鑫景福致力于滿足“快速服務(wù),零缺陷,輔助研發(fā)”PCBA訂購(gòu)單需求。

PCBA方案設(shè)計(jì)
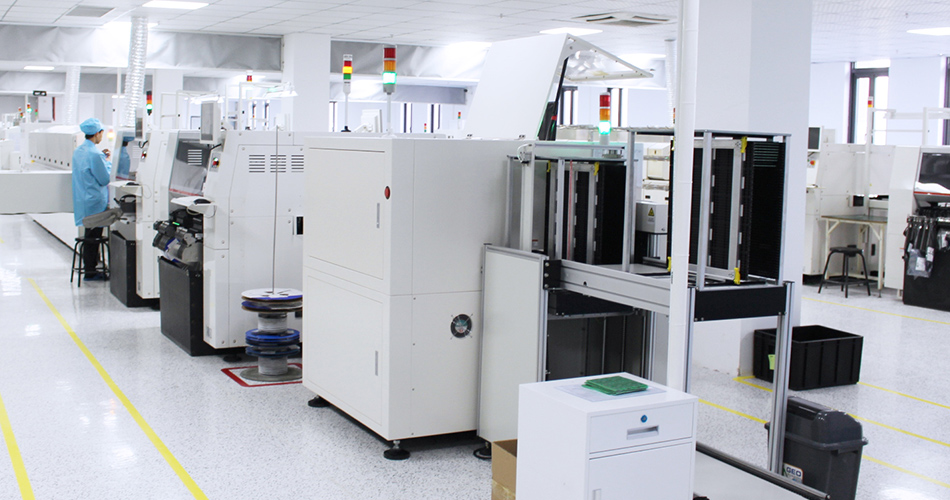
28 key indICators of production and manufacturing in PCBA processing plant
There are three main indicators to measure the success of an enterprise, namely employees, turnover and profit growth; There are also three main indicators to measure the success of manufacturing management in an enterprise, namely, manufacturing cycle, resource efficiency and process stability.
PCBA processing plant needs to set performance indicators for work order, equipment, personnel and quality based on these three weather vanes to measure whether the manufacturing process of the enterprise is excellent. If we can't correct definition make KPI, will not be able to use information technology systems to support our appraisal six manufacturing business processes (production control, production preparation, planning and production scheduling, quality control, equipment maintenance and management information) to see if there is optimizing space, each of the high order business goals are associated with several key indicators.
MESA (Manufacturing Enterprise Solutions Association) has sponsored research over the past several years to help manufacturing MARKets identify the most important metrics and to help decision makers understand indicator improvement and its relationship to metrics planning and software solution usage. As part of the latest indicator survey, these 28 manufacturing indicators were identified as the most used by discrete, process, and hybrid/batch manufacturers.
In the following, the 28 KPIs will be classified and elaborated:
Improve customer experience and responsiveness
1. On-Time Delivery to Commit -- This metric is the percentage of completed products that the manufacturer has delivered to the customer as promised.
2. Manufacturing Cycle Time -- measuring the time needed from the order delivery to the beginning of the production process to the completion of the finished product production.
3. Time to Make Changeovers -- a measure of how fast or fast it takes to convert a production line or plant from producing one product to producing different ones.
Second, improve quality
4. First Pass Yield -- indicates the percentage of products that are correctly manufactured for the first time in the manufacturing process and meet the specifications, without waste or rework.
5. Customer rejection /Return Material authorization/return Customer Rejects/Return Material Authorizations /Returns -- Measure the number of times customers reject products or request returns based on bad or substandard products received.
6. Supplier's Quality Incoming -- Measures the percentage of quality materials entering the manufacturing process from a designated supplier.
Third, improve efficiency
7, production capacity Throughput -- measuring the number of products produced by machines, production lines, equipment or factories in a specified period of time.
8. Capacity Utilization -- indicates the proportion of capacity utilization at a given time point.
9. Overall Equipment Efficiency (OEE) -- This multidimensional measure is a multiplier of availability x performance x quality. OEE can be used to indicate the overall effectiveness of a production facility or an entire production line.
10, Schedule or Production performance - the percentage of time to reach the target production level within the specified time.
Four, reduce inventory
11, WIP \ flow WIP Inventory/Turns -- a ratio calculation commonly used to measure the effective use of inventory materials. It is calculated by dividing the cost of goods sold by the average inventory used to produce those goods.
V. Guarantee compliance
12. Reportable Health and Safety Incidents -- measure the number of actual accidents or threatening health and safety incidents occurred during a period of time.
13. Reportable Environmental Incidents -- measure the number of environmental accidents occurred during a period of time.
14, Number of Non-Compliance Events/Year -- a measure of the number of times a factory exceeds normal regulatory compliance rules in a year. Complete documentation of specific noncompliance times, causes, and solutions is required.
Six, reduce maintenance
15. Planned Maintenance Work Orders vs. Emergency Maintenance Work Orders -- This ratio is an indicator of the frequency of planned maintenance, not more disruptive/unplanned maintenance.
Downtime to Operating Time -- The ratio of downtime to operating time is a direct indicator of the availability of production assets.
7. Enhance flexibility and innovation
17. Rate of New Product Introduction - describes how quickly a new product can be introduced to the market and usually includes a combination of design, development, and manufacturing acceleration times.
18, Engineering Change Order Cycle Time -- Measure the speed of design change or modification of existing products, which can be achieved through documentation process and mass production.
Reduce costs and improve profitability
19. Total Manufacturing Cost per Unit (Excluding material) Excluding Materials - This is a measure of the total possible controllable manufacturing cost for a given manufacturing unit, item or quantity.
20. Manufacturing Cost as a Percentage of Revenue -- the ratio of total manufacturing cost to the total revenue of a manufacturing plant or business unit.
21. Net Operating Profit - A measure of the financial profitability of all investors/shareholders/creditors of a manufacturing plant or business unit, either before or after tax.
22, Productivity in Revenue per Employee - This is a measure of the revenue generated by a plant, business unit or company divided by the number of employees.
Margin - This measure is calculated by dividing the profit margin generated by a manufacturing plant or business Unit by a given unit or output.
24. Return on Assets/Return on Net Assets -- a measure of financial performance calculated by dividing the net income of a manufacturing plant or business unit by the value of deployed fixed assets and working capital.
25. Energy Cost per Unit - Measures the cost of energy (electricity, steam, oil, gas, etc.) needed to produce a given unit or volume of production.
26. Cash-to-Cash Cycle Time -- This measure is the duration between the purchase of inventory in a manufacturing facility or business unit and the amount of money receivable/payable (usually in days) collected for the sale of products that use inventory.
27. EBITDA -- This acronym stands for Earnings before interest, taxes, Depreciation and amortization. It calculates the earnings of a business unit or company before subtracting any interest, taxes, depreciation and amortization from the final accounting treatment of revenues and expenses. EBITDA is often used as a top indicator of a company's current operating profitability.
28. Customer demand satisfaction Rate/ On-Time delivery/ Perfect Order Percentage Customer Fill rate/on-time delivery/ Perfect order percentage -- This index refers to all products ordered by customers. The percentage of times that correct specifications are met and delivered on time as expected.
conclusion
The recognition degree of the importance of the above KPIs varies with different enterprises and industries, so it can only be used as a reference. More importantly, for the application of key indicators, many manufacturing enterprises have not carried out relevant KPI measurement work, only qualitative judgment. In the future, the application of KPI will become more and more important and will become the objective basis for improvement evaluation of pcb manufacturing related projects.
點(diǎn)擊
然后
聯(lián)系
然后
聯(lián)系
電話熱線
13410863085Q Q
微信
- 郵箱