
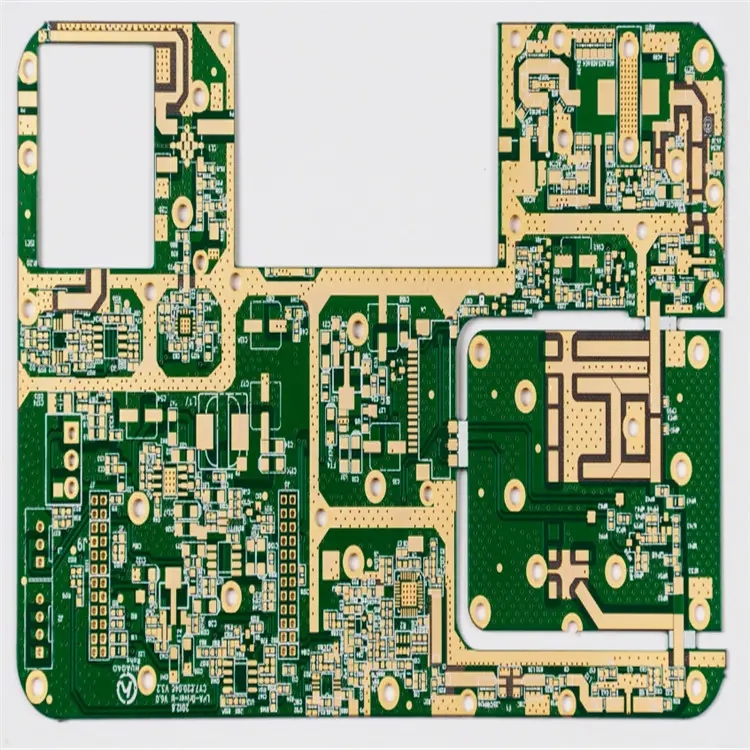
Common problems and resin plug hole of high frequency board stICking dry film
Circuit board manufacturer, circuit board designer and PCBA processor explain the common problems of high-frequency board dry film and resin plug hole
With the continuous development of the electronic industry and the continuous upgrading of products, in order to save space for high-frequency boards, the lines of many boards when designing high-frequency boards have been very SMAll. The previous wet film can no longer meet the current graphic transfer process. Now, generally, small lines are produced with dry film. What problems do we have in the film coating process? The high-frequency board manufacturer will introduce them below.
01. Bubbles appear between the high-frequency plate dry film and the copper foil surface
Bad problem: selecting flat copper foil is the key to ensure no bubbles.
Solution: increase the film pressure of PCB high-frequency board, and handle the board with care.
Bad problem: The film temperature of PCB high-frequency board is too high, resulting in wrinkling of some contact materials due to temperature difference.
Solution: Reduce the film temperature of PCB high-frequency board.
Bad problems: the surface of the hot pressing roller is uneven, with pits and drilling dirt on the adhesive film.
Solution: Regularly check and protect the flatness of the hot pressing roll surface.
02. Dry film wrinkling
Bad problem: The dry film is too sticky, so place the board carefully during operation.
Solution: In case of contact, handle it in time.
Bad problem: PCB high-frequency board is overheated before pasting film.
Solution: The preheating temperature of high-frequency board should not be too high.
03. The dry film is not firmly stuck on the copper foil
Unfavorable problem: the copper foil surface is not cleaned properly, and direct operation will leave oil stain or oxide layer.
Solution: Wear gloves to wash the board.
Adverse problems: The quality of dry film solvent is not up to standard or has expired.
Solution: The manufacturer should select * * * dry film and regularly check the shelf life of dry film.
Bad problems: fast transmission speed, low film temperature of PCB high-frequency board.
Solution: Change the film pasting speed and temperature of PCB high-frequency board.
Bad problem: The processing environment humidity is too high, which leads to the extension of the dry film bonding time.
Solution: Keep the relative humidity of the production environment at 50%.
04. Residual glue
Bad problem: poor dry film quality.
Solution: Replace the dry film.
Bad problem: exposure time is too long.
Solution: Have an understanding of the materials used and conduct reasonable exposure time.
Bad problem: Developer failure.
Solution: Change the developer.
Why some high-frequency circuit boards need resin plug holes
The process of using resin plug holes for high-frequency circuit boards is often due to BGA parts, because the traditional BGA may do via routing from the PAD to the back of the PAD. However, if the BGA is too dense and the via cannot go out, you can directly do VIA routing from the PAD hole to the other layer, and then fill the hole with resin and copper plating to become PAD, which is also known as the VIP process. If you only do VIA on the PAD without using resin plug holes, It is easy to cause tin leakage, leading to short circuit on the back and empty soldering on the front.
The manufacturing process of the resin plug hole of the high-frequency circuit board includes drilling, electroplating, plugging, baking and grinding. After drilling, the hole is plated, then the resin is plugged and baked, and finally the resin is ground flat. Since the resin after grinding does not contain copper, it needs to be coated with a layer of copper again to turn it into PAD. These processes are done before the original drilling process of the high-frequency circuit board, that is, the hole to be plugged is treated first, and then other holes are drilLED, Follow the normal process.
If the plug hole of the high-frequency circuit board is not plugged properly, when there are bubbles in the hole, because the bubbles are easy to absorb moisture, the PCB of the high-frequency circuit board may burst when passing through the tin furnace. However, if there are bubbles in the hole during the process of plugging, the bubbles will extrude the resin during baking, resulting in the situation that one side is concave and the other side is prominent. At this time, the defective products can be detected, and the high-frequency circuit board with bubbles is not likely to burst, because the main reason for the burst is moisture, Therefore, if the boards that have just left the factory or have been baked during loading, generally speaking, they will not cause bursting. PCB manufacturers, PCB designers and PCBA processors will explain the common problems of high-frequency board dry film and resin plug holes.
然后
聯(lián)系
電話熱線
13410863085Q Q
微信
- 郵箱