between the actual components and the bonding pad: whether the actual SMT mounting components purchased are consistent with the designed bonding pad (if not, please use a red label to indicate), and whether they meet the spacing requirements of the SMT mounting machine.
3. Generate 3D graphics: generate 3D graphics, check whether space elements interfere with each other, whether element layout is reasonable, whether it is conducive to heat dissipation, whether it is conducive to SMT reflow soldering heat absorption, etc.
4. PCBA production line optimization: optimize the loading sequence and the location of the material station. Input the existing pasting machine (such as Siemens high-speed machine, universal multi-function machine) into the software, and distribute the components to be pasted onto the existing board. How many types of pasting Siemens has, how many types of pasting Siemens has, how many types of pasting Siemens has, how many types of pasting methods are there in the world, how many locations and where to pick up materials, etc. This can optimize the SMT chip processing program and save time. For multi line production, the distribution of instalLED components can also be optimized.
5. Operation instructions: automatically generate the operation instructions of the workers on the production line.
6. Revision of Inspection Rules: inspection rules can be modified. For example, if the component spacing is 0.1mm, the manufacturer and circuit board complexity can be set to 0.2mm according to the specific model, the line width is 6mi, and it can be changed to 5mil in high-density design.
7. Support Panasonic, Fuji and Universal patch software: it can automatically generate paste software to save programming time.
8. Automatically generate steel plate optimization graphics.
9. Automatically generate AOI and X-ray programs.
10. Check to support multiple software formats (Japan, KATENCE, China PROTEL).
11. Check the BOM and correct relevant errors, such as spelling errors of the manufacturer. BOM is converted to software format. PCB design capacity Maximum signal design rate: 10Gbps CML differential signal; Maximum number of PCB design layers: 40; Minimum line width: 2.4mil; Minimum line spacing: 2.4mil; Minimum BGA PIN spacing: 0.4mm; Minimum mechanical hole diameter: 6mil; Minimum laser drilling diameter: 4mil; Maximum number of PINs:; 63000+Maximum number of elements: 3600; Maximum number of BGAs: 48+.
PCB design service process
1. The customer provides schematic diagram consulting PCB design; 2. Evaluate the quotation according to the schematic diagram and customer design requirements; 3. The customer confirms the quotation, signs the contract and prepays the project deposit; 4. Receive the advance payment and arrange the engineer to design; 5. After the design is completed, provide the document screenshot to the customer for confirmation; 6. The customer confirmed that it was OK, settled the balance and provided PCB design data.
然后
聯(lián)系
電話熱線
13410863085Q Q
微信
- 郵箱