
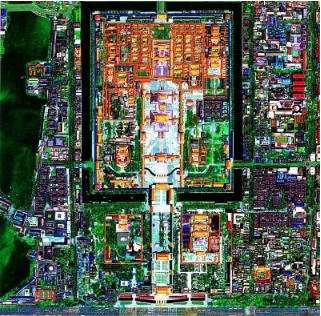
1、 Shape and size design standard of middle pad
PCB standard package library should be calLED.
The minimum unilateral diameter of all pads shall not be less than 0.2gai5mm, and the maximum diameter of the entire pad shall not be greater than 3 times of the element aperture.
The distance between the edges of two pads shall be greater than 0.4 mm as far as possible.
Oval and oblong connecting discs are recommended in dense cases. The diameter or minimum width of a single side PCB pad is 1.6mm; The hole diameter of the weak current circuit pad of the double-sided board is only required to add 0.5mm, and excessive pad size may cause unnecessary continuous welding.
Pads with hole diameter more than 1.2mm or pad diameter more than 3.0mm shall be designed as diamond or quincunx pads
For plug-in PCB components, in order to avoid copper foil breakage during welding, and the single side connecting plate shall be completely covered with copper foil; The minimum requirement of double panel is to fill tears; As shown in the figure:
All machine plug-in parts shall be designed as drip pads along the bending foot direction to ensure full welding points at the bending foot.
The daisy shaped pad shall be used for the pad on the large area copper sheet to avoid false soldering. If there is a large area of ground wire and power line area on the PCB (the area exceeds 500 mm2), a window should be opened locally or the grid should be designed to fill (FILL).
2、 PCB manufacturing requirements for bonding pads
If the two ends of the SMD components are not connected with the plug-in components, test points shall be added, and the diameter of the test points shall be equal to or greater than 1.8mm, so as to facilitate the online tester test.
If the IC pin pad with dense pin spacing is not connected to the hand plug-in pad, it needs to add a test pad. If it is a patch IC, the test point cannot be placed in the patch IC silk screen. The diameter of the test point is equal to or greater than 1.8 mm, so as to facilitate the online tester test.
If the bonding pad spacing is less than 0.4mm, white oil must be paved to reduce the continuous welding when passing the wave peak.
Both ends and ends of the SMD element shall be designed with tin lead. The width of tin lead is recommended to be 0.5mm, and the length is generally 2 or 3mm.
If there are hand soldering elements on the single panel, the tin bath shall be removed in the opposite direction to the tin passing direction. The width of the hole depends on the size of 0.3MM to 1.0MM; (50-70% of the hole diameter) as shown in the figure below:
The spacing and size of conductive rubber keys should be consistent with the size of the actual conductive rubber keys. The PCB connected with this should be designed as a gold finger, and the corresponding gold plating thickness should be specified.
The size and spacing of PCB pads shall be the same as that of patch elements (1:1).
For solder joints with a distance of less than 0.4mm between pads (the number of pads is more than 4) on the same line, if the long side of the component is parallel to the wave crest direction as much as possible on the basis of adding white oil, then add an empty pad at the end of the pad or increase the PCB pad at the end of the pad, so as to eat trailing solder to reduce continuous soldering.
然后
聯(lián)系
電話熱線
13410863085Q Q
微信
- 郵箱