
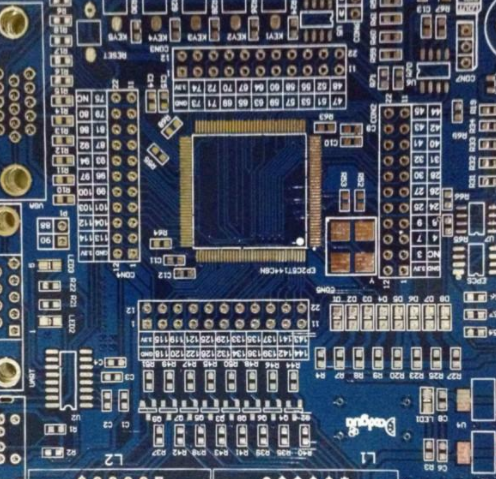
Technology and Methods of Eliminating Silver Layer on PCB
As we all know, since printed circuit boards cannot be used in heavy industry after assembly, the scrap cost is caused by mICropores Further research on this problem has proved that this problem is completely due to the solderability problem caused by circuit board design, and has nothing to do with silver precipitation process or other final surface treatment methods
1 Root cause analysis
By analyzing the root cause of defects, the defect rate can be reduced through process improvement and parameter optimization The Gianni effect usually occurs under the crack between the solder mask and the copper surface In the process of silver precipitation, because the crack is very SMAll, the silver ion supply in the silver precipitation solution is limited, but the copper here can be corroded into copper ions, and then silver precipitation reaction occurs on the copper surface outside the crack Because ion conversion is the driving force of silver precipitation reaction, the corrosion degree of copper surface under crack is directly related to the thickness of silver precipitation Cracks are formed due to any of the following reasons: excessive lateral erosion/development or poor bonding of the solver film to the coupler surface; Uneven electroplated copper layer (thin copper orifice); There are obvious deep scratches on the substrate copper under the resistance film. Corrosion occurs when sulfur or oxygen in the air reacts with metal surfaces Silver reacts with sulfur to form a $silver sulfide (Ag2. S) film on the surface There are several methods to pollute silver with sulfur, either by air (as mentioned earlier) or by other sources such as PWB wrapping paper The reaction pipeline between silver and oxygen is different. It usually forms dark brown cuprous oxide with the copper under the silver layer This defect is usually due to the rapid deposition of silver, forming a low-density silver deposition layer, which makes the copper at the bottom of the silver layer easy to contact with the air, so that the copper will react with the oxygen in the air The loose crystal structure has larger intergranular space, which requires thicker silver deposition layer to achieve oxidation resistance This means that a thicker silver layer is deposited during the production process, which increases production costs and increases opportunities for weldability problems, such as micropores and poor welding Copper exposure is usually associated with chEMIcal processes prior to silver precipitation This defect occurs after the silver deposition process, mainly because the residual film not completely removed before the process hinders the deposition of silver layer The common problem is the residual film produced in the resistance welding process. At present, it is unclear about the consequences of developers in the development process, which is calLED "residual film". This residual film blocks the silver precipitation reaction Mechanical treatment is also one of the causes of copper exposure The surface structure of the circuit board will affect the contact uniformity between the circuit board and the solution Inadequate or excessive solution recycling will also form uneven silver deposits Ionic substances on the surface of the circuit board polluted by ions may interfere with the electrical characteristics of the circuit board These ions mainly come from the silver immersion solution itself (remaining in the silver immersion layer or under the solder resist film). Different precipitated silver solutions have different ion contents The higher the ion content of the solution, the higher the ionic pollution value under the same washing conditions The porosity of silver deposits is also one of the important factors affecting ion pollution The silver layer with high porosity is easy to retain ions in solution, which increases the difficulty of cleaning, and finally leads to the corresponding increase of ion pollution value The effect of post washing will also directly affect ion pollution. Insufficient washing or unqualified water quality will lead to ion pollution exceeding the standard The pore diameter is usually less than 1mil The cavity on the metal interface compound between the solder and the welding surface is called micropore, because it is actually the "plane cavitation group" of the welding surface, which greatly reduces the stress on the welding joint There are micropores, ENIG and silver deposits on the OSP The root cause of microporosity is unknown, but several influencing factors have been identified Although all microvoids in the ag precipitate layer occur on thick silver (more than 15mm thick) surfaces When the copper surface structure at the bottom of the silver deposition layer is very rough, micropores are more likely to appear The appearance of micropores also seems to be related to the type and composition of organic matter co deposited in the silver layer In view of the above phenomenon, original equipment manufacturers, postal express, printed circuit board manufacturers and chemical suppliers have conducted several analog welding studies, none of which can completely eliminate micropores
PCB board
2. Preventive measures
In order to avoid or eliminate defects and improve the yield The prevention of Gianni effect can be traced back to the pretreatment copper plating process It is used for high aspect ratio holes and micro through-holes. Uniform plating thickness helps eliminate the hidden danger of Gianni effect Excessive corrosion or side erosion during film stripping, etching and tin stripping may lead to the formation of cracks, and there may be residual corrosion solution or other solutions in the cracks However, the problem of solder film is still the main cause of Gianni effect Most defect plates with Gianni effect have side corrosion or solder film falling off, mainly due to exposure development process Therefore, if the solder film is developed after the "front foot" and the solder film is completely solidified, the problem of Gianni effect can be almost eliminated To obtain good silver deposition, the silver deposition position must be 100% copper. The solution in each tank has good perforation capacity, and the solution can be effectively exchanged through the hole For very fine structures, such as HDI plates, it is useful to install ultrasound or syringes in pre-treatment and silver precipitation solutions For the production management of silver precipitation process, the effect of Gianni can be improved by controlling the micro erosion rate to form a smooth and semi bright surface For original equipment manufacturers (Oems), in order to eliminate the hidden danger of Gianni effect, it is necessary to avoid large copper surfaces or through holes with high aspect ratio connected with thin wires Chemical supplier, silver precipitation solution should not be highly corrosive, maintain proper pH value, silver precipitation rate is controlled, which can produce the required crystal structure, and thin silver thickness can achieve corrosion resistance Corrosion can be reduced by increasing coating density and reducing porosity Use sulfur free packaging and seal to prevent the sulfur in the air from contacting the silver surface Store the packed cardboard in an environment with a temperature of 30 ℃ and a relative humidity of 40% Although the shelf life of silver disk is very long, the storage should still follow the principle of first out By optimizing the pre precipitation process, exposed copper can be reduced or eliminated For this purpose, the copper surface can be inspected by "water cut-off" test or "bright spot" test after micro etching The clean copper surface can keep the water film for at least 40 seconds Regularly maintain the equipment to ensure the uniform and stable circulation of solution. Through DOE time optimization, the silver precipitation operating parameters, temperature and stirring were obtained to ensure the required thickness and high-quality silver layer Use ultrasonic wave or injector as required to improve the wettability of silver precipitation solution on micro through-hole, high aspect ratio hole and thick plate, and provide a feasible solution for HDI plate production These auxiliary mechanical methods can be applied to pre-treatment and silver precipitation solutions to ensure that the hole wall is completely wetted Ion pollution can be reduced by reducing the ion concentration of precipitated silver solution Therefore, the ion content of silver precipitation solution should be as low as possible without affecting the efficiency of the solution the ion content (ions and anions) must be periodically tested for compliance with industry standards To distinguish major pollutants, the results of these tests must be recorded and retained Microporosity is a defect that is difficult to prevent, because the true cause of microporosity is unknown As mentioned above, we have known that there are some factors that seem to cause or accompany microporosity, and microporosity can be controlled by eliminating or minimizing these factors The thickness of silver deposition is an important factor leading to microporosity. In summary, controlling the thickness of silver deposition is the first step Secondly, the micro corrosion rate and silver deposition rate should be adjusted to obtain smooth and uniform surface structure The organic content in the silver deposit should also be monitored by testing the purity of the silver deposit at different points in the service life of the bath solution The reasonable silver content should be controlled above 90% (atomic ratio).
3. The ideal process - AlphaSTAR
In addition to excellent performance, the "ideal process" must also meet the safety requirements. The requirements for environmental protection and reliability of the electronic industry announced on July 1, 2006. Although Les Chemical had the AlphaLEVEL product series as early as 1994, les Chemical continued to improve the process and research and development, and successfully developed the third generation of silver slot technology printed circuit board, AlphaSTAR AlphaSTAR process is specially designed to meet today's increasingly strict surface treatment requirements It solves the above-mentioned problems that lead to PCB obsolescence, new costs, environmental protection and safety, and complies with current and future regulations that may affect the printed circuit board industry The process consists of 7 steps (three of which are washing steps), its efficiency and advantages are described as follows: pretreatment is divided into the following four steps: oil removal, water washing, micro erosion and water washing The surface tension of degreasing solution is very low, which can wet all copper surfaces. This not only eliminates the problem of copper exposure, but also promotes the deposition of silver layer in high aspect ratio pores and micro through-hole The unique micro etching formula can produce slightly coarse particles and semi gloss surface structure, which helps to form a silver layer with fine and dense crystal structure, leading to high density. Even at very low silver thickness, there is a silver deposit layer with low porosity This greatly improves the corrosion resistance of the silver layer Silver precipitation is divided into the following three steps: pre leaching, silver precipitation and deionized water washing There are three purposes of pre teaching First, it is used as a sacrificial solution to prevent copper and other substances from being brought into the micro etching tank and polluting the silver precipitation solution Second, provide a clean copper surface for the silver precipitation displacement reaction. In this way, the copper surface can obtain the same chemical environment and pH value as the silver precipitation solution The third function of this process is to automatically replenish the silver tank, since the preceding has the same composition as the silver sink (except for the metallic silver) In the silver precipitation reaction, the consumption of metallic silver and the change of the content of organIC components in the silver precipitation solution are only losses caused by leaching in the tank. The components of pre leaching and silver precipitation solution are the same, and the pre leaching amount is equal to the silver precipitation amount. Therefore, the silver precipitation solution will not accumulate unnecessary organic substances The silver precipitation reaction is carried out by the substitution reaction between copper and silver ions The copper surface is slightly roughened by the AlphaSTAR micro etching solution to ensure that a uniform silver deposition layer is slowly formed at a controlled silver deposition rate The slow silver deposition rate is favorable for depositing dense crystal structure, avoiding particle growth due to precipitation and agglomeration, and forming high-density silver layer It is so dense, modelly thick (6-12U ") silver layer not only has high corrosion resistance, but also has good conductivity. silver precipitation is very stable, has a long life, and is not sensitive to light and trace halides. Other advantages of AlphaSTAR include significantly reducing downtime, low ion pollution, and low equipment cost
4. Conclusion
the AlphaSTAR process combines several finishing properties that meet and exceed The PCB industry's requirements for reliability, safety, and compliance AlphaSTAR process has a wide operation window; It is easy to operate, control and maintain, and can be reworked in the same final surface treatment production cost AlphaSTAR process solves the above six problems related to silver precipitation process, eliminating or reducing its direct impact on high-quality PCB products In addition, the process complies with RoHS and WEEE regulations, and the silver layer is completely lead-free
然后
聯(lián)系
電話熱線
13410863085Q Q
微信
- 郵箱