
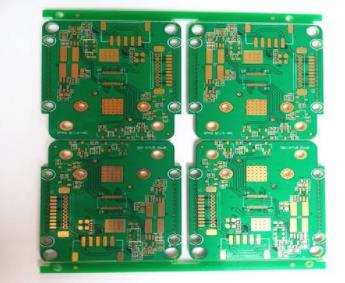
The second half of the explanation of high-speed circuit board design problems
circuit board manufacturers, circuit board designers and PCBA manufacturers explain high-speed circuit board design problems to you, and answer the second half
16. Can you introduce some foreign technICal books and data on high-speed PCB design?
Nowadays, high-speed digital circuits are used in communication networks, calculators and other related fields. In terms of communication network, the working frequency of PCB board has reached GHz, and the number of layers is up to 40 as far as I know. Due to the progress of the chip, the highest working frequency on the board of a general PC or server has reached more than 400MHz (such as Rambus).
In response to the demand for high-speed and high-density routing, the demand for blind/buried vias, mirrovias and build up processes is also increasing. These design requirements can be mass produced by manufacturers.
17. Two frequently referenced characteristic impedance formulas:
Microstrip Z={87/[sqrt (Er+1.41)]} ln [5.98H/(0.8W+T)], where W is the line width, T is the copper sheet thickness of the routing, H is the distance from the routing to the reference plane, and Er is the dielectric constant of the PCB material.
This formula can only be applied when 0.1<(W/H)<2.0 and 1<(Er)<15.
Stripline Z=[60/sqrt (Er)] ln {4H/[0.67 π (T+0.8W)]}, where H is the distance between two reference planes, and the routing is in the middle of the two reference planes. This formula can only be applied when W/H<0.35 and T/H<0.25.
18. Can a ground wire be added in the middle of the differential signal line?
Generally, the differential signal cannot be grounded. Because the most important point of differential signal application principle is to use the benefits of coupling between differential signals, such as flux cancellation, noise immunity, etc. If a ground wire is added in the middle, the coupling effect will be destroyed.
19. Does rigid flexible plate design require special design software and specifications? Where can we undertake such PCB processing in China?
Flexible printed circuit can be designed with general PCB design software. It is also produced by FPC manufacturers in Gerber format. Because the manufacturing process is different from the general PCB, each manufacturer will have its own * * for the minimum line width, minimum line spacing and minimum aperture (via) according to their manufacturing capacity. In addition, copper sheet can be laid at the turning point of the Flexible circuit board for reinforcement. As for the manufacturer, it can be found by using "FPC" as the keyword query.
20. What is the principle of properly selecting the grounding point between PCB and housing?
The principle of selecting PCB and housing grounding point is to use the chassis ground to provide a low impedance path to the return current and control the path of the return current. For example, it is usually possible to connect the PCB layer with the chassis ground near the high-frequency device or clock generator by using the fixing screws to minimize the area of the entire current loop, and thus reduce electromagnetic radiation.
21. What aspects should the circuit board DEBUG start from?
As far as digital circuits are concerned, first determine three things in sequence:
1. Confirm that all power values meet the design requirements. Some systems with multiple power supplies may require some specifications for the sequence and speed of the power supplies.
2. Confirm that all clock signal frequencies work normally and there is no non monotonic problem on the signal edge.
3. Confirm whether the reset signal meets the specification requirements. If all these are normal, the chip should send the first cycle signal. Next, debug according to the system operation principle and bus protocol.
22. When the size of the circuit board is fixed, if more functions need to be included in the design, it is often necessary to increase the wiring density of the PCB. However, this may lead to increased mutual interference of the wiring, and at the same time, too thin wiring will not reduce the impedance. Please introduce the skills in high-speed (>100MHz) high-density PCB design?
When designing high-speed and high-density PCBs, we should pay special attention to crosstalk because it has a great impact on timing and signal integrity. The following points should be noted:
Control the continuity and matching of the characteristic impedance of the wiring.
The size of the wire spacing. Generally, the spacing is twice the line width. Through SIMulation, we can know the influence of routing distance on timing and signal integrity, and find out the minimum tolerable distance. Different chip signals may have different results.
Select the appropriate termination method.
Avoid that the routing directions of the two adjacent layers are the same, or even that the two layers overlap, because the crosstalk is greater than that of the adjacent layers.
Use blind/buried via to increase the routing area. However, the production cost of PCB will increase. It is really difficult to achieve full parallelism and equal length in actual implementation, but we should try our best to do so.
In addition, differential termination and common mode termination can be reserved to mitigate the impact on timing and signal integrity.
23. LC circuit is often used for filtering at analog power supply. But why is LC filtering worse than RC filtering sometimes?
The comparison of LC and RC filtering effects must consider whether the frequency band to be filtered and the inductance value are properly selected. Because the inductance is related to the inductance value and frequency. If the noise frequency of the power supply is low and the inductance value is not large enough, the filtering effect may not be as good as RC. However, the cost of using RC filtering is that the resistor itself will consume energy, and the efficiency is poor. In addition, attention should be paid to the power that the selected resistor can withstand.
24. What is the method of selecting inductance and capacitance value when filtering?
The selection of inductance value shall consider not only the noise frequency to be filtered, but also the reaction ability of instantaneous current. If the LC output terminal has the opportunity to output a large current instantaneously, the inductance value is too large to hinder the speed of this large current flowing through the inductor, increasing ripple noise.
The capacitance value is related to the ripple noise specification value that can be tolerated. The SMAller the ripple noise value is required, the larger the capacitance value will be. The capacitor ESR/ESL will also have an impact. In addition, if the LC is placed at the output end of the switching regulation power, pay attention to the influence of the pole/zero generated by the LC on the stability of the negative feedback control circuit.
25. How to meet EMC requirements as much as possible without causing too much cost pressure?
The increased cost of EMC on PCB is usually due to the increase of the number of layers to enhance the shielding effect and the addition of high-frequency harmonic suppression devices such as ferrite beam and choke. In addition, the shielding structure of other institutions is usually required to make the whole system pass the EMC requirements. Here are just a few ways to reduce the electromagnetic radiation effect generated by the circuit in terms of PCB design skills.
Devices with slow signal slope rate shall be selected as far as possible to reduce the high-frequency components generated by the signal.
Pay attention to the placement of high-frequency components, and do not be too close to external connectors.
Pay attention to the impedance matching of high-speed signals, the routing layer and its return current path to reduce high-frequency reflection and radiation.
Place enough and appropriate decoupling capacitors on the power supply pins of each device to mitigate the noise on the power supply layer and stratum. Pay special attention to whether the frequency response and temperature characteristics of the capacitor meet the design requirements.
The ground near the external connector can be properly separated from the stratum, and the ground near the connector can be connected to the chassis ground.
The ground guard/hunt traces can be properly used beside some signals with high speed. However, we should pay attention to the influence of guard/hunt traces on the characteristic impedance of the wiring.
The power layer is 20H smaller than the formation, and H is the distance between the power layer and the formation.
26. When there are multiple digital/analog function blocks in a PCB, the conventional practice is to separate digital/analog/ground. Why?
The reason for separating D/A from ground is that the digital circuit will generate noise in the power supply and ground when switching between high and low potentials. The size of the noise is related to the speed and current of the signal. If the ground plane is not divided and the noise generated by the digital area circuit is large and the analog area circuit is very close, the analog signal will still be interfered by the ground noise even if the digital and analog signals do not intersect. That is to say, the digital analog ground undivided mode can only be used when the analog circuit area is far away from the digital circuit area that generates large noise.
27. Another method is to ensure that the digital/analog signal is laid out separately, and the digital/analog signal wiring is not crossed with each other. The whole PCB ground is not divided, and the digital/analog ground is connected to this ground plane. Why?
The requirement that the routing of digital and analog signals cannot cross is that the return current path of a faster digital signal will flow back to the source of the digital signal as far as possible along the ground near the lower part of the routing. If the routing of digital and analog signals crosses, the noise generated by the return current will appear in the analog circuit area.
28. How to consider impedance matching when designing high-speed PCB design schematics?
When designing high-speed PCB circuits, impedance matching is one of the elements of design. The impedance value has an absolute relationship with the routing method. For example, when walking on the surface layer (microstrip) or the inner layer (stripe/double stripe), the distance from the reference layer (power layer or stratum), the routing width, PCB material, etc. will affect the characteristic impedance value of the routing. That is to say, the impedance value can be determined only after wiring.
The general simulation software can't take into account some discontinuous impedance wiring due to the * * of the line model or the mathematical algorithm used. At this time, only some terminators (such as series resistance) can be reserved on the schematic diagram to mitigate the effect of discontinuous impedance. The real fundamental solution to the problem is to avoid impedance discontinuity when wiring.
29. Where can we provide a more accurate IBIS model base?
The accuracy of IBIS model directly affects the simulation results. Basically IBIS can be regarded as the electrical characteristic data of the actual chip I/O buffer equivalent circuit, which can generally be converted from the SPICE model (measurement can also be used, but * * more). The SPICE data has an absolute relationship with the Chip Manufacturing, so the SPICE data of the same device provided by different chip manufacturers are different, and the data in the converted IBIS model will also vary accordingly.
That is to say, if manufacturer A's devices are used, only they can provide accurate model data of their devices, because no one knows better than them what process their devices are made by. If the IBIS provided by the manufacturer is inaccurate, the fundamental solution is to constantly require the manufacturer to improve.
30. When designing high-Speed PCB, what aspects should designers consider the rules of EMC and EMI?
Generally, radiation and conducted shall be considered simultaneously in EMI/EMC design The former belongs to the part with higher frequency (>30MHz) and the latter belongs to the part with lower frequency (<30MHz) Therefore, we should not only pay attention to the high frequency and ignore the low frequency
A good EMI/EMC design must consider the location of components, PCB stack arrangement, important online routing, and component selection at the beginning of the layout. If there is no better arrangement in advance, it will take twice the effort and increase the cost if it is resolved afterwards
For example, the position of the clock generator should not be close to the external connector as far as possible, the high-speed signal should go through the inner layer as far as possible and pay attention to the characteristic impedance matching and the continuity of the reference layer to reduce reflection, the slope rate of the signal pushed by the device should be as small as possible to reduce the high-frequency component, and when selecting the decoupling/bypass capacitor, pay attention to whether its frequency response meets the requirements to reduce the power layer noise
In addition, pay attention to the return path of high-frequency signal current to minimize the loop area (that is, the loop impedance is as small as possible) to reduce radiation The range of high-frequency noise can also be controlLED by dividing the stratum Finally, properly select the chassis ground between PCB and housing. The circuit board manufacturer, circuit board designer and PCBA manufacturer will explain the design problems of high-speed circuit boards to you.
然后
聯(lián)系
電話熱線
13410863085Q Q
微信
- 郵箱