
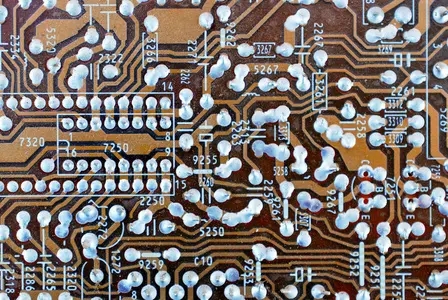
1. Method of circuit board plug-in, tin DIPping and pin cutting
1. Plate making (usually made by a special plate making enterprise, and the drawings are provided by ourselves) and cleaned.
2. Insert SMAll parts horizontally and directly, such as 1/4W resistance, capacitance, inductance and other small components close to the circuit board.
3. Insert large and medium-sized components, such as 470 μ ElectrolytIC capacitors and fire cows.
4. Insert IC, such as patch IC, which can be welded in the first step. In principle, the components shall be arranged from low to high and from small to large. The principle of high and low shall prevail over the principle of horizontal dimension.
In case of manual welding, insert and weld one plug-in. If it passes the furnace, it can be operated directly according to the operation guide of the tin furnace. The cutting feet can be either manually cut or processed by a special cutting machine. The basic process requirement is to just cut off the exposed tin ladle.
If you want to open a factory for large-scale production, you'd better read and master the relevant national and industrial standards first, otherwise your hard work will be ignored. Moreover, mastering the standard process can also help you to formulate and sort the circuit board production process.
Finally, I strongly suggest that you find an electronic factory to steal teachers. After all, seeing is believing.
2. Working principle of immersion welding furnace
The filler metal in the filler metal pot is heated and melted by the immersion welding furnace to reach the specified temperature; Workpieces to be welded or parts to be welded of workpieces to be welded are cleaned and dipped with flux; The workpiece to be welded or the part to be welded of the workpiece to be welded is immersed in the solder pot of the immersion welding furnace, and the part to be welded is heated above the solder melting point; Due to the effect of affinity, the filler metal is attached to the part of the workpiece to be welded; The workpiece is taken out for cooling and the immersion welding is completed. The temperature of different kinds of immersion welding varies greatly, and the blacksmith himself is not expert. The tin temperature is about 350 ℃ when using 30 tin to dip weld the water tank. The thermocouple is equipped with a digital temperature controller to control the heating tube.
3. Operation guidance for dip welding, leg cutting and wave soldering
1、 Production tools and raw materials
Soldering furnace, exhaust fan, air compressor, clip, scraper, circuit board with components plugged in, flux, tin bar, thinner, foot cutting machine, diagonal pliers, wave soldering machine.
2、 Preparations
1. Turn on the power switch of the soldering furnace and wave soldering machine as required, set the temperature at 255-265 ℃ (high in winter and low in summer), and add appropriate tin bars.
2. Mix the flux and thinner according to the proportion requirements of the process card, and start the foaming machine.
3. Adjust the height and width of the foot cutting machine to the corresponding position. The width and flatness of the conveyor belt are consistent with the circuit board. The height of the foot cutting machine is 1-1.2mm. Set the conveyor belt of the foot cutting machine and the power switch of the cutter to the ON position.
4. Adjust the speed of the upper and lower assembly lines, and turn on the exhaust equipment.
5. Check the batch number of materials to be processed and relevant technical requirements, and report to the team leader for handling in advance if problems are found.
6. Melt tin, preheat, clean and transfer the whole machine according to the wave soldering operation procedures, and adjust the speed to the corresponding width of the circuit board until the start light is on.
3、 Operating Steps
1. Use the right hand to clamp the circuit board, and visually inspect whether each element meets the requirements, and use the left hand to correct those that do not meet the requirements.
2. Clamp the circuit board with the inserted part, spray a little flux on the copper mooring surface, scrape the oxide layer on the tin surface of the tin furnace with a scraper, immerse the copper mooring surface of the circuit board sprayed with flux into the tin furnace, and immerse the circuit board into the tin furnace for about 0.5mm for 2-3 seconds.
3. After the tin is dipped, the hand shall be gently lifted up obliquely, and kept stable without shaking, so as to prevent faulty soldering and fullness.
4. After 5 seconds, when it is basically solidified, it is put into the assembly line and flows into the next process.
5. The foot cutting machine starts the foot cutting operation, and observe whether the circuit board is warped or deformed.
6. The cutting leg height is 1-1.2mm, and it will flow into the automatic wave crest welding machine after being qualified
7. Turn off the power when the operating equipment is used.
4、 Process requirements
1. The flux shall be sprayed evenly on the PCB pad.
2. When tinning, the copper surface of the circuit board should just contact the tin surface for 0.5mm, and no tin dust should adhere to the circuit board.
3. It is not allowed to cause blistering of copper and platinum due to too long time and too high temperature. The temperature of tin furnace is 255-265 ℃ (higher in winter and lower in summer), and the tin coating time is 2-3 seconds.
4. The solder joints must be smooth and bright, and all pads of the circuit board must be tinned.
5. Ensure the worktable is clean and record the equipment regularly.
5、 Precautions
1. The lines with poor welding must be re welded, and the secondary re welding must be carried out after cooling.
2. During operation, do not touch the tin furnace, and do not let water or oil stains fall into the tin furnace to prevent scalding.
3. Flux and thinner are flammable materials. They should be stored and used away from fire sources. The foam pipe should be immersed in the flux and not exposed to the air.
4. If it is not used for a long time, the flux shall be recycLED and sealed. The foam pipe shall be immersed in a closed container containing flux.
5. Ventilation shall be ensured during welding to prevent air pollution. Operators shall wear work clothes and masks.
6. The liquid storage box for chain claw cleaning should be added and replaced regularly. The liquid level is 1/2 - 2/3 of the slot height. Pay attention to adjusting the clearance between the brush and the chain claw.
7. When changing tin, pay attention to the safety of operators to avoid scalding.
8. Frequently check the wires at the heating point to avoid aging and leakage.
9. Pay attention to check the tin level, which should be no less than 20mm from the top of the cylinder block
4. Flux is used for dip welding of electronic component circuit boards. What is called flux foaming and what is its role? How to foam?
It can remove the oxide on the soldering tin, so that the soldering tin is firmer and has better luster.
5. Welding process requirements for manual tin furnace
Key points of soldering technology
As an operation technology, manual soldering can be mastered mainly through practical training. However, following the basic principles, learning from the experience accumulated by predecessors, and using the correct methods, you can master the operation technology with half the effort. The following points are essential for learning welding technology.
1、 Basic conditions for soldering
1. Weldability of weldment
Not all materials can be connected by soldering. Only some metals have good solderability (strictly speaking, they can be soldered) can be connected by soldering. Generally, copper and its alloys, gold, silver, zinc, nickel, etc. have good weldability, while aluminum, stainless steel, cast iron, etc. have poor weldability, which generally requires special flux and methods to solder.
2. Qualified solder
The solder quality will be affected if the composition of lead tin solder is substandard or the impurities exceed the standard. Especially, the content of some impurities, such as zinc, aluminum, CADmium, etc., even 0.001% of the content will significantly affect the wettability and fluidity of the solder, reducing the welding quality. It is obvious that no good cook can produce delicious food with inferior raw materials.
3. Suitable flux
Different fluxes shall be used for welding different materials. Even for the same material, different fluxes are often used when different welding processes are used, such as manual soldering iron welding and immersion welding. Different fluxes are required for post welding cleaning and no cleaning. For manual soldering, the use of rosin and active rosin can meet the assembly requirements of most electronic products. It should also be noted that too much or too little flux is not conducive to soldering.
4. The solder joint design is reasonable
Reasonable solder joint geometry is crucial to ensure the quality of soldering. Due to the limited strength of lead and tin materials, it is difficult to ensure sufficient strength of solder joints for the joints shown in Figure 1 (a), while the joint design in Figure 1 (b) has been greatly improved. Figure 2 shows the influence on welding quality when the size of lead and hole of through-hole mounting element on printed board is different.
2、 Key points of manual soldering
The following points are derived from the soldering mechanism and proved to be universally applicable by practical experience.
1. Grasp the heating time
Different heating speeds can be used for soldering, for example, the shape of the soldering iron is not good, and we have to extend the time to meet the requirements of the solder temperature when using a small soldering iron to solder large weldments. In most cases, prolonged heating time is harmful to electronic product assembly, because
(1) The bonding layer of the solder joint exceeds the proper thickness due to long-time heating, which causes the performance deterioration of the solder joint.
(2) printed boards, plastics and other materials will deform and deteriorate when heated too much.
(3) The performance of components changes or even fails after being heated.
(4) The surface of the solder joint is oxidized due to the volatilization of the flux and loss of protection.
Conclusion: The shorter the time is, the better on the prEMIse that the solder wets the weldment.
2. Keep proper temperature If high temperature soldering iron is used to weld and calibrate solder joints in order to shorten the heating time, it will bring another problem: the flux in the solder wire does not have enough time
Overflow on the welded surface and premature volatilization failure; Too fast melting speed of solder affects the function of flux; Because the temperature is too high, although the heating time is short, it also causes overheating.
Conclusion: Keep the tip in a reasonable temperature range. The general experience is that the temperature of the soldering head is 50 ℃ higher than the melting temperature of the solder.
The ideal state is to shorten the heating time at a lower temperature. Although this is contradictory, we can obtain a satisfactory solution in practical operation.
3. It is harmful to apply force on the solder joint with the soldering iron head
The soldering iron head transfers heat to the solder joint mainly by increasing the contact area. It is useless to apply force to the solder joint with the soldering iron for heating. In many cases, it will cause damage to the weldment. For example, the welding points of potentiometers, switches and connectors are often fixed on the plastIC components, and the force application results in the failure of the original components.
3、 Key points of soldering operation
1. Surface treatment of weldment
The weldments encountered in manual soldering iron welding are all kinds of electronIC parts and wires. Unless electronic components within the "insurance period" are used under mass production conditions, generally the weldments encountered need to be surface cleaned to remove rust, oil, dust and other impurities affecting the welding quality. In manual operation, mechanical scraping, alcohol and acetone scrubbing are commonly used.
2. Pre welding
Pre soldering refers to wetting the component leads or conductive welding parts to be soldered with soldering tin in advance, which is generally called tin plating, tin coating, tin lining, etc. It is accurate to call pre welding, because its process and mechanism are all the whole process of tin welding - the solder wets the surface of the weldment, and after the bonding layer is formed by the diffusion of metal, the surface of the weldment is "plated" with a layer of solder. Pre soldering is not an indispensable operation for soldering, but it is almost indispensable for manual soldering, especially for maintenance, debugging and development.
3. Do not use excessive flux
An appropriate amount of flux is indispensable, but do not think that the more the better. Excessive rosin not only causes the workload to be cleaned around the welding point after welding, but also prolongs the heating time (rosin melts, volatilizes and takes away heat), reducing work efficiency; When the heating time is insufficient, it is easy to be mixed into the solder to form "slag inclusion" defect; For the welding of switch elements, excessive flux is easy to flow to the contacts, resulting in poor contact.
The appropriate amount of flux should be loose perfume, which can only wet the solder joints to be formed. Do not let loose perfume flow into the component surface or socket hole (such as IC socket) through the printed board. For the welding wire with rosin core, no flux is needed.
4. Keep the soldering head clean
Because the iron head is in a high temperature state for a long time during welding, and it is also in contact with flux and other substances that are decomposed by heat, its surface is easy to be oxidized to form a layer of black impurities, which almost form a thermal insulation layer, making the iron head lose its heating effect. Therefore, the impurities shall be wiped off on the soldering iron frame at any time. It is also a common method to wipe the soldering iron head with a wet cloth or sponge at any time.
5. Heating shall be conducted by soldering bridge
In the non assembly line operation, the shape of the solder joint welded at one time is various, and we cannot constantly change the soldering head. To improve the heating efficiency of the soldering iron head, it is necessary to form a solder bridge for heat transfer. The so-called solder bridge is a bridge that uses a small amount of solder left on the soldering iron as the heat transfer between the soldering iron head and the weldment during heating. It is obvious that the thermal conductivity of liquid metal is much higher than that of air, so that the weldment is quickly heated to the welding temperature, as shown in Figure 4. It should be noted that the amount of tin retained as a solder bridge should not be excessive.
6. The amount of soldering tin shall be appropriate
Excessive soldering tin not only unnecessarily consumes more expensive tin, but also increases the welding time and correspondingly reduces the working speed. What is more serious is that in high-density circuits, excessive tin can easily cause undetectable short circuits.
However, too little solder can not form a firm bond, reducing the strength of solder joints. Especially when soldering wires on the board, insufficient solder often causes the wires to fall off.
7. The weldment shall be firm
Do not move or vibrate the weldment before the solder solidifies. In particular, when using tweezers to clamp the weldment, the tweezers must be removed after the solder solidifies. This is because the solidification process of solder is a crystallization process. According to the crystallization theory, the external force (moving of the weldment) during crystallization will change the crystallization conditions, resulting in coarse crystals, resulting in the so-called "cold welding". The appearance phenomenon is that the surface is dull and looks like bean dregs; The internal structure of the solder joint is loose, easy to have air gaps and cracks, resulting in reduced strength of the solder joint and poor conductivity. Therefore, the weldment must be kept still before the solder solidifies. In actual operation, various appropriate methods can be used to fix the weldment, or reliable clamping measures can be used.
8. The soldering iron should be evacuated carefully
The soldering iron shall be handled in time, and the angle and direction of evacuation have a certain relationship with the formation of solder joints.
When removing the soldering iron, rotate it slightly to keep proper solder at the solder joint, which needs to be realized in actual operation.
6. What flux should be selected for the hand dipping tin furnace? There is SMD on the PCB, which will not harm the SDM?
It is not the flux that harms SMD, but the temperature of the tin furnace and the length of immersion welding time during immersion welding... Of course, if the effect of tin coating on the flux is good, the immersion welding time is relatively short. Of course, the thermal shock damage to SMD components is small. Sometimes the red glue used has poor heat resistance, which will cause SMD components to fall into the tin furnace during immersion welding. These are also not directly related to the flux, But there is a certain causal relationship... The premise is to find a kind of flux with strong soldering effect and fast soldering but good safety performance, which can help you shorten the welding time as much as possible, so that you will not harm the SMD components as much as possible
The activity of the flux is stronger, and naturally its residue is more corrosive. Products with high requirements for electrical insulation should also be considered clearly when selecting the flux... Don't care about one thing and lose another
然后
聯(lián)系
電話熱線
13410863085Q Q
微信
- 郵箱