
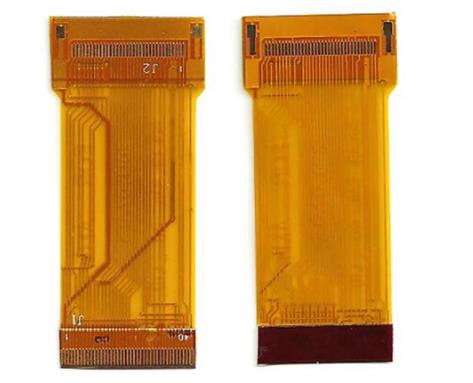
What are the problems in FPC manufacturing? How to solve it?
PCB manufacturers, PCB designers and PCBA manufacturers explain to you what problems exist in FPC manufacturing? How to solve it?
The blank part is blocked: the reasons are: ① the exposure of the back of the plate. ② Main overexposure. ③ Poor compactness with the negative film. The solution is: ① Calculate the correct post exposure time. ② Shorten the main exposure time within the range of reproduced fine lines or dots. ③ Check the vacuum degree to make sure that there is no air left between the film and the resin. The effective method is roller extrusion. Flexible circuit board.
2. The bottom cannot be washed out: the causes are: ① overexposure after exposure, ② the bottom plate is exposed under white fluorescent lamp for a long time. ③ The film is not suffICiently blackened. ④ The flushing fluid has faiLED. The solution is: ① The exposure is bright after reducing. ② Operate under the yellow safety light. ③ Remake the base plate to make the blackening concentration above 4.0. ④ Replace with new flushing fluid. Circuit board factory.
3. Straight line bending but not straight: The causes are: ① Insufficient post exposure. ② Insufficient main exposure. ③ Insufficient drying time. ④ The design (pattern) itself exceeds the tolerance of the edition. The solution is: ① Give the necessary post exposure, sometimes the ultraviolet ray of the lamp will decrease, so the post exposure test should be conducted again. ② Give the necessary main exposure, sometimes the ultraviolet ray of the lamp will be reduced, so the main exposure test shall be conducted again. ③ Extend the drying time, and allow more than 12h of natural drying as required. ④ Redesign.
4. The version is too hard: the cause is overexposure. The solution is to reduce the main exposure time or post exposure time.
5. SMAll dots or fine lines are washed away: the causes are: ① inadequate post exposure. ② Insufficient main exposure. ③ The design itself exceeds the tolerance of the edition. The solution is: ① If necessary post exposure is given, the ultraviolet ray of the lamp will sometimes decrease, so the post exposure test should be conducted again. ② Given the necessary main exposure, the ultraviolet ray of the lamp will sometimes be reduced, so the main exposure test shall be conducted again. ③ Redesign.
6. Pinhole: The causes are: ① There is much dust in the dark room. ② The negative film is not coated with light blocking paint. ③ The film does not reach the proper concentration. ④ The vacuum pad is not clean. The solutions are as follows: ① Do a good job in the cleanliness of the plate making room. ② Apply light blocking paint on the base side of the negative film. ③ Check the condition of the negative film. ④ Find a new vacuum pad.
7. Blurred image part: the causes are: ① Defects of the negative film. ② Apply a light blocking coating on the sensitive emulsion side of the negative film. ③ A negative for offset printing is used. ④ The vacuum is not enough. The solution is: ① Check whether the negative film and portrait part are clear. ② The shading coating is applied on the substrate side instead. ③ Remake the negative for relief plate. ④ Check whether the vacuum is sufficient, and also check whether there are bubbles between the negative film and the layout.
8. Orange peel on the surface of the plate: the reasons are: ① The plate is bent after the cover plate of the plate is removed. ② Insufficient vacuum. ③ Defects of the version. ④ It is corroded by flushing agent. ⑤ The panel was not cleaned with clean detergent after rinsing. The solution is as follows: ① The layout cannot be moved after removal. ② Check whether the vacuum pump works normally. ③ Check the quality with defective samples. ④ Process the plate immediately after exposure. ⑤ Carefully check whether there is fish eye during drying.
9. The layout has a sense of adhesion: the reason is that the finishing treatment is insufficient. The solution is to extend the treatment time and replace with new liquid.
10. After plate making, the layout cracks: the reasons are: ① The layout is eroded by ozone. ② The layout is exposed to sunlight or fluorescent lamp for a long time. ③ Not cleaned after printing. The solution is: ① Clear the source of ozone or keep the page away from ozone. ② Keep the layout in a place where sunlight or indoor light cannot reach, and cover it with a black cover. ③ Wash the ink.
11. The printing ink from the anilox roller is not accepted by the layout: the reason is that the processing of the layout is too much. The solution is to shorten the processing time.
12. Inadequate hardening of the bottom of the plate: the reasons are: ① the washing treatment is not sufficient, and there is still unhardened resin. ② There was no sufficient exposure to harden the bottom. The solution is: ① Check the brushing pressure and flushing time. ② Increase the post exposure time.
13. Fluctuation of fine lines on the printing press: The causes are: ① The solvent in the ink is not suitable for the layout, causing the swelling of the image part. ② Inadequate post exposure of the layout. The solution is: ① Change the ink solvent. ② Check whether the post exposure is carried out correctly.
14. The plate is detached from the clamping plate of the rinsing device: the causes are: ① The screws are loose. ② Improper splint tension. ③ Excessive brushing pressure. The solution is: ① Tighten the screws. ② Repair after inspection. ③ Move the roller. PCB manufacturers, PCB designers and PCBA manufacturers explain to you what problems exist in FPC manufacturing? How to solve it?
然后
聯(lián)系
電話熱線
13410863085Q Q
微信
- 郵箱