
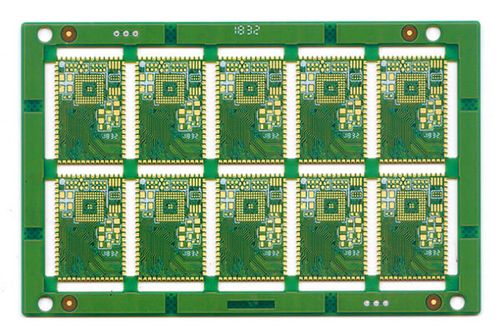
PCB manufacturer: How to check and prevent PCB short circuit?
PCB maintenance
One of the most common problems encountered in the maintenance of electronIC products of circuit board manufacturers is short circuit. Short circuit causes considerable harm to PCBA boards, ranging from burning components to scrapping PCBA. We have to avoid short circuit as much as possible. We must grasp every step of production and check every suSPIcious point. How to check and prevent PCB short circuit?
1. If it is manual welding, form a good habit.
First, before welding, visually check the PCB board, and use a multimeter to check whether the key circuits (especially the power supply and ground) are short circuited;
Secondly, after welding a chip, use a multimeter to test whether the power supply and ground are short circuited;
In addition, do not throw the soldering iron randomly during welding. If you throw the soldering tin onto the solder leg of the chip (especially the surface mount components), it will not be easy to find.
2. Open the PCB diagram on the computer, light up the short circuited network, and see where it is closest to and is most easily connected to one. Pay special attention to the internal short circuit of IC.
3. Short circuit is found. Take a board to cut lines (especially for single/double layer boards). After cutting lines, power on each function block separately, and eliminate one part by one.
4. Use short circuit positioning analyzer, such as PROTEQ CB2000 short circuit tracker in Singapore, QT50 short circuit tracker in Hong Kong SMArt Technology, POLAR ToneOhm950 Multilayer board circuit short circuit detector in the United Kingdom, etc.
5. Be careful when welding small surface mount capacitors, especially power filter capacitors (103 or 104), which are large in number, are easy to cause short circuit between power supply and ground. Of course, sometimes the capacitor is short circuited due to bad luck, so the best way is to check the capacitor before welding.
6. If there is a BGA chip, because all the solder joints are covered by the chip and cannot be seen, and it is also a multilayer board (more than 4 layers), it is better to separate the power supply of each chip during the design, and connect it with a magnetic bead or a 0 ohm resistance. In this way, when the power supply is short circuited to the ground, disconnect the magnetic bead for detection, and it is easy to locate a chip. Because BGA is difficult to weld, if it is not automatically welded by the machine, it will short circuit the adjacent power supply and the two welding balls.
然后
聯(lián)系
電話熱線
13410863085Q Q
微信
- 郵箱