
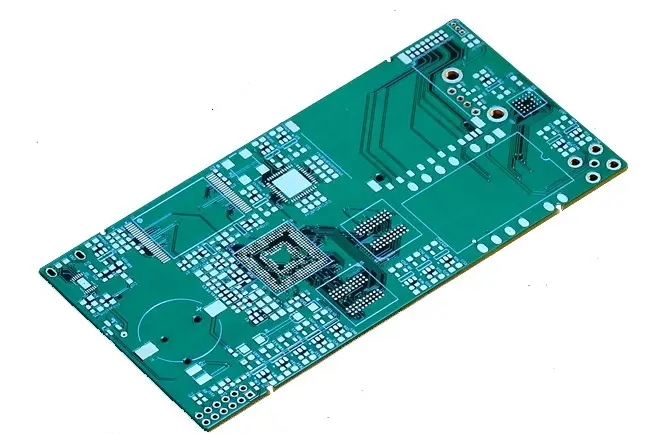
Advantages of PCB panel proofing and what conditions must be met for welding
In many customer consultations, there are many questions about PCB panel proofing. Of course, many new customers do not know much about PCBA panel proofing. What are the advantages of PCB panel proofing?
In order to improve the qualifICation rate of electronic products, it is necessary to have a predictable guarantee for the quality of its core component - PCB. Therefore, a SMAll amount of production needs to be carried out first through PCB proofing to test the performance of products, which can not only improve production efficiency, but also reduce production costs.
2. Panel proofing is an effective measure to reduce production costs. PCB assembly will have fewer processes for the whole PCBA processing process. Whether the whole assembly is 20 pieces or 10 pieces, it maximizes the use of production resources and improves production efficiency.
3. PCBA panel proofing is of great benefit to the manufacturer's front-end engineering. They can better participate in the production of customers' products, and better understand the production and process difficulties of customers' products; It is of great benefit to the subsequent product production quality control. Such early participation will help to control production risks and improve customer satisfaction.
4. It can minimize the quality problems that may be encountered in mass production. After all, it is very important for a manufacturer to ensure a good reputation.
What conditions must PCB welding meet?
Welding is the most important process in PCB processing, which plays a decisive role in PCB quality. What conditions must PCB welding meet?
1. The weldment has good weldability
Solderability refers to the performance of the alloy that can form a good combination between the metal material to be welded and the solder at an appropriate temperature. In order to improve the solderability, measures such as surface tin plating and silver plating can be taken to prevent the oxidation of the material surface.
2. The surface of weldment must be kept clean
Even weldments with good weldability may produce oxide film and oil stain harmful to wetting on the surface of weldments due to storage or contamination. The dirty film must be removed before welding, otherwise the welding quality cannot be guaranteed.
3. Use a suitable flux
The function of the flux is to remove the oxide film on the surface of the weldment. Different fluxes should be selected for different welding processes. When welding precision electronic products such as printed circuit boards, rosin based flux is usually used to ensure reliable and stable welding.
4. The weldment shall be heated to proper temperature
During welding, the role of thermal energy is to melt solder and heat the welding object, so that tin and lead can get enough energy to penetrate into the lattice of the metal surface to form alloy. If the welding temperature is too low, it is easy to form false welding; If the welding temperature is too high, the solder will be in the non eutectic state, and the solder quality will decline.
5. Suitable welding time
Welding time refers to the time required for physical and chEMIcal changes in the whole welding process. It includes the time when the metal to be welded reaches the welding temperature, the melting time of solder, the time when the flux plays its role and the time when the metal alloy is generated. When the welding temperature is determined, the appropriate welding time shall be determined according to the shape, nature and characteristics of the weldment.
PCB manufacturing, PCB design and PCBA processing manufacturers explain the advantages of PCB panel proofing and what conditions must be met for welding.
然后
聯(lián)系
電話熱線
13410863085Q Q
微信
- 郵箱