
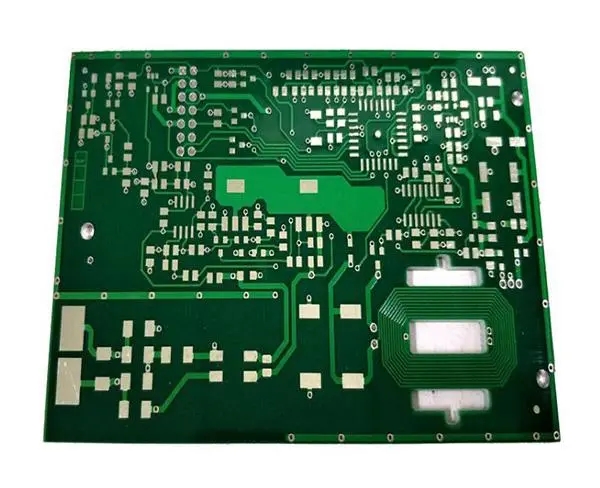
PCB nICkel plating solution problem and why PCB has several different colors
On PCB, nickel is used as the substrate coating of precious and base metals. The deposition layer of low stress nickel on PCB is usually prepared by using modified Watt nickel plating solution and some sulfamic nickel plating solutions with stress reducing additives. What problems do you usually encounter when using PCB nickel plating solution?
1、 Temperature - different nickel processes use different bath temperatures. In the high temperature nickel plating bath, the nickel coating obtained has low internal stress and good ductility. Generally, the operating temperature is maintained at 55~60 ℃. If the temperature is too high, nickel salt hydrolysis will occur, resulting in pinholes in the coating and reducing cathodic polarization.
2、 PH value -- The PH value of nickel plating electrolyte has a great influence on the coating performance and electrolyte performance. Generally, the PH value of PCB nickel plating electrolyte is maintained between 3 and 4. The nickel plating solution with higher PH value has higher dispersion force and higher cathode current efficiency. However, the PH is too high. As the cathode continuously releases hydrogen during electroplating, when it is greater than 6, the coating will have pinholes. The nickel plating solution with lower PH has better anodic dissolution, which can increase the nickel salt content in the electrolyte. However, if PH is too low, the temperature range of bright coating will be narrowed. When nickel carbonate or basic nickel carbonate is added, the PH value increases; Add aminosulfonic acid or sulfuric acid to reduce the PH value, and check and adjust the PH value every four hours during operation.
3、 Anode - Soluble anode is used for conventional nickel plating on PCB, and it is quite common to use titanium basket as the anode inner nickel angle. The titanium basket shall be put into the anode bag woven of polypropylene material to prevent the anode mud from falling into the plating solution, and the holes shall be cleaned regularly and checked for smoothness.
4、 Purification - When there is organic pollution in the bath, it should be treated with activated carbon. However, this method usually removes part of the stress remover (additive), which must be supplemented.
5、 Analysis - The bath should use the key points of the process procedure specified by the process control to regularly analyze the bath composition and Hull cell test, and guide the production department to adjust the bath parameters according to the obtained parameters.
6、 Stirring - Like other electroplating processes, the purpose of stirring is to accelerate the mass transfer process, reduce the concentration change and increase the upper limit of allowable current density. Another very important role of stirring the plating solution is to reduce or prevent pinholes in the nickel plating layer. Compressed air, cathode movement and forced circulation (combined with carbon core and cotton core filtration) are commonly used for mixing.
7、 Cathode current density Cathode current density has an effect on cathode current efficiency, deposition rate and coating quality. In the low current density region, the cathodic current efficiency increases with the increase of current density when nickel is plated with electrolyte with lower PH; In the area of high current density, the cathodic current efficiency is independent of current density, while when nickel electroplating solution with high PH is used, the cathodic current efficiency has little relationship with current density. As with other plating types, the cathode current density range selected for nickel plating shall also depend on the composition, temperature and stirring conditions of the plating solution.
Why do circuit boards have different colors?
Why do circuit boards have different colors? At present, the common PCB colors in the MARKet are green, black, blue, yellow, purple, red and brown; Recently, white, pink and other different color PCBs have also appeared. So why are there several different colors for PCB?
In PCB production, whether the copper layer is manufactured by addition or subtraction method, it will finally get a smooth and unprotected surface. Although the chEMIcal properties of copper are not as active as aluminum, iron, magnesium, etc., pure copper is easily oxidized in contact with oxygen in the presence of water. Because the thickness of copper layer in PCB is very thin, the oxidized copper will become a bad conductor of electricity, which will greatly damage the electrical performance of the entire PCB.
In order to prevent copper oxidation, separate the welding part and non welding part of PCB during welding, and protect the surface layer of PCB circuit board, design engineers paint a special coating on the surface of PCB to form a protective layer with a certain thickness and block the contact between copper and air. This coating is calLED solder mask, and the material used is solder mask.
For the convenience of maintenance and manufacturing, PCB often needs to print SMAll words on the board. Therefore, engineers added various colors to the solder resist paint, and finally formed a black or red or blue PCB.
From this point of view, the color of PCB board has nothing to do with the quality of PCB. The difference between black PCB and blue PCB, yellow PCB and other color PCBs is that the color of solder resist paint painted on the last is different. If the PCB design and manufacturing process are exactly the same, the color will not have any impact on the performance or heat dissipation. In recent years, people have used more solder resist paints such as dark green, dark brown and dark blue for PCB to facilitate manufacturing and maintenance.
PCB manufacturers, PCB designers and PCBA manufacturers explain the problems of PCB nickel plating solution and why PCB has different colors.
然后
聯(lián)系
電話熱線
13410863085Q Q
微信
- 郵箱