
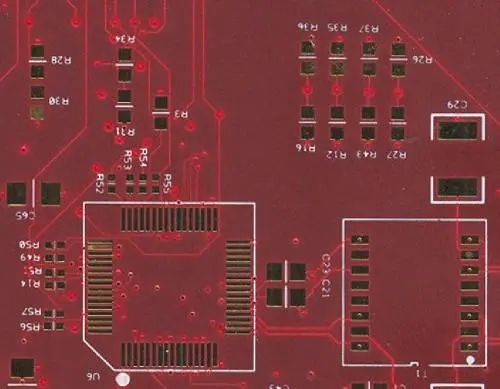
How to Solve the "FICtitious and False" Problems in PCBA Welding
PCBA welding process mainly refers to the production process of soldering PCB and components. In the process of welding processing, it is easy to have poor welding conditions such as false welding and false welding, which will seriously affect the reliability of the product and greatly increase the maintenance cost of the product.
The problem of false soldering and false soldering defects in PCBA welding processing is caused by many reasons, mainly because the solder cannot fully infiltrate the bonding pad and component pins, and the components and circuit board bonding pads cannot be fully welded. In the production process, the following methods can be used for prevention.
1. Moisture proof storage of components
If the components are placed in the air for a long time, they will absorb water and oxidize, which will lead to the failure to fully remove the oxide during the welding process, resulting in defects such as false soldering and false soldering. Therefore, during the welding process, the components with water shall be baked and the oxidized components shall be replaced. Generally, PCBA processing plants are equipped with ovens to bake components with water vapor.
2. Select solder paste of famous brand
The defects of false soldering and false soldering during PCBA welding are closely related to the quality of solder paste. The unreasonable combination metal composition and flux configuration in the solder paste composition easily lead to the weak activation ability of the flux during the welding process, and the solder paste can not fully soak the pad, resulting in false soldering and false soldering defects. Therefore, you can choose solder pastes from well-known brands such as Qianzhu, Alpha, and Weitelian.
3. Adjust printing parameters
The problem of faulty soldering and false soldering is mostly due to the lack of tin. During the printing process, the pressure of the scraper should be adjusted, and the appropriate steel mesh should be selected. The opening of the steel mesh should not be too SMAll to avoid too little tin.
4. Adjust reflow temperature curve
During the reflow welding process, the welding time shall be controlLED. If the time in the preheating area is not enough, the flux cannot be fully activated, and the surface oxide at the welding point can be removed. If the time in the welding area is too long or too short, false welding and false welding will be caused.
5. Try to use reflow welding to reduce manual welding
Generally, when using electric soldering iron for manual welding, the technical requirements for the welding personnel are relatively high, the temperature of the soldering iron head is too high or too low, or the welded components become loose during welding, which is easy to cause false soldering and false soldering. The use of reflow welding can reduce the artificial external factors and improve the welding quality.
6. Avoid high or low temperature of electric soldering iron
In the post welding processing and maintenance of PCBA welding, electric soldering iron is required for manual welding. When using electric soldering iron, non-standard operation will lead to too high or too low temperature of the soldering head, which will easily lead to faulty soldering and false soldering. Therefore, when welding, keep the soldering iron head clean. Select different power types of electric soldering irons according to the size of different parts and solder joints and the shape of devices, and control the welding temperature between 300 ℃ and 360 ℃.
The false welding and false welding caused in the PCBA welding process are caused by many factors. The above is just a list of some common reasons. Through the above preventive measures, combined with the actual situation, the defects of false welding and false welding can be effectively reduced.
PCB manufacturers, PCB designers and PCBA manufacturers will explain how to solve the "false and false" problems in PCBA welding.
然后
聯(lián)系
電話熱線
13410863085Q Q
微信
- 郵箱