
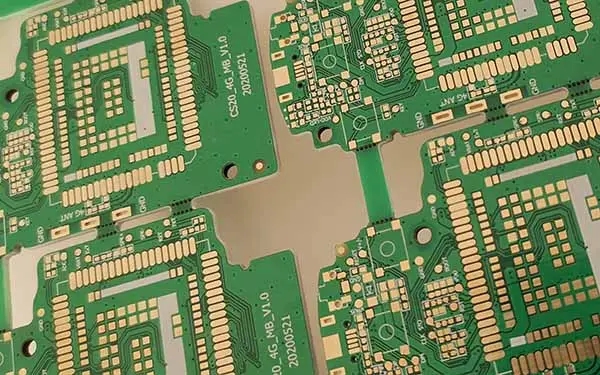
DetaiLED explanation of maintenance methods for nICkel plating solution of circuit board
The circuit board manufacturer, circuit board designer and PCBA processor explain the maintenance methods of the nickel plating solution for circuit boards
Bath maintenance
a) Temperature - different nickel processes use different bath temperatures. The influence of temperature change on nickel plating process is complex. In the high temperature nickel plating bath, the nickel coating obtained has low internal stress and good ductility. When the temperature is increased to 50 ° C, the internal stress of the coating is stable. Generally, the operating temperature is maintained at 55-60 ℃. If the temperature is too high, nickel salt hydrolysis will occur, and the generated nickel hydroxide colloid will retain colloidal hydrogen bubbles, causing pinholes in the coating and reducing cathodic polarization. Therefore, the working temperature is very strict and should be controlled within the specified range. In actual work, the room temperature controller is used to maintain the stability of its working temperature according to the optimal temperature control value provided by the supplier.
b) PH value - The practice results show that the PH value of nickel plating electrolyte has a great influence on the coating performance and electrolyte performance. In strong acid electroplating solution with PH ≤ 2, there is no nickel deposition, but light gas is precipitated. Generally, the PH value of PCB nickel plating electrolyte is maintained between 3-4. The nickel plating solution with higher PH value has higher dispersion force and higher cathode current efficiency. However, when the PH is too high, the PH value of the coating near the cathode surface will rise rapidly due to the continuous precipitation of light gas from the cathode during the electroplating process. When the PH is greater than 6, there will be light nickel oxide colloid, which will cause hydrogen bubbles to stay and make the coating appear pinholes. The inclusion of nickel hydroxide in the coating will also increase the brittleness of the coating. The nickel plating solution with low PH has good anodic dissolution, which can increase the nickel salt content in the electrolyte and allow the use of higher current density, thus strengthening production. However, if PH is too low, the temperature range of bright coating will be narrowed. When nickel carbonate or basic nickel carbonate is added, the PH value increases; Add aminosulfonic acid or sulfuric acid to reduce the PH value, and check and adjust the PH value every four hours during operation.
c) Anode - Soluble anode is used for conventional nickel plating on PCB, and it is quite common to use titanium basket as the anode inner nickel angle. The advantage is that the anode area can be large enough without change, and the anode maintenance is relatively SIMple. The titanium basket shall be put into the anode bag woven of polypropylene material to prevent the anode mud from falling into the plating solution. Regularly clean and check whether the hole is unblocked. The new anode bag shall be soaked in boiling water before use.
d) Purification - When there is organic pollution in the bath, it should be treated with activated carbon. However, this method usually removes part of the stress remover (additive), which must be supplemented. The treatment process is as follows:;
(1) Take out the anode, add 5ml/l of impurity removal water, heat (60-80 ° C) and blow air (air stirring) for 2 hours.
(2) When there are many organic impurities, 30% hydrogen peroxide of 3-5 ml/lr shall be added for treatment, and the gas shall be stirred for 3 hours.
(3) Add 3-5 g/l powdered activity under continuous stirring, continue to stir with air for 2 hours, turn off the stirring and stand for 4 hours, add filter aids and use the standby tank to filter and clean the tank.
(4) Hang back the anode for cleaning and maintenance, use the nickel plated corrugated iron plate as the cathode, and drag the cylinder for 8-12 hours under the current density of 0.5-0.1 A/dm2 (also often used when there is inorganic pollution in the plating solution that affects the quality)
(5) Change the filter element (generally, a group of cotton cores and a group of carbon cores are used for continuous filtration in series, and the periodic replacement can effectively delay the large treatment time and improve the stability of the plating solution), analyze and adjust various parameters, and add additive wetting agent to test the plating.
e) Analysis - The bath should use the key points of the process procedure specified by the process control to regularly analyze the bath composition and Hull cell test, and guide the production department to adjust the bath parameters according to the obtained parameters.
f) Stirring - Like other electroplating processes, the purpose of stirring is to accelerate the mass transfer process, reduce the concentration change and increase the upper limit of allowable current density. Another very important role of stirring the plating solution is to reduce or prevent pinholes in the nickel plating layer. Because, in the electroplating process, the plating ions near the cathode surface are poor, and a large amount of hydrogen is released, which increases the PH value and produces nickel hydroxide colloid, resulting in the retention of hydrogen bubbles and the formation of pinholes. The above phenomena can be eliminated by strengthening the stirring of the residual plating solution. Compressed air, cathode movement and forced circulation (combined with carbon core and cotton core filtration) are commonly used for mixing.
g) Cathode current density Cathode current density has an effect on cathode current efficiency, deposition rate and coating quality. The results show that the cathodic current efficiency increases with the increase of current density in the low current density region when nickel is plated with electrolyte with lower PH; In the area of high current density, the cathodic current efficiency is independent of current density, while when nickel electroplating solution with high PH is used, the cathodic current efficiency has little relationship with current density.
As with other plating types, the range of cathode current density selected for nickel plating should also depend on the composition, temperature and stirring conditions of the plating solution. Due to the large area of PCB assembly, the current density in the high current area differs greatly from that in the low current area. Generally, 2A/dm2 is appropriate. PCB manufacturers, PCB designers and PCBA processors will explain the maintenance methods of PCB nickel plating solution.
然后
聯(lián)系
電話熱線
13410863085Q Q
微信
- 郵箱