
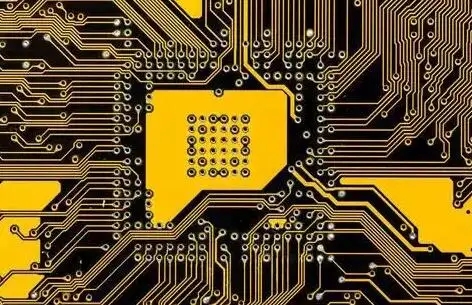
Analysis of phOSPhorus content in lead-free solders for circuit boards
The working environment affects some functions of electronIC products, such as keys or switches, and the reliability of the exposed metal film area will affect the products to some extent. Since these areas are not protected by green paint or other sealant, they must rely on their own ability to resist the corrosive environment, such as high humidity or polluting gases. The corrosion of various interconnection points on the board may lead to open circuit or short circuit. For the overall assembly of finished products, the final coating of the circuit board has become an important topic. In terms of long-term reliability, the films can also be used as a barrier layer for metal diffusion to protect the bottom copper pad from oxidation at high temperatures. The intermetallic metals (IMC) generated on the copper surface after welding can also play a buffer role for the MiSMAtchs of thermal expansion coefficient (CTE) between interfaces, without causing the silicon wafer to crack. However, such IMC itself should not have brittleness to make the strength of solder joints better.
1、 Analysis of the increase of phosphorus content on the interface
Tin silver copper lead-free solder was used to weld on ENIG surface with medium phosphorus (8.0 wt%) and high phosphorus (11.2 wt%) respectively, and then the growth of IMC was observed in depth. Figure 9 below is the red line MARKed on the section of the microsection to illustrate the scanning path of SEM.
There are two mechanisms for the increase of phosphorus content in some local areas of such interfaces, namely:
(1) When the phosphorus nickel alloy layer is immersed in gold water for displacement reaction, the pure nickel part is rapidly dissolved in gold water and gold is deposited, resulting in the remaining insoluble phosphorus between its interfaces.
However, when the high phosphorus nickel oxide surface is immersed in gold water, due to its strong corrosion resistance, the replacement reaction caused by the attack of gold water is also slowed down, so that the thickness of the gold layer is thinner than that of medium phosphorus nickel with low corrosion resistance.
This phenomenon can be seen from the fact that the gold thickness on the surface of the phosphorus nickel layer (8 wt%) under the same operating conditions is 0.08 μ m. 0.05 thick gold with high phosphorus nickel layer (11.2 wt%) μ The comparison of m can be completely clear.
It can be seen from the data collated in the test of the ENIG film of the former culture that the thickness of the gold layer under normal conditions ranges from 0.05-0.08 μ m. As for the increase of phosphorus content, it is less than 1%. However, in the vulnerable area near the grain boundary, the amount of phosphorus increases by more than 4%. Therefore, it is known that the tendency of "phosphorus increase" on the local interface of the nickel coating with strong corrosion resistance will also be slowed down after the gold leaching reaction.
(2) The further increase of phosphorus content downstream of the interface occurs in the welding reaction, that is, when pure nickel is melted by high-temperature liquid tin to form IMC, the phosphorus content left behind by nickel will naturally increase. At this time, if the corrosion resistance of the nickel coating is stronger, the increase trend of the local phosphorus content on the interface will also be smaller.
It can be seen from this that the phosphorus content on the interface of 11.2 wt% high phosphating nickel layer after welding is not obviously increased. Of course, it can be explained that the corrosion resistance is getting stronger, but in fact, in addition to the behavior of chEMIcal reaction, the high phosphorus nickel layer also has the physical characteristics of a flat surface. It can be clearly seen from the SEM magnified picture that the high phosphorus nickel surface is more flat than the medium phosphorus one, so the contact area provided in the welding reaction is also smaller, which inevitably weakens the trend of pure nickel dissolution. The explanation of this physical phenomenon can be further confirmed from the structure of IMC fattening and thickening after TC test.
At this moment, we can go back to the push ball test. The curve difference of "push ball and elongation" must be caused by the difference of IMC structure from the comparison between the benign gentle decline of the curve and the adverse brittle steep decline. The phosphorus content may not increase on the interface after welding for those with high phosphorus content. For the welding of 11.2 wt% high phosphorus nickel layer, the number of "phosphorus increase" on the interface will not affect the reliability. On the contrary, when the content of medium phosphorus is 8.0wt%, its "push ball and elongation" test does show great adverse changes in thrust.
2、 Comparison of tensile strength after stringing
(1) . Strength of aluminum wire
A total of 50 such tensile tests were carried out. In ENIG 5 μ The phosphorus content of the m-thick nickel layer varies from 4.2-11.6wt%, and the thickness of the gold layer in the middle phosphorus nickel layer is 0.08 μ m; However, the thickness of gold layer obtained by high phosphorus nickel layer [10.1 and 11.6 wt%] is only 0.05 μ m。
For the original ENIG sample or the sample aged at 155 ℃ for 4 hours, the average tension of the three standard deviations after wiring can reach 9.5 cN (± 0.75 cN), and is not affected by the phosphorus content. This value has already exceeded the 4cN required by the 2011 method in MIL-STD-883C to pass the standard.
(2) . Strength of gold thread
This tensile test has been conducted for 60 times in total. The two types of samples used are electroplated nickel gold and high phosphating nickel immersion gold (ENIG), which are deliberately used as reference samples for comparison of aging or original ENIG samples. The gold surface of both before wiring is cleaned by plasma. The phosphorus content in ENIG original sample is 11.2 wt%. The average tensile force of nickel gold electroplating is 13.9 cN, while the average tensile force of high phosphorus ENIG layer without plasma cleaning is 14.1 cN. As for the electroplated nickel gold surface without plasma cleaning, the average wire pulling force is only 13.3 cN.
The measured "average value of three standard deviations" (X-3S, which can cover 99.73% of various tensile test values) of the plasma cleaned electroplated nickel gold surface is 10.01 cN, while the average tensile force of the high phosphorus ENIG surface not cleaned by plasma is 9.9 cN, but the tensile force of the uncleaned electroplated nickel gold surface is only 8.8 cN.
3、 Conclusion
(1) When the gold layer of high phosphorus nickel is 0.05 μ M, its threading capacity can be equal to 0.08 of the medium phosphorus μ M gold layer. One of the reasons is that the gold layer with high phosphorus nickel surface is a compact gold layer with fewer pores, and because the corrosion resistance of the high phosphorus nickel layer is better, it is not easy to oxidize.
(2) When the thickness of nickel layer and gold layer in ENIG fluctuates, that is, embrittlement may occur on the surface. Among them, the most obvious embrittlement is at the places where the nickel layer is thinner and the gold layer is thicker. However, in the high phosphorus ENIG film, even the places where the nickel layer is not thick enough will not suffer from embrittlement.
(3) After the circuit board welding and the thermal cycle test of accumulative stress, the high phosphorus ENIG film is not prone to brittle fracture. And after 1000 times of TC, the strength of high phosphorus solder joints was not adversely affected. The data of "push ball and extension length" measured by high phosphorus is also quite stable, but the data obtained by medium phosphorus users after 1000TC is quite scattered compared with the original ones.
(4) After microsection observation and analysis of brittle samples after PCB welding and TC, it was found that the push ball cracking positions of medium phosphorus ENIG were all concentrated near IMC, but the cracking of high phosphorus ones mostly occurred in the sphere itself, and it can also be seen that the IMCs of the two were different.
(5) For high phosphorus ENIG, the adverse effect of "phosphorus increase" on the interface caused by its gold immersion reaction and welding reaction can be reduced by about 30% compared with medium phosphorus ENIG. This discovery is not the key factor with the previously recognized "total phosphorus on the interface"; On the contrary, the difference between the phosphorus content in the main nickel layer and the "phosphorus rich" area is the key statement and can be consistent with each other.
(6) As for the aluminum wire, its strength is not affected by the different phosphorus content in the nickel layer, nor by the difference of the original ENIG or 155 ℃ bremscence for 4 hours. Moreover, the ability of high phosphorus ENIG gold wire is also very good, and the thickness of its gold layer is only one tenth of that of nickel gold plating layer. This discovery will be further studied in the future.
It can be seen from the above measured data that high phosphorus ENIG has many benefits. For the sake of good solder joint integrity and excellent effect of aluminum wire or gold wire, the nickel thickness of high phosphorus ENIG used shall reach 5.5 μ M, the phosphorus content should also be kept between 9.5-13 wt%, while the thickness of the gold layer is only 0.05 μ M is enough.
然后
聯(lián)系
電話熱線
13410863085Q Q
微信
- 郵箱