
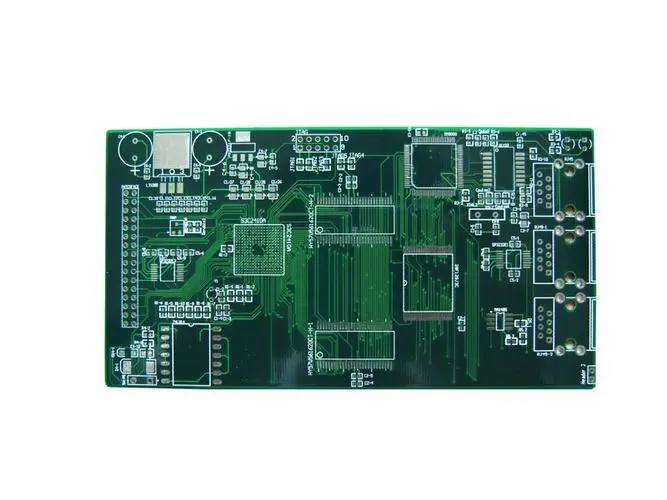
Eight super details that cannot be ignored in SMT processing
As an electronIC processing supplier, we must thoroughly understand all the processing processes in the factory, especially the SMT processing process as the main force.
In each workshop, there will be SMT processing lines. On this assembly line, we can divide it into the following parts.
1. Printing of lead-free solder paste
In the previous article, I mentioned the printing of lead-free solder paste. In this part, the machine we use is SMT sEMI-automatic printing machine. In this part of operation, we should notice that the steel mesh is aligned with PCB, and the opening of the steel mesh must be completely coincident with the PCB pad. Normal production can only be started after 3 pieces of test print are confirmed to be OK. Self inspection shall be carried out for each printed PCB, and the printing solder paste shall be free from defects such as excessive tin, insufficient tin, connected tin, and offset. The printing defects shall be carefully cleaned. Wipe the steel mesh in time. Add solder paste in time to ensure the amount of solder paste rolling on the wire mesh.
2. Mounting of SMAll materials
The machine we use in this process is the CP machine. It can quickly mount materials. Before starting the machine, it is necessary to make sufficient preparations, such as the placement of materials and the positioning setting of the machine. When the yellow light of the machine is on, it is necessary to prepare to fill it with materials.
3. Installation of large materials
This process is to help PCB add large materials that cannot be mounted on CP machine before, such as crystal oscillator. In this link, we use the XP machine. It can realize automatic mounting of large materials. Note that the process is SIMilar to the CP machine.
4. Furnace front QC
This link is an essential part of the whole SMT process. This link can ensure that all semi-finished products are completely free before passing through the furnace, so it is calLED furnace front QC. In this position, a QC is usually used to check PCB boards that flow out of the mounter. Check the layout for material leakage, deviation and other problems. Then, manually correct the plates with material leakage or deviation.
5. Reflow soldering
The function of reflow soldering is to melt the solder paste of the layout, so that the materials can be tightly welded to the layout. The machine needed for this process is wave soldering. There are also several points for attention in wave soldering. The first is the adjustment of temperature in the furnace, which requires comprehensive consideration of various aspects such as the heating degree of PCB board and the heat resistance of materials, and then set the optimal temperature for wave soldering, so that no other problems will occur after PCB board passes the furnace.
6. QC after furnace
Quality is life. After passing the furnace, certain problems will occur, such as empty welding, faulty welding, continuous welding, etc. So how to find these problems? We must also attach a QC to this link to detect the plate surface problems after the furnace. Then conduct manual correction.
7. QA spot check
After all the automatic mounting processes are completed, we still have one last step, that is, spot check. The spot check step can roughly evaluate the production qualification rate, that is, the quality of our products. Of course, every step must be carefully done during the spot check, and every detail on the page must not be missed, so as to ensure the quality of the company's products.
8. Warehousing
Final warehousing. Attention should also be paid to the warehousing, and the packaging should be neat, not sloppy. Only in this way can we give customers a perfect experience.
然后
聯(lián)系
電話熱線
13410863085Q Q
微信
- 郵箱