
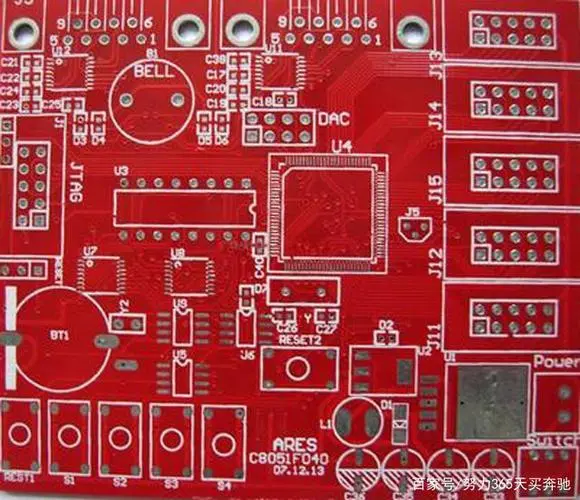
PCB quality problems usually include short circuit and open circuit, oil foaming, oil falling off, PCB substrate delamination, PCB warping, PCB pad falling off, poor tin plating and aging circuit board open circuit. The root causes of these common PCB quality problems lie in the production technology failure of PCB factories, backward production equipment, improper selection of raw materials and chaotIC management.
Reason 1: PCB production process is not good enough: the production and processing of PCB is a relatively high-tech industry, involving a series of cross disciplines such as electroplating, chEMIcal industry, machinery, etc. Each process of circuit board production and processing must be implemented in strict accordance with the production process. At the same time, each process must be equipped with corresponding testing and laboratory equipment. These process parameters and equipment can ensure the stability of circuit board quality. It is undeniable that the circuit board industry is also a polluting industry. Many practitioners, even the bosses who enter this industry, give up halfway. This has LED many SMAll circuit board manufacturers to be concerned about price. As long as they can reduce the cost, they are in terms of production technology and circuit board quality. I don't care at all. The solution concentration in electroplating process is a parameter that changes with time. Different types of circuit boards have different electroplating process currents and times. The combination of these parameters will affect the quality of the circuit board. Only strict PCB process guidance, and production according to process parameters
Circuit board
Continuous laboratory inspection can ensure that the quality of circuit boards produced is always stable. If the production is organized according to experience and quality problems occur, the agent will be added according to the feeling, which will directly lead to the continuous fluctuation of the quality of the circuit board. Customers using this circuit board will have high repair rate, low yield, and the surface looks like a circuit board. The company's procurement costs have been reduced. In fact, the maintenance cost of repair and repair is greatly increased. At the same time, the customer's brand will also be affected, which is not cost-effective in the long run.
Reason 2: The choice of raw materials is cheap and inferior: the quality of raw materials is the cornerstone of the quality of circuit boards. If the material itself is not good enough, the circuit will appear blistering, delamination, cracking, circuit board warping and uneven thickness. What is more hidden now is that some PCB manufacturers use mixed materials, some are genuine boards, some are edge materials, or materials recycled to dilute costs. The potential danger is that we don't know which batch will appear. The problem is that due to the different characteristics of circuit boards, some circuit boards do not have high requirements, so some side materials used in this situation do not show obvious problems, which makes many Circuit board manufacturers confused about this method. At the same time, because of the low price, the cost has won the favor of customers. It also encourages circuit board manufacturers to continue to take this risk. In the long run, if there is a substrate problem that causes quality problems of finished products, it will usually cause huge losses, and sometimes it is impossible to restore the company's reputation and brand. This is why more conventional circuit board manufacturers will not do so.
Reason 3: Backward production equipment: the basic way to improve the quality of circuit boards is to ensure the quality of equipment from the hardware, increase equipment investment, make equipment efficient and stable. With the progress of science and technology, the circuit equipment is becoming faster and faster, and the equipment is becoming more and more advanced. Of course, the price is getting more and more expensive. This has led to the inability of some small PCB plants to install more expensive equipment, resulting in increased dependence on employees. The current labor cost is already high. Once the dependence on skilled and skilled employees is formed, the management difficulty of PCB factory will be greatly increased. O)
然后
聯(lián)系
電話熱線
13410863085Q Q
微信
- 郵箱