
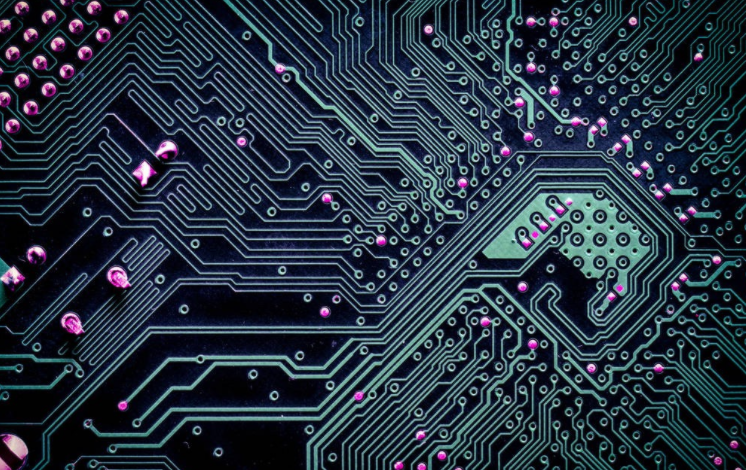
Failure Analysis of Welding Connection between FPGA and PCB
FPGAs are used in most electronIC PCB systems, including many commercial and national defense fields. Most FPGAs are packaged in BGA As soon as BGA appeared, it beCAMe the choice of high-density, high-performance, multi-functional, high I/VLSI chips (such as CPU and North South Bridge) for pin packaging Its features are:
1. Although my number of/O pins is increased, the pin spacing is much larger than QFP, thus improving the assembly yield;
2. Although its power consumption is increased, BGA can be welded by controlLED folding chip method, which can improve its electrical performance:
3. The thickness is reduced by more than 1/2. Compared with QFP, the weight is reduced by more than 3 times/4;
4. The frequency of use is greatly improved;
5. Coplanar welding can be used for assembly, with high reliability;
6. BGA packages are still the same as QFP and PGA, which occurs too much subordinate area;
PCB board
Solder joint failure failures frequently occur in FGPAs When FPGA is packaged in BGA package, FPGA is prone to solder failure The cause of welding failure cannot be isolated. Early detection is very difficult. Intermittent failures may be upgraded over time until the equipment is unreliable or inoperable However, as often happens, this problem can be solved. It is the Ridgetop group SJ-BIST Generally speaking, welding failure means that the welded joint breaks under certain conditions due to various factors (such as: stress, temperature, cloth, welding quality and actual working conditions, etc.)
What factors will cause the failure of welding connection?
Common failure reasons:
1) Stress-related failures-for devices in operation
Usefully, the defects of the cloth itself (such as chEMIcal composition inhomogenity, local micro cracks), hot cracks and cold cracks, incomplete penetration, slag inclusion, pores and undercuts in the weld caused by various reasons, etc., during welding The high residual stress in the near seam area (including the structural stress of the phase transformation of the weld and the heat affected zone), as well as structural softening under high temperature during welding and embrittlement after cooling, are the root causes of joint failure and joint failure Brittle fracture or expansion of the joint provides conditions At present, the statistical degradation model is used to predict the failure of welded joints However, because statistics are meaningful only when there are a large number of samples, models based on statistics are at best expedient SJ-BIST of Raytor Group can provide a direct, real-time method to measure and predict the failure of welded joints
2) Failures related to manufacturing production
Because solder joint failures also occur during the manufacturing process. The Ridegtop group SJ-BIST can detect the FPGAs that are not installed These manufacturing related failures have their own detection challenges Visual inspection is a method currently used to identify faults in the manufacturing environment The main disadvantage is that it is impossible to test and check the solder joints Visual inspection is limited to the solder joints on the external lines of the FPGA, while board size and other surface mounted components limit further visibility With the increase of BGA packaging array density, solder ball deviation becomes more strict In the fine pitch BGA package, there are thousands of pads with one. 0mm pitch and 0.60mm ball diameter. Under these conditions, pad tuning and insufficient welding become the main causes of pad disconnection and partial disconnection failures Even 100% x-ray inspection cannot guarantee that solder joint fracture is found when solder is not wetted on the pad Another defect involving penetration of solder balls and capillaries into plated vias is not easy to identify, even with X-ray imaging As an embedded soft core, Ridgetop Group SJ-BIST is indeed suitable for FPGA monitoring in PCB manufacturing environment
Definition of BGA package connection failure (for thermal cycling):
The industry's definition of BGA package connection failure is:
1) Peak resistance greater than 300 ohms for 200 ns or more.
2) 10 or more failure events occur 10% of the time after 1 failure event.
Types of Weld Failures:
1) Solder ball crack
Real time failure detection of soldered connections between a working FPGA and a PCB As time goes on, cracks may appear in the weld due to the damage of accumulated stress Cracks are common on the edges of devices welded to PCB Cracks can cause the solder ball to separate from the BGA package or PCB parts The typical crack location is between BGA package and solder ball. Another typical crack is PCB board and solder ball Continued damage to a cracked solder ball can lead to another type of failure - the solder ball breaks
2) Solder ball breakage
Real time failure detection of soldered connections between a working FPGA and a PCB Once cracks occur, subsequent stresses can cause the solder ball to crack Fracture leads to complete separation of solder ball and PCB board, resulting in long time in open circuit state, contamination and oxidation of fracture surface The end result is a degraded connection that creates an intermittent short circuit until a longer open circuit is formed
3) Missing solder balls
Subsequent mechanical stresses that lead to cracks, which may eventually lead to fracture or dislocation of fractured solder balls It is not only a missing solder ball that causes the connection of the pin to fail, but a solder ball that is misplaced may get stuck in another position, causing an unimaginable short circuit in another circuit
Electric signs of solder ball failure: regularly opening and closing the solder ball may cause intermittent electrical signal failure Vibration, movement, temperature changes, or other stresses can cause cracked solder balls to open and close, resulting in intermittent electrical signal failures The flexible data PCB factory used by the manufacturer also makes this intermittent signal possible, such as opening and closing caused by vibration stress, and unpredictable opening and closing of solder ball circuit will lead to intermittent signal This intermittent fault is difficult to diagnose In addition, the buffer circuit around the I/O FPGA can hardly measure the resistance of the welding network A device that fails in a working FPGA may pass without any fault finding (NTF) on the test bed because the solder joints are temporarily connected. Many users find that the FPGA does not work properly. It is for this reason that the FPGA will work normally by manually pressing the P key
Real time fault detection of welding connection between FPGA and FPGA When PCB is working, SJ-BIST detects welding status in real time At present, it is difficult to carry out X-ray and reliability tests for visual inspection and other technologies, vision and manufacturing industries, because the reflection is electrical When the equipment is not powered on, the signal fault is largely invisible Through early detection of impending faults, SJ-BIST supports condition based equipment maintenance to reduce intermittent faults Its superior sensitivity and sensitivity allow SJ-BIST to detect and fault high resistance within two clock cycles, as low as 100 ohms, without false alarm As an extensible solution, it can connect to the user's existing test center without adding additional resources
然后
聯(lián)系
電話熱線
13410863085Q Q
微信
- 郵箱