
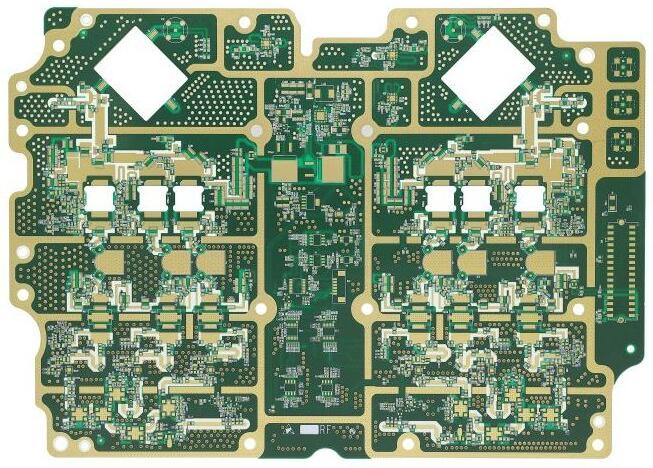
7 Inspection method for PCB produced by PCB proofing manufacturer
Explain the electronIC hardware design process, including hardware requirement scheme, scheme design, PCB design, PCB proofreading, PCB manufacturing, UT and integration testing, etc In the process of PCB manufacturing, in order to ensure the product quality of PCB, manufacturers usually use various detection methods to detect defects in different PCB production processes
PCB processing and manufacturing
7 Common inspection methods Printed circuit board
1. Manually and visually inspect the printed circuit board
The most traditional testing method is to use a magnifying glass or a calibration microscope, and use the operator's visual inspection to determine whether the printed circuit board is qualified and when the correction operation is required However, due to the production of printed circuit boards and the reduction of wire spacing and component volume, this method is increasingly impractical
Advantages: low budget cost, no test fixture
Disadvantages: subjective human error, high long-term cost, discontinuous defect detection, difficult data collection, etc
2. PCB online test
Find out manufacturing defects and test analysis, digital, and pass the power performance test of mixed signal components to ensure that they meet the specification requirements There are several test methods, such as needle bed tester and flying needle tester
Advantages: low test cost for each board, powerful digital and functional test capability, fast and thorough short circuit and open circuit test, programming firmware, high defect coverage and easy programming, etc
Disadvantages: test fixture is required, programming and debugging time are required, fixture manufacturing cost is high, it is difficult to use, etc
3. PCB function test
The functional system test is to use special test equipment in the middle stage and the end of the production line to conduct a comprehensive test on the functional modules of the circuit board to confirm the quality of the circuit board. Function test is the earliest principle of automatic test It is based on a specific board or specific unit and can be completed together with various equipment There are several types of end product testing, the latest physical models, and stack testing Functional testing usually does not provide in-depth data, such as foot level and component level diagnostics for process improvement, and requires professional equipment and specially designed test programs It is very complicated to write functional test program. In retrOSPect, it is not applicable to most circuit board production lines
4. Automatic optical inspection
Also known as automatic visual inspection, which is based on optical principles and comprehensively uses image analysis, is used in computer and automatic control technologies to detect and process defects encountered in circuit board production This is a new method to identify manufacturing defects AOI is usually used before and after reflow and before power test to improve the pass rate of power processing or functional test At this time, the cost of correcting defects is far lower than the cost after the final test, often more than 10 times
5. Automatic X-ray inspection
Using the difference in the absorption rate of different substances to X-rays It is mainly used to detect defects such as bridging, missing parts, poor alignment, etc, It is caused by ultra-fine spacing and ultra-high density circuit board and assembly process It can also use its tomography technology to detect the internal defects of IC chips This is the only way to test the welding quality of ball grid array and plug welding ball at present
Advantages: It can detect the quality of BGA welding and embedded components without fixed device cost
Disadvantages: slow speed, high failure rate, difficulty in detecting reworked solder joints, high cost and long program development time
6. Laser detection system
This is the latest development of PCB testing technology Scan the printed board with a laser beam, collect all measurement data, and compare the actual measurement value with the preset acceptance limit value The technology has been verified on bare boards, and assembly board testing is being considered, and the speed is enough to meet the needs of large-scale production lines
Advantages: fast output speed, no need for fixed devices and visual uncovered channels
Disadvantages: high initial cost, many maintenance and use problems
7. Size detection
Use the two dimensional image measuring instrument to measure the hole position Since printed circuit board is a SMAll, thin and soft product, contact measurement is easy to deform and lead to inaccurate measurement Two dimensional image measuring instrument has become the best high-precision dimension measuring instrument
Different inspection methods have their advantages and disadvantages The manufacturer will select appropriate inspection methods for different situations PCB type, complexity, defects to ensure quality and other specific conditions PCB
Interesting knowLEDge
Some people say that only after going to university did they know that the green board is called In fact, not all PCBs are green. There are other colors, such as black and purple The green printed circuit board is coated with a layer of "green oil layer", also known as "soldering mask", to protect the circuit and prevent short circuit
然后
聯(lián)系
電話熱線
13410863085Q Q
微信
- 郵箱