
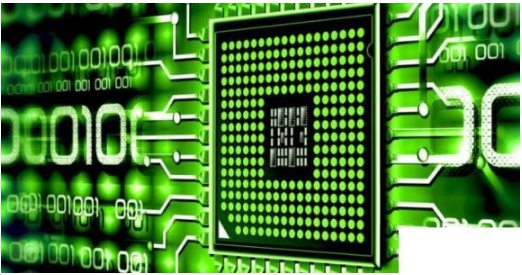
Most of the electrICal energy consumed by PCB devices during operation, such as RF power amplifiers, FPGA chips, and power products, except for useful power, is converted into heat EMIssion. The heat generated by electronic equipment makes the internal temperature rise rapidly. If the heat is not dissipated in time, the equipment will continue to heat up, and the components will fail due to overheating, and the reliability of electronic equipment will decline. The installation density of electronic equipment increases, the effective heat dissipation area decreases, and the temperature rise of equipment seriously affects the reliability. Therefore, the research on thermal design is very important.
The brother who engages in radio frequency has firewood, so it's OK to dissipate heat?
The heat dissipation of PCB is a very important link. Now let's discuss the heat dissipation techniques of PCB.
For electronic equipment, a certain amount of heat will be generated during operation, so that the internal temperature of the equipment will rise rapidly. If the heat is not dissipated in time, the equipment will continue to rise in temperature, the devices will fail due to overheating, and the reliability of electronic equipment will decline. Therefore, it is very important to conduct good heat dissipation treatment.
The direct cause of PCB temperature rise is the existence of circuit power consumption devices, Electronic devices have power consumption in varying degrees, and the heat intensity varies with the power consumption.
Two phenomena of temperature rise in PCB:
(1) Local temperature rise or large area temperature rise;
(2) Short time temperature rise or long time temperature rise. In analyzing PCB thermal power consumption, the following aspects are generally analyzed.
2.1 Electrical power consumption
(1) Analyze the power consumption per unit area;
(2) Analyze the distribution of power consumption on PCB.
2.2 Structure of printed board
(1) Dimensions of printed boards;
(2) Materials of printed boards.
2.3 Installation mode of printed board
(1) Installation mode (such as vertical installation and horizontal installation);
(2) Sealing condition and distance from the casing.
2.4 Thermal radiation
(1) Radiation coefficient of printed board surface;
(2) Temperature difference between printed board and adjacent surface and their absolute temperature
2.5 Heat conduction
(1) Install the radiator;
(2) Conduction of other mounting structures.
2.6 Thermal convection
(1) Natural convection;
(2) Forced cooling convection.
The analysis of the above factors of PCB is an effective way to solve the temperature rise of PCB. These factors are often interrelated and dependent in a product and system. Most factors should be analyzed according to the actual situation. Only for a specific actual situation can the temperature rise, power consumption and other parameters be calculated or estimated correctly.
1 Heat dissipation through PCB
At present, the widely used PCB boards are copper clad/epoxy glass cloth substrate or phenolic resin glass cloth substrate, and there are a few paper based copper clad boards. Although these substrates have excellent electrical and processing properties, they have poor heat dissipation. As a heat dissipation way for high heating elements, they can hardly be expected to transmit heat from the resin of PCB itself, but to dissipate heat from the surface of the element to the surrounding air. However, as PCB products have entered the era of component miniaturization, high-density installation and high heating assembly, it is not enough to rely only on the surface of components with very SMAll surface area for heat dissipation.
At the same time, due to the large use of surface mounted components such as QFP and BGA, a large amount of heat generated by the components is transferred to the pcb board. Therefore, the best way to solve heat dissipation is to improve the heat dissipation capacity of the PCB itself in direct contact with the heating elements, which is transmitted or distributed through the PCB board.
2 High heating element plus radiator and heat conduction plate
When there are a few components in the PCB with large heating capacity (less than 3), a radiator or heat transfer tube can be added to the heating components. When the temperature cannot be reduced, a radiator with a fan can be used to enhance the heat dissipation effect.
When there are many heating devices (more than 3), large heat dissipation cover (plate) can be used. It is a special radiator customized according to the position and height of the heating devices on the PCB board, or different component high and low positions can be picked out on a large flat panel radiator.
Buckle the heat shield onto the element surface as a whole, and contact each element to dissipate heat. However, the heat dissipation effect is not good due to the low consistency of components during assembly and welding. Usually, a soft thermal phase change heat conduction pad is added on the surface of the components to improve the heat dissipation effect.
3 For equipment cooLED by free convection air, it is better to arrange the integrated circuit (or other devices) in longitudinal or transverse direction.
4 Use reasonable wiring design to realize heat dissipation
Because the resin in the sheet has poor thermal conductivity, and the copper foil lines and holes are good conductors of heat, improving the copper foil residual rate and increasing the thermal conductivity holes are the main means of heat dissipation.
To evaluate the heat dissipation capability of a PCB, it is necessary to calculate the equivalent thermal conductivity (9 eq) of the insulating substrate for PCB, a composite material composed of various materials with different thermal conductivity.
5 The components on the same printed board shall be arranged in zones as far as possible according to their calorific value and heat dissipation degree. The components with low calorific value or poor heat resistance (such as small signal transistors, small-scale integrated circuits, electrolytic capacitors, etc.) shall be placed at the top (entrance) of the cooling air flow, and the components with high calorific value or good heat resistance (such as power transistors, large-scale integrated circuits, etc.) shall be placed at the bottom of the cooling air flow.
6 In the horizontal direction, high-power devices shall be arranged as close to the edge of the printed board as possible to shorten the heat transfer path; In the vertical direction, high-power devices shall be arranged as close as possible to the top of the printed circuit board, so as to reduce the impact of these devices on the temperature of other devices during operation.
7 The heat dissipation of the printed circuit board in the equipment mainly depends on the air flow, so the air flow path should be studied during the design, and the device or printed circuit board should be reasonably configured. When air flows, it always tends to flow in a place with small resistance. Therefore, when configuring components on the PCB, it is necessary to avoid leaving a large space in a certain area. The configuration of multiple printed circuit boards in the whole machine should also pay attention to the same problem.
8 The devices that are sensitive to temperature should be placed in the area with the lowest temperature (such as the bottom of the equipment), and should not be placed directly above the heating devices. Multiple devices should be staggered on the horizontal plane.
9 Place the devices with the highest power consumption and heat generation near the best heat dissipation position. Do not place the components with high heat generation on the corners and surrounding edges of the printed board, unless there is a heat sink near it. In the design of power resistance, select a larger device as far as possible, and make it have enough heat dissipation space when adjusting the layout of the printed circuit board.
10 RF power amplifier or LED PCB adopts metal base plate.
11 Avoid the concentration of hot spots on the PCB, distribute the power evenly on the PCB as much as possible, and maintain the uniformity and consistency of PCB surface temperature performance. It is often difficult to achieve strict uniform distribution in the design process, but the area with too high power density must be avoided to avoid the occurrence of hot spots that affect the normal operation of the entire circuit. If conditions permit, it is necessary to conduct thermal efficiency analysis of printed circuit. For example, the thermal efficiency index analysis software module added to some professional PCB design software can help designers optimize circuit design.
4.1 Material selection
(1) The temperature rise caused by the current passing through the conductor of the printed board plus the specified ambient temperature shall not exceed 125 ℃ (the typical value in common use. It may vary depending on the selected board). As the components installed on the printed board also emit some heat, which affects the working temperature, these factors should be taken into account when selecting materials and designing the printed board, and the hot spot temperature should not exceed 125 ℃. Choose a thicker copper clad foil as much as possible.
(2) Under special circumstances, aluminum based, ceramic based and other plates with low thermal resistance can be selected.
(3) Multilayer structure is helpful to PCB thermal design.
4.2 Ensure smooth heat dissipation channel
(1) Make full use of component layout, copper sheet, windowing, heat dissipation hole and other technologies to establish a reasonable and effective low thermal resistance channel to ensure the smooth export of heat from PCB.
(2) The setting of heat dissipation through-hole is designed with some heat dissipation through-hole and blind hole, which can effectively improve the heat dissipation area, reduce the thermal resistance, and improve the power density of the circuit board. For example, a through hole is set on the bonding pad of LCCC device. In the circuit production process, solder is used to fill it, so as to improve the thermal conductivity. The heat generated during the circuit operation can be quickly transferred to the metal heat dissipation layer or the copper foil set on the back through the through hole or blind hole. In some specific cases, circuit boards with heat dissipation layers are specially designed and used. The heat dissipation materials are generally copper/molybdenum and other materials, such as printed boards used on some module power supplies.
(3) Use of thermal conductive materials In order to reduce the thermal resistance in the heat conduction process, thermal conductive materials are used on the contact surface between the high power consumption device and the substrate to improve the heat conduction efficiency.
(4) The process method is easy to cause local high temperature in some areas with devices on both sides. In order to improve the heat dissipation condition, a small amount of fine copper can be added into the solder paste, and the solder joint under the device will have a certain height after reflow soldering. The gap between the device and the printed circuit board is increased, and the convection heat dissipation is increased.
4.3 Layout requirements of components
(1) Conduct software thermal analysis on PCB, and design and control the highest internal temperature rise;
(2) The components with high heating and large radiation can be specially designed and installed on a printed board;
(3) The heat capacity of the board surface is evenly distributed. Pay attention not to place the high power consumption devices in a centralized manner. If it is unavoidable, place the low components in the upstream of the air flow, and ensure that sufficient cooling air flows through the heat consumption concentrated area;
(4) Keep the heat transfer path as short as possible;
(5) Make the heat transfer cross-section as large as possible;
(6) The Layout of components shall take into account the influence on the thermal radiation of surrounding parts. Heat sensitive parts and components (including semiconductor devices) shall be kept away from heat sources or isolated;
(7) (Liquid medium) capacitor should be kept away from heat source;
(8) Pay attention to keeping the direction of forced ventilation consistent with that of natural ventilation;
(9) The air duct of additional sub boards and components shall be consistent with the ventilation direction;
(10) Keep enough distance between intake and exhaust as far as possible;
(11) The heating device shall be placed above the product as much as possible and on the air flow channel when conditions permit;
(12) Components with high heat or current shall not be placed at the corners and surrounding edges of the printed board. If possible, they shall be installed on the radiator and away from other components, and the cooling channel shall be smooth;
(13) (Peripheral components of small signal amplifier) Try to use components with small temperature drift;
(14) The metal case or chassis shall be used for heat dissipation as much as possible.
4.4 Requirements for wiring
(1) Board selection (reasonable design of printed board structure);
(2) Wiring rules;
(3) The minimum channel width is planned according to the device current density; Pay special attention to the channel wiring at the junction;
(4) Large current lines shall be surface as far as possible; If the requirements cannot be met, the use of bus bars can be considered;
(5) The thermal resistance of the contact surface shall be minimized. Therefore, the heat conduction area should be increased; The contact plane shall be flat and smooth, and can be coated with thermal conductive silicone grease if necessary;
(6) Stress balance measures shall be considered for thermal stress points and bold lines shall be added;
(7) The heat dissipation copper sheet shall be fenestrated by means of heat dissipation stress elimination and heat dissipation resistance welding;
(8) Copper foil with large surface area shall be used if possible;
(9) Large pads are used for the grounding mounting holes on the printed circuit board to make full use of the mounting bolts and the copper foil on the surface of the printed circuit board for heat dissipation;
(10) Place as many metalized vias as possible, and the aperture and disk surface shall be as large as possible, relying on vias to help heat dissipation;
(11) Supplementary means for heat dissipation of PCB devices;
(12) Under the condition that large area copper foil can be used, additional radiator can not be used for economic reasons;
(13) Calculate the appropriate surface heat dissipation copper foil area according to the device power consumption, ambient temperature and allowable maximum junction temperature (guarantee principle tj ≤ (0.5~0.8) tjmax).
然后
聯(lián)系
電話熱線
13410863085Q Q
微信
- 郵箱