
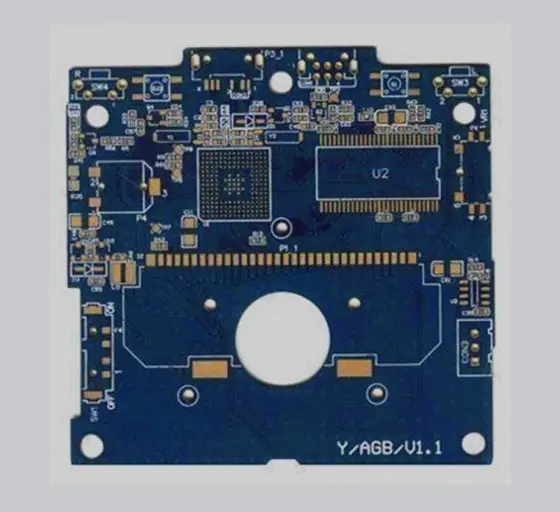
Why is the edge of high-frequency circuit board charred during electroplating
PCB manufacturers, PCB designers and PCBA processors explain why high-frequency PCB edges are charred during electroplating
printed circuit boards, also known as printed circuit boards, are providers of electrICal connections for electronIC components.
Printed circuit board is usually represented by "PCB", not "PCB".
PCB design is mainly layout design; The main advantage of using circuit board is to greatly reduce wiring and assembly errors, and improve the automation level and production labor rate.
High frequency circuit board is a special circuit board with high electromagnetic frequency. Generally speaking, high frequency can be defined as the frequency above 1GHz. Its physical performance, accuracy and technical parameters are very high, and are commonly used in automotive anti-collision systems, satellite systems, radio systems and other fields.
Because electronic products need precise technology and certain environmental and safety adaptability, it has promoted the rapid progress of high-frequency circuit board electroplating technology. In high-frequency circuit board electroplating, the chEMIcal analysis of organic compounds and metal additives is more and more complex, and the chemical reaction process is more and more accurate.
But even so, high-frequency circuit boards still have the problem of edge charring from time to time during electroplating. What is the root cause of the problem?
The reasons for the edge burning of high-frequency circuit board during electroplating are:
1. Insufficient tin and lead metal content
The metal content is insufficient, the current is slightly high, H+is easy to be discharged, and the diffusion and electromigration speed of the bath body become low, leading to scorching.
2. Tin lead anode is too long
The anode is too long and the workpiece is too short, and the power lines at the lower end of the workpiece are too dense, which is easy to scorch; When the anode distribution in the horizontal direction is much longer than the length of the workpiece placed horizontally, the power lines at both ends of the workpiece are dense and easy to be burnt.
3. Current density is too high
Each bath has its best current density range.
The current density is too low, the grain of the coating is coarsened, and even the coating cannot be deposited. When the current density is increased, the cathodic polarization effect is increased, so that the coating is dense and the plating rate is increased. However, if the current density is too high, the coating will be burnt black or charred;
4. Insufficient tank liquid circulation or mixing
Stirring is the main means to improve the convective mass transfer rate. By moving or rotating the cathode, a relative flow can occur between the liquid layer on the workpiece surface and the plating solution at a little distance; The greater the stirring intensity is, the better the convective mass transfer effect is. When the stirring is insufficient, the surface liquid flows unevenly, which causes the coating to be burnt.
5. Insufficient additives
In SIMple salt electroplating, if too many additives are added, the additive film generated by adsorption is too thick, and it is difficult for the main salt metal ions to penetrate the adsorption layer for discharge, but H+is a SMAll proton, which is easy to penetrate the adsorption layer for discharge and hydrogen evolution, and the coating is easy to be burnt. In addition, too many additives have other side effects, so any additives and brighteners must adhere to the principle of adding less and adding more frequently.
In addition, the causes of scorching are
Organic pollution; Contamination by metal impurities; Too much lead in the coating; The anode mud falls into the tank; The hydrolysis of fluoboric acid produces the adhesion of lead fluoride particles. PCB manufacturers, PCB designers and PCBA processors explain why high-frequency PCB edges are charred during electroplating.
然后
聯(lián)系
電話熱線
13410863085Q Q
微信
- 郵箱