
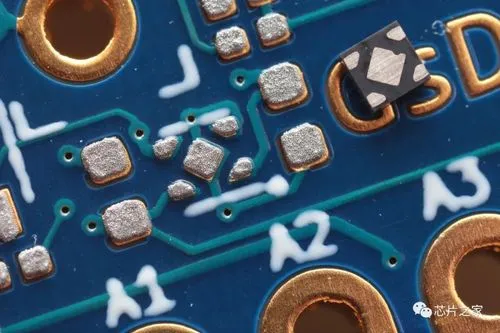
The 32 layer PCB rapid proofing is in the circuit board. If there is signal transmission, it is expected that the signal can be transmitted to the receiving end smoothly from the sending end of the power supply with the minimum energy loss, and the receiving end will fully absorb it without any reflection. To achieve this kind of transmission, the impedance in the line must be equal to the impedance inside the transmitter to be calLED "impedance matching". When designing high-speed PCB circuits, impedance matching is one of the elements of design. The impedance value is absolutely related to the wiring mode. For example, whether to walk on the surface layer (MICrostrip) or the inner layer (Stripline/Double Stripline), the distance from the reference power layer or layer, PCB routing width, PCB material, etc. will affect the characteristic impedance value of the routing. In other words, the impedance value can only be determined after wiring, and the characteristic impedance produced by different products also has slight difference. General SIMulation software can't take into account some discontinuous impedance wiring due to the limitation of the line model or the mathematical algorithm used. At this time, only some terminators, such as series resistors, can be reserved on the schematic diagram to mitigate the effect of discontinuous impedance wiring. The real fundamental solution to the problem is to avoid impedance discontinuity when wiring.
Process Flow and Technology of Multilayer board
Core board production - laminated RCC - laser drilling - hole electroplating - pattern transfer - etching and film stripping - laminated RCC - integrated printed circuit board (HDI/BUM board) that is repeatedly formed into an anb structure.
A - is the number of layers on one side, n - is the core board, and b - is the number of layers on the other side.
The guarantee of performance depends on PCB design, which everyone has realized. The performance test results of the same logic connection, the same device and different PCBs are different. Good design not only has high stability, but also can pass various demanding tests. But it is impossible to achieve this effect if the design is not ideal. In some low-end products, many manufacturers use the same chipsets and similar logical connections. The only difference is the level of PCB design. The difference of products is mainly reflected in PCB design. Fast proofing of 32 layer circuit board
The ease of processing is also an important indicator of PCB design. Good PCB design is convenient for processing, maintenance, testing and manufacturing. The quality of PCB is not only related to the production efficiency of PCB manufacturers and SMT manufacturers, but also to the convenience of our testing and debugging.
The difference between hardware and software of PCB board
It is divided into rigid circuit board, Flexible circuit board and soft and hard combination board.
The visual difference between rigid PCB and flexible PCB is that flexible PCB can be bent. The common thickness of Rigid PCB board is 0.2mm, 0.4mm, 0.6mm, 0.8mm, 1.0mm, 1.2mm, 1.6mm, 2.0mm, etc. The common thickness of flexible PCB is 0.2mm. Thickening layer will be added at the back of the part to be welded. The thickness of the thickening layer varies from 0.2mm to 0.4mm. The purpose of understanding these is to provide structural engineers with a spatial reference when designing. Common materials of rigid PCB board include phenolic paper laminate, epoxy paper laminate, polyester glass felt laminate, and epoxy glass cloth laminate; Common materials of Flexible PCB board include: polyester film, polyimide film, fluorinated ethylene propylene film.
Process requirements for fast proofing of 32 layer PCB
2.1 Process requirements for component processing
2.1.1 Before the components are inserted, the solderability of the components must be treated. If the solderability is poor, the components' pins must be tinned first.
2.1.2 After the pins of components are shaped, the pin spacing shall be consistent with the bonding pad hole spacing corresponding to the pcb board.
2.1.3 The shape of component pin processing shall be conducive to heat dissipation during component welding and mechanical strength after welding.
2.2 Process requirements for component insertion on PCB
2.2.1 The insertion sequence of components on PCB board is from low to high, from SMAll to large, from light to heavy, from easy to difficult, from general components to special components, and the installation of the previous process shall not affect the installation of the next process.
2.2.2 After the components are inserted, their MARKs shall be read from left to right as far as possible in a direction that is easy to read.
2.2.3 Polarity of components with polarity shall be installed in strict accordance with the requirements of the drawings, and wrong installation is not allowed.
2.2.4 The insertion of components on PCB board shall be evenly distributed, neatly arranged and beautiful, and oblique arrangement, vertical crossing and overlapping arrangement are not allowed; One side is not allowed to be high while the other side is low; It is also not allowed that one side of the pin is long and the other side is short.
2.3 Process requirements for PCB solder joints
2.3.1 The mechanical strength of welding points shall be sufficient
2.3.2 Reliable welding to ensure conductivity
2.3.3 The surface of welding points shall be smooth and clean
The demand for 94HB single-sided cardboard proofing is not very large, so it is impossible to put a large number of 94HB single-sided cardboard panels together for proofing, but to use a single sheet for production. Therefore, the cost is generally 200. Many people are also surprised that 94HB single-sided cardboard is a paper substrate, which is a relatively cheap product, while FR-4 fiberglass board is a mid end product. This is why the price of proofing is still expensive.
FPC chEMIcal nickel gold is a popular term, and the correct term should be called nickel leaching gold (EN/IG) No additional current is required for the formation of chemical nickel layer. With the action of reducing agent (such as sodium dihydrogen hypophOSPhite NaH2PO2, etc.) in the bath solution, continuous deposition of nickel phosphorus alloy layer can be carried out on the activated metal surface to be plated at high temperature. The chemical nickel layer can be used as a shielding layer for metal atom migration to prevent copper from diffusing to the gold coating
As for gold DIPping, it is a typical displacement reaction without reductant When the chemical nickel surface enters the gold leaching bath, the gold layer is deposited on the nickel metal at the same time as the nickel layer is dissolved and thrown away Once the nickel surface is completely covered by the gold layer, the deposition reaction of the gold layer gradually stops and it is difficult to increase to a certain thickness As for another series of thickened gold, strong reducing agent is needed to gradually thicken the gold layer.
PCB PCB proofing
Nickel alloy has solderability and can also provide a substrate for IC chip wiring (Au/Al wire). It has been widely used in PCB design
In fact, the welding strength of the solder joints formed by plated nickel gold to the parts is almost all built on the surface of the nickel layer. The purpose of gold plating is to protect the nickel surface from passivation or oxidation in the air and maintain the minimum solderability The gold layer itself is completely unsuitable for welding, and the strength of its solder joints is also very poor
At the moment of high temperature welding of circuit boards, gold and tin have already formed different forms of interface alloy compounds (such as AuSn, AuSn2, AuSn4, etc.) and escaped. Therefore, the real basis of solder joints are all landed on the nickel surface, and the strength of solder joints has nothing to do with gold That is to say, the tin in the solder will form Ni3Sn4 interface alloy eutectic with pure nickel The thin gold layer will disperse quickly in a short time and slip into a large amount of solder, so the gold layer can not form reliable solder joints at all
Therefore, if the nickel layer is too thin (less than 3um - 5um) to provide a good solder base, SMT reflow solder will fall off or have poor adhesion
In the production process of FPC, in order to save costs, improve production efficiency and shorten the production cycle, it will adopt the method of patchwork instead of single piece production. There are several principles to follow when assembling FPC.
1. On the premise that each process can be produced, try to "squeeze" the plate. The so-called "extrusion" is to reduce the distance between adjacent plates, so as to reduce the size of the whole plate assembly, save production materials and reduce production costs.
2. The spacing between single plates shall be at least 2.5mm. First of all, this is to meet the requirements for positioning holes. In the process of mass production, die stamping is generally used for molding. In order to enhance the accuracy of die stamping, positioning holes need to be placed between each piece in the assembly to avoid the offset of die stamping, which will lead to the scrapping of FPC; In the process of sample production, laser cutting is generally used for forming. In order to avoid slight deviation and avoid deviation of one piece and the whole piece, single pieces cannot be directly connected, so that they do not affect each other.
3. Etched characters shall be added to the plate assembly, and the size and quantity of the plate assembly shall be briefly described, so as to facilitate the check and verification in subsequent production.
4. Add positioning holes at the four corners of the whole assembly, and select one corner to mark different positioning holes, so as to keep the direction consistent in the subsequent process production, so as not to lead to the return of film sealing and character printing.
5. The width of the plate shall be fixed as 250mm and the length shall be within 250mm as far as possible. The larger the size of the plate, the greater the offset, the worse the production precision, and the higher the defective rate of finished products.
After knowing the five principles that need to be followed, I will briefly introduce the three ways of composition.
1. Regular composition. The pattern is directly arranged in the direction of a single piece, which is most suitable for FPC pattern with regular shape, such as rectangle, square, circle, ellipse, etc;
2. Oblique splicing. Tilt the single piece to a certain extent, and then array it, so as to maximize the use of the space for the assembly, such as the curved bars, folds, etc;
3. Reverse stitching. That is, combine one positive and one negative of a single PCS.
All splicing methods shall follow the principle of material saving on the premise of production.
In order to avoid electromagnetic radiation generated when high-frequency signals pass through the printed wire during the manufacturing process of industrial control medical double-sided pcb circuit board, the following points should also be noted when wiring the industrial control medical double-sided PCB circuit board:
1. Try to reduce the discontinuity of the wire on the industrial control medical double-sided PCB circuit board, for example, the wire width should not change suddenly, the corner of the wire should be greater than 90 degrees, and circular wiring is prohibited.
2. The clock signal lead is most likely to generate electromagnetic radiation interference. When wiring the industrial control medical double-sided PCB circuit board, it should be close to the ground circuit, and the driver should be close to the connector.
3. The bus driver shall be close to the bus to be driven. For those leads leaving the printed circuit board, the driver should be close to the connector.
4. A signal ground wire shall be clamped between every two signal wires for the wiring of data bus of industrial control medical double-sided PCB circuit board. It is better to place the ground loop close to the least important address lead, because the latter often carries high-frequency current.
5. When arranging high-speed, medium speed and low-speed logic circuits on the printed board, the components shall be arranged
6. The industrial control medical double-sided PCB circuit board can suppress reflection interference. In order to suppress the reflected interference at the terminals of printed lines, except for special needs, the length of printed lines should be shortened as much as possible and slow speed circuits should be used. If necessary, terminal matching can be added, that is, a matching resistor with the same resistance value can be added at the end of the transmission line to the ground and the power supply. According to experience, for general fast TTL circuits, terminal matching measures should be taken when the line length of industrial control medical double-sided PCB circuit board is more than 10cm. The resistance value of the matching resistance shall be determined according to the maximum value of the output drive current and the absorption current of the integrated circuit.
然后
聯(lián)系
電話熱線
13410863085Q Q
微信
- 郵箱