
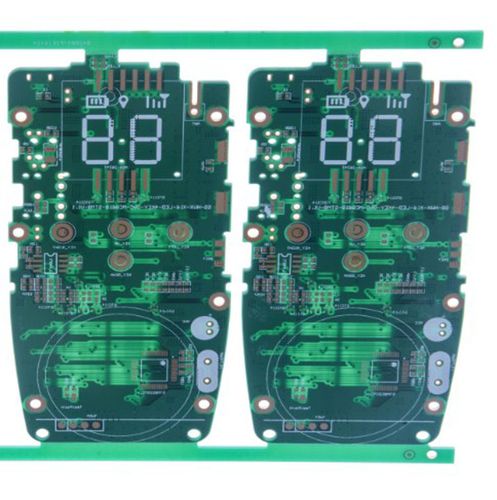
Summary of production experience of halogen-free PCB
Halogen free PCB
1. Lamination
Laminating parameters may vary from company to company. Take the above mentioned BenefICial Substrate and PP as the multilayer board. In order to ensure the full flow of resin and good adhesion, it requires a low temperature rise rate (1.0-1.5 ℃/min) of the board material and multi section pressure matching. In addition, it requires a long time in the high temperature stage, which lasts more than 50 minutes at 180 ℃. The following is a recommended set of platen program settings and actual sheet temperature rise. The bonding force between the copper foil and the substrate of the pressed plate is 1. ON / mm according to the test results. After six times of thermal shock, the electrically charged plate does not show delamination and bubbles.
2. Drilling machinability
Drilling condition is an important parameter, which directly affects the quality of hole wall in PCB processing. The adoption of P and N series functional groups in halogen-free copper clad laminates increases the molecular weight and enhances the rigidity of molecular bonds, which also enhances the rigidity of materials. At the same time, the Tg point of halogen-free materials is generally higher than that of ordinary copper clad laminates, so the drilling parameters of ordinary FR-4 are used for drilling, and the results are generally not ideal. When drilling halogen-free plates, it is necessary to make some adjustments under normal drilling conditions.
For example, if the company uses Shengyi S1155 / S0455 core plate and PP four layer plate, its drilling parameters are not the same as those of normal drilling. When drilling halogen-free plates, the rotating speed should be 5-10% faster than the normal parameters, while the feed and withdraw speed should be 10-15% lower than the normal parameters, so that the roughness of the drilLED holes is SMAll.
3. Alkali resistance
In general, the alkali resistance of halogen-free plates is worse than that of common FR-4. Therefore, in the etching process and the rework process after resistance welding, special attention should be paid to that the immersion time in alkaline film remover should not be too long to prevent the occurrence of white spots on the substrate. In the actual production, our company has suffered a lot: the halogen-free plates that have been soldered and cured need to be backwashed due to some problems, but the common FR-4 backwashing method is still used for the backwashing, and they were immersed in 75 ℃ and 10% NaoH for 40 minutes. As a result, all the white spots of the base materials washed out were reduced to 15-20 minutes. This problem no longer exists. Therefore, it is better to make the first plate when reworking the halogen free plate for resistance welding, so as to obtain the best parameters, and then rework in batches.
4. Halogen free resistance welding
At present, there are many kinds of halogen-free solder resist inks available in the world, and their performance is SIMilar to that of ordinary liquid photosensitive inks.
5. Summary
Halogen free PCB boards can meet the quality requirements of PCB boards in other properties due to their low water absorption and environmental requirements. Therefore, the demand for halogen-free PCB boards is growing; In addition, major plate suppliers have also invested more funds in the research and development of halogen-free substrate and halogen-free PP. It is believed that low price halogen-free plate structures will be put into the MARKet soon. Therefore, PCB manufacturers should put the trial and use of halogen-free boards on the agenda, formulate detailed plans, gradually expand the share of halogen-free boards in the factory, and make themselves ahead of the market demand.
然后
聯(lián)系
電話(huà)熱線(xiàn)
13410863085Q Q
微信
- 郵箱