
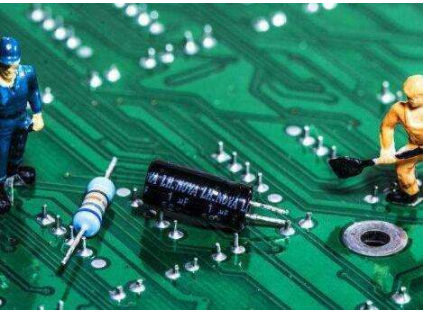
For a long time, the main concern of the test PCB engineer is to ensure that he has an effective test program that can be executed well in production. In circuit testing (ICT) is still a very effective method to detect manufacturing defects. The more advanced ICT system can also add practical value in the test function configuration by providing the method of programming Flash memory, PLD, FPGA and EEPROM during the test. Agilent 3070 system is the MARKet leader in ICT.
Now ICT still plays an important role in the manufacturing and testing of printed circuit board assembly (PCA), but how will people's pursuit of lead-free PCB affect the ICT stage?
The promotion of lead-free soldering technology has LED to a lot of research on PCB surface treatment technology. These studies are mainly based on the technical performance in the PCB construction process. The impact of different PCB surface treatment technologies on the test phase is mostly ignored, or only focused on contact resistance. This report will provide details of the impacts observed in ICT and the need to respond to and understand these changes.
The purpose of this paper is to share PCB surface treatment experience and train engineers for the change of ICT PCB production process requirements. This paper will talk about the surface treatment of lead-free PCB, especially the ICT stage in the manufacturing process of, and reveal that the successful test of lead-free surface treatment also depends on the beneficial contribution of PCB construction process.
A successful ICT test is always related to the physical characteristics of the contact points of the needle bed fixture and the test pad on the PCB. When a very sharp * * * contacts a welded test point, the solder will sag, because the contact pressure of * * * * is far higher than the yield strength of the solder. * * * * Any impurities passing through the surface of the test pad as the solder is depressed. The following uncontaminated solder is now in contact with * * * * to achieve good contact with the test point**** The insertion depth is a direct function of the yield strength of the target material**** The deeper the penetration, the better the contact.
The contact pressure of 26000 to 160000 psi (pounds per square inch) can be applied to * * * * in 8 ounces (oz), depending on the surface diameter. Because the yield strength of solder is about 5000psi, * * * has better contact with this relatively soft solder.
Selection of PCB surface treatment process
Before we understand the causes and consequences, it is important to describe the types of existing PCB processing processes and what these types can provide. All printed circuit boards (PCBs) have copper layers on them. If the copper layer is not protected, it will be oxidized and damaged. There are many different protective layers available, the most common ones are hot air solder leveling (HASL), organic solder protection (OSP), electroless nickel gold immersion (ENIG), silver immersion and tin immersion.
Hot air PCB solder leveling (HASL)
HASL is the main lead surface treatment process used in industry. The process is formed by immersing the circuit board into the lead tin alloy, and excessive solder is removed by the "wind knife", the so-called wind knife is the hot air blowing on the board surface. For PCB process, HASL has many advantages: it is the cheapest PCB, and the surface layer can be welded after repeated reflow, cleaning and storage. For ICT, HASL also provides the process of automatically covering test pads and vias with solder. However, compared with the existing alternative methods, HASL surface has poor flatness or coplanarity. Now there are some lead-free HASL alternative processes, which are more and more popular due to the natural replacement of HASL. The application of HASL has achieved good results over the years, but with the emergence of "environmental protection" green process requirements, the existence of this process is numbered. In addition to the lead-free problem, the increasingly high board complexity and finer spacing have exposed many limitations of the HASL process.
Advantages: The lowest cost PCB surface process can maintain solderability throughout the manufacturing process and has no negative impact on ICT.
Disadvantages: Usually lead containing process is used, which is now limited and will be eliminated before 2007. For fine pin pitch (<0.64mm), it may lead to solder bridging and thickness problems. The unevenness of the surface will lead to the problem of the same surface in the assembly process.
Organic solder protector
Organic solder protective agent (OSP) is used to produce a thin, uniform and consistent protective layer on the copper surface of PCB. This coating protects the circuit from oxidation during storage and assembly operations. This process has existed for a long time, but it was not popularized until recently with the search for lead-free technology and fine pitch solutions.
OSP has better performance in PCA assembly than HASL in terms of the same plane and weldability, but requires significant process changes in the type of flux and the number of thermal cycles. Because its acidic characteristics will reduce the OSP performance and make copper easy to oxidize, it needs to be treated carefully. Assemblers prefer to deal with metal surfaces that are more flexible and can withstand more thermal cycles.
OSP surface treatment is adopted. If the test point is not welded, the contact problem of the needle bed fixture will occur in ICT. If only the sharper * * * type is used to pass through the OSP layer, it will only cause damage and puncture the PCA test via or test pad. The research shows that using higher detection force or changing the type of * * * * has little effect on the yield. The yield strength of untreated copper is one order of magnitude higher than that of lead welding, and the only result is that the exposed copper test pad will be damaged. All testability guidelines strongly recommend that bare copper is not detected directly. When using OSP, you need to define a set of OSP rules for the ICT phase. The most important rule requires that Stencil be opened at the beginning of PCB process to allow solder paste to be added to the test pads and vias that ICT needs to contact.
Advantages: Comparable with HASL in unit cost, good coplanarity, lead-free process, and improved solderability.
Disadvantages: The assembly process needs to be greatly changed. If the unprocessed copper surface is detected, it will be bad for ICT. If the sharp ICT * * * * may damage the PCB, manual preventive treatment is required, which limits ICT testing and reduces the repeatability of testing.
Nickel gold immersion without electroplating
The electroless nickel gold immersion (ENIG) coating has been successfully applied to many circuit boards. Although it has a high unit cost, it has a flat surface and excellent solderability. The main disadvantage is that the electroless nickel layer is very fragile and has been found to crack under mechanical pressure. This is called "black block" or "mud crack" in industry, which has led to some negative reports of ENIG.
Advantages: good weldability, flat surface, long storage life, can withstand multiple reflow soldering.
Disadvantages: high cost (about 5 times of HASL), "black block" problem, cyanide and other harmful chEMIcals are used in the manufacturing process.
Silver immersion
Silver immersion is a newly added method for PCB surface treatment. It is mainly used in Asia and is being promoted in North America and Europe. In the welding process, the silver layer melts into the welding point, leaving a tin/lead/silver alloy on the copper layer, which provides a very reliable welding point for BGA packaging. Its contrast color makes it easy to be checked, and it is also a natural alternative to HASL in welding treatment.
Silver immersion is a surface processing technology with a very good development prospect, but like all new surface processing technologies, the end user is very conservative about this. Many manufacturers regard this process as a "under investigation" process, but it is likely to become the best lead-free surface process choice.
Advantages: good weldability, smooth surface, natural replacement of HASL immersion.
Disadvantages: The conservative attitude of end users means that there is a lack of relevant information in the industry.
Tin immersion
This is a relatively new surface treatment process, which has many SIMilar characteristics with the silver immersion process. However, due to the need to prevent thiourea (possibly a carcinogen) used in the tin immersion process during PCB manufacturing, there are significant health and safety issues to consider. In addition, attention should also be paid to tin migration ("tin burr" effect), although anti migration chemicals can achieve certain results in controlling this problem.
Advantages: good weldability, smooth surface and relatively low cost.
Disadvantages: health and safety issues, limited number of thermal cycles
然后
聯(lián)系
電話熱線
13410863085Q Q
微信
- 郵箱