
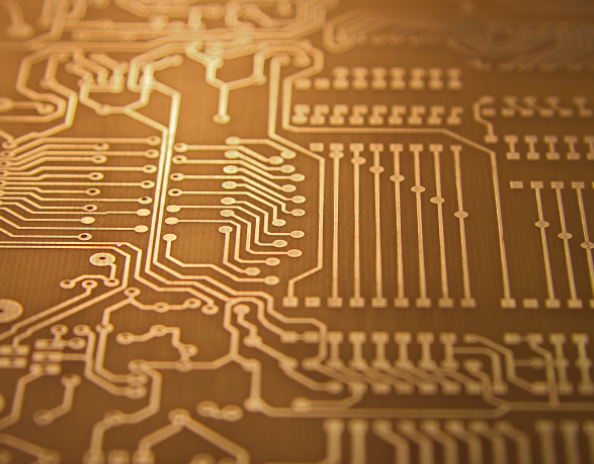
EMC design Based on PCB
1. troduction to PCB
PCB, whose Chinese name is printed circuit board, is an important supplier of electronIC components, electronIC component support and electronic component power connection Because it is made by electronic printing, it is calLED "printed" circuit board The inventor of the printed circuit board is Austrian Paul Eisler. In 1936, who used the printed circuit board in the radio device In 194.3, Americans widely used this technology in military radio In 1948, the United States officially recognized the invention for commercial use Since the mid 1950s, PCB technology has been widely adopted In printed circuit board, the interconnection between electronic components is realized by direct connection of wires Now, the circuit board only exists as an effective experimental tool; Printed circuit board plays a leading role in the electronic industry According to the number of circuit layers, it can be divided into single-sided, double-sided and multilayer boards The common Multilayer board is generally 4-layer board or 6-layer board, and the complex multilayer board can reach more than 10 layers
Printed circuit board
1. There are three main types of PCB boards for departments:
1) Single panel
A single-sided board is a basic PCB with parts concentrated on one side and wires on the other side. Because the wires only appear on one side, this type of PCB is called single-sided PCB because there are many strict restrictions on designing circuits for single boards, only early circuits use these types of boards
2) Double panel
The double sided circuit board has wiring on both sides This "bridge" between circuits is called via The via is a SMAll hole on the PCB, filled with metal or painted, which can be connected to the wires on both sides Because the area of the double-sided board is twice that of the single panel and the wiring can be staggered, it is more suitable for more complex circuits than the single-sided circuit board
3) Multilayer board
In order to increase the area that can be wired A printed circuit board with a double-sided inner layer, two single-sided outer layers, or two double-sided inner layers and two single-sided outer layers, is alternately combined with a positioning system and insulating bonding materials, and a conductive pattern printed circuit boards interconnected according to design requirements are divided into four layer and six layer printed circuit boards, also known as multilayer printed circuit boards The number of layers of a circuit board represents several independent wiring layers, usually an even number, including two outer layers Most motherboards are 4-8 layer structures, but technically, nearly 100 layers of PCB can be realized Most large supercomputers use multilayer mainboards, but because such computers can be replaced by many ordinary computer groups, the use of super multilayer boards has gradually stopped Because the layers in the PCB are closely connected, it is usually not easy to see the actual digital digits, but if you carefully observe the motherboard, you can still see them
According to the classification of hardware and software, it is divided into ordinary circuit board and Flexible circuit board PCB is the working platform of circuit components in electronic equipment It provides electrical connections between circuit components Its efficiency is directly related to the quality of electronic equipment With the rapid development of microelectronics technology and the improvement of circuit integration, the density of components pCB board is getting higher and higher, and the working speed of the system is getting faster and faster. This makes the electromagnetic compatibility design of PCB become more and more important, and becomes the key to the stable and normal operation of the system
2. Common EMI in PCB
There are two ways to solve the electromagnetic compatibility problem in PCB design: active reduction and passive compensation Therefore, it is necessary to analyze the interference source and propagation path of electromagnetic interference The EMI in PCB design usually includes conducted interference, crosstalk interference and radiated interference
2.1 Conducted interference
Conducted interference mainly affects other circuits through wire coupling and common mode impedance coupling. For example, if noise enters the system through the power circuit, all circuits using the power will be affected Figure 1 shows that noise is coupled through common mode impedance Circuits 1 and 2 use a common wire to obtain a supply voltage and a ground return If the voltage of circuit 1 suddenly needs to rise, then the voltage of circuit 2 must be caused by the common power source and the impedance between the two circuits decreases
2.2 Crosstalk interference
Crosstalk is when one signal line interferes with another adjacent signal path. It usually occurs on adjacent circuits and conductors, characterized by mutual capacitance and mutual inductance between circuits and conductors For example, the ribbon line on the PCB carries low-level signals. When the parallel line length exceeds 10cm, crosstalk interference will occur Because crosstalk may be caused by capacitance of electric field and mutual inductance of magnetic field, when considering crosstalk on PCB stripline, the main problem is to determine which of the coupling of electric field and magnetic field is the main factor
2.3 Radiated Interference
Radiated interference is the interference introduced by the radiation of space electromagnetic waves. The radiated interference in PCB is mainly the common mode current radiated interference between cable and internal trace When the electromagnetic wave radiates to the transmission line, the problem of field line coupling will occur The small voltage sources distributed along the line can be divided into common mode and differential mode components Common mode current refers to the current with small amplitude difference but the same phase on two wires, while differential mode current refers to the current on two wires with the same amplitude and opposite phase
3. Electromagnetic compatibility design of PCB
With the increasing density of electronic components and circuits on the PCB, in order to improve the reliability and stability of the system, corresponding measures must be taken to make the designed PCB meet the requirements of electromagnetic compatibility and improve the anti-interference efficiency of the system
3.1 Select PCB board
In PCB design, due to the mutual coupling of electromagnetic fields, signals on adjacent transmission lines will cross talk Therefore, when designing PCB electromagnetic compatibility, first consider the size of PCB If the PCB size is too large and the print line is too long, the impedance will inevitably increase, the noise resistance will be reduced, and the cost will also increase; If the size of PCB is too small, crosstalk may occur between adjacent transmission lines, and the heat dissipation efficiency is poor The number of layers of PCB board is determined according to the comprehensive factors of power supply, ground type, signal line density, signal frequency, signal quantity required for special wiring, surrounding elements, cost and price One of the methods of PCB EMC design is to meet the strict requirements of EMC, consider the manufacturing cost, and appropriately add ground plane For the power supply layer, the internal power layer division can usually meet the needs of multiple power supplies. However, if multiple power supplies are required and interlaced, two or more power supply planes must be considered For the signal layer, in addition to the wiring density of the signal line, from the EMC perspective, it is also necessary to consider the mask or isolation of key signals to determine whether to add corresponding layers
3.2 PCB layout design
The layout of the PCB should generally follow the following principles:
(1) Try to shorten the connection between high-frequency components and reduce their distribution parameters and mutual electromagnetic interference. Components susceptible to interference should not be too close together, and inputs and outputs should be as far away as possible
(2) There may be a high voltage between some components or wires
(3) The device with large heat generation should leave space for the heat sink The heating element shall be kept away from the heating element
(4) Arrange the position of each functional unit according to the circuit flow
(5) Take the component of each functional module as the center and arrange it around it to minimize and shorten the lead and connection length between components
(6) Comprehensively consider the distribution parameters among the components. The components shall be arranged in parallel as far as possible, which is not only conducive to improving the anti-interference ability, but also beautiful in appearance and easy to mass production
3.3 Layout design of components
Compared with discrete components, integrated circuit components have the advantages of good sealing, fewer solder joints, and low failure rate, which should be given priority At the same time, selecting equipment with a slower signal slope can reduce the high frequency components generated by the signal Making full use of SMD components can shorten the connection length, reduce impedance and improve electromagnetic compatibility When arranging components, first group them with a certain pipe, put them in the same group, and arrange incompatible components separately to ensure that components do not interfere with each other in space In addition, heavy components shall be secured with brackets
3.4 Wiring design PCB board
The general principle of PCB layout design is to lay clock and sensitive signal lines first, then lay high-speed signal lines and unimportant signal lines the following details need to be considered:
(1) In the multi-layer board wiring, a "well"-shaped network structure is used between adjacent layers;
(2) Reduce wire bending and avoid sudden change in wire width. The corners of the signal lines should be designed into arcs or connected with 45 degree broken lines;
(3) The distance between the outer conductors or components of the PCB is not less than 2mm from the edge of the PCB, which not only prevents the change of characteristic impedance, but also facilitates PCB clamping;
(4) For devices that must lay a large area of copper foil, they should be grid-shaped and connected to the ground through vias;
(5) Short and thin wires can effectively suppress interference The width of the wire depends on the current flowing through the wire Generally speaking, for copper with thickness of 0, the width is 1mm. The allowable current load of the foil is 1A For low power consumption digital integrated circuits, 0 line width is selectable from. 2 to 0.5mm In the same PCB, the width of ground wire and power wire should be greater than that of signal wire
然后
聯(lián)系
電話熱線
13410863085Q Q
微信
- 郵箱