
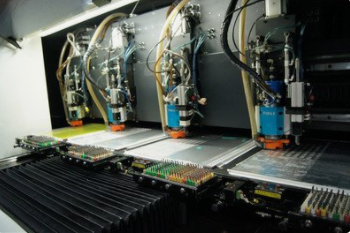
In PCB design, power supply is a topIC that cannot be ignored. Especially now, the power supply voltage of many PCB products is getting lower and lower, and the current is getting higher and higher, often hundreds of amperes. Therefore, people are paying more and more attention to the integrity of power supply. This article focuses on some problems of PCB power voltage drop.
Theoretically, the calculation of voltage drop should be applied to the physics knowLEDge of junior high school. The power voltage drop<v * tolerance=i * r (DC resistance) can be said to be very SIMple. The method of reducing voltage drop is also well known, as long as the DC impedance on the power supply path and the return path is reduced. Therefore, when designing PCBs, PCB layout engineers must often hear the following requirements:
please replace these 8mil SMAll holes with 16mil large holes.
this power supply can't be changed many times, please adjust it.
replace this power supply layer with 2OZ copper foil.
Many confident PCB engineers may think that it is not just the current carrying capacity. I have calculated the number of vias and the width of copper sheet according to the empirical formula. The power supply must be appropriate. There can be no problem. I am past the age when I will be easily fooled.
In fact, does the voltage drop only depend on the voltage of the electrical terminal? No, the power voltage drop is a system that affects the whole body. Modifying any parameter in the system will affect the final result. To understand this system, you need to know the flow direction of the power supply.
Talk about pressure drop in simple terms
The upper part is a power plane. The MARKed route is the part with the highest current density. The green part is the nearest path from the power supply to the return ground plane. It can be seen from the above that the closer the path is, the more current will flow through it. Like us, we prefer to take shortcuts. We want to take the path with less resistance to save our strength to the power end.
This characteristic will lead to high current density in some areas and high current through some vias. Therefore, instead of adding a corresponding number of vias according to the empirical formula, the current will pass through the vias in an average distribution manner. This causes the current passing through some vias to exceed the capacity range. After the board is used for a period of time, the middle of the vias may break, affecting the life of the vias and the service cycle of the board. Therefore, for some high current power supplies, if the vias are added neatly, it may affect the size of the vias current. At this time, it is tricky to add vias, and the higher the vias current near the power supply output, so it is recommended to use simulation to guide the addition of vias array.
The same is true for the current density. The current density will be relatively high on the nearest path between the power output and the power consumption. If the nearest path is exactly the bottleneck area, you need to modify the power path.
Another factor also affects the voltage drop of the power supply, which is temperature and wind speed. The temperature mainly affects the resistivity of the conductor. As the temperature rises, the resistivity will increase, and the DC resistance in the conductor will also increase. Therefore, in the case of large power consumption, heat dissipation should also be considered in power supply design.
To sum up, when designing PCB power supply, in addition to meeting the current carrying copper sheet width and the number of vias, we also need to pay attention to the current size of each circuit board vias, the current density on the power path, the working environment of the board, temperature rise and other factors.
Explain the power voltage drop in PCB design in simple terms
In PCB design, power supply is a topic that cannot be ignored. Especially now, the power supply voltage of many PCB products is getting lower and lower, and the current is getting higher and higher, often hundreds of amperes. Therefore, people are paying more and more attention to the integrity of power supply. This article focuses on some problems of PCB power voltage drop.
Theoretically, the calculation of voltage drop should be applied to the physics knowledge of junior high school. The power voltage drop<v * tolerance=i * r (DC resistance) can be said to be very simple. The method of reducing voltage drop is also well known, as long as the DC impedance on the power supply path and the return path is reduced. Therefore, when designing PCBs, PCB layout engineers must often hear the following requirements:<p="">
"XX worker, please replace these 8mil small holes with 16mil large holes."
"XX worker, this power supply can't be changed many times, please adjust it."
"XX worker, replace this power supply layer with 2OZ copper foil."
Many confident PCB engineers may think that it is not just the current carrying capacity. I have calculated the number of vias and the width of copper sheet according to the empirical formula. The power supply must be appropriate. There can be no problem. I am past the age when I will be easily fooled.
In fact, does the voltage drop only depend on the voltage of the electrical terminal? No, the power voltage drop is a system that affects the whole body. Modifying any parameter in the system will affect the final result. To understand this system, you need to know the flow direction of the power supply.
Talk about pressure drop in simple terms
The upper part is a power plane. The marked route is the part with the highest current density. The green part is the nearest path from the power supply to the return ground plane. It can be seen from the above that the closer the path is, the more current will flow through it. Like us, we prefer to take shortcuts. We want to take the path with less resistance to save our strength to the power end.
This characteristic will lead to high current density in some areas and high current through some vias. Therefore, instead of adding a corresponding number of vias according to the empirical formula, the current will pass through the vias in an average distribution manner. This causes the current passing through some vias to exceed the capacity range. After the board is used for a period of time, the middle of the vias may break, affecting the life of the vias and the service cycle of the board. Therefore, for some high current power supplies, if the vias are added neatly, it may affect the size of the vias current. At this time, it is tricky to add vias, and the higher the vias current near the power supply output, so it is recommended to use simulation to guide the addition of vias array.
The same is true for the current density. The current density will be relatively high on the nearest path between the power output and the power consumption. If the nearest path is exactly the bottleneck area, you need to modify the power path.
Another factor also affects the voltage drop of the power supply, which is temperature and wind speed. The temperature mainly affects the resistivity of the conductor. As the temperature rises, the resistivity will increase, and the DC resistance in the conductor will also increase. Therefore, in the case of large power consumption, heat dissipation should also be considered in power supply design.
To sum up, when designing PCB power supply, in addition to meeting the current carrying copper sheet width and the number of vias, we also need to pay attention to the current size of each circuit board vias, the current density on the power path, the working environment of the board, temperature rise and other factors.
然后
聯(lián)系
電話熱線
13410863085Q Q
微信
- 郵箱