
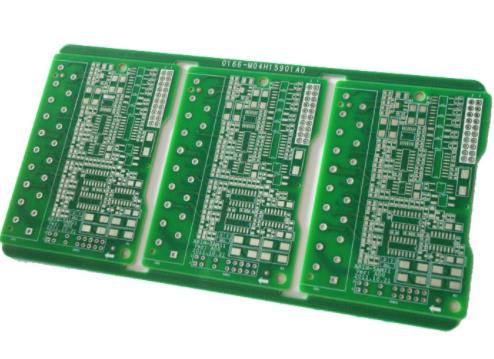
Causes of SMT welding cracks and how to remove corrosion on HDI
The Circuit board manufacturer, circuit board designer and PCBA processor explain the causes of welding cracks during SMT chip processing and how to remove the corrosion on HDI
Nowadays, there are more and more electronIC products, which are more and more refined. As long as the products using electricity need circuit boards, the circuit board factory provides customers with one-stop services of hard boards, soft boards, HDI, FPCA, and soft and hard combination boards. Next, we will analyze the causes of welding cracks during SMT chip processing.
Causes of welding cracks during SMT chip processing
1. The wetting between the soldering pad of the soft board patch and the welding surface of the components did not meet the processing requirements.
2. The use of welding paste did not meet the processing standard.
3. The thermal expansion coefficients of welding and various raw materials of electrical grade do not match, and the spot welding condensation is unstable.
4. The setting of reflow temperature curve cannot make the organic chEMIcal volatile organic compounds and water in the solder paste evaporate before entering the flow back zone.
5. The difficulties of lead-free welding materials in the processing of soft plate patch are high temperature, high interfacial tension and high viscosity. The increase of interfacial tension will certainly make it more difficult for the steam to escape from the refrigeration link, making it difficult for the steam to drain out, thus increasing the proportion of cracks. As a result, there are more air holes and cracks in lead-free welding during SMT chip processing of soft plate.
6. In addition, because the temperature of lead-free welding is higher than that of lead welding, especially in large size, multilayer boards, and Electronic devices with high thermal conductivity, the high temperature is usually about 260 ℃, and the temperature difference between refrigeration condensation and indoor temperature is large, so the ground stress of lead-free welding is also large.
How to remove corrosion on HDI?
How to remove corrosion on HDI?
Over time, your HDI will accumulate more than corrosion. Dirt, dust and all kinds of dirt can easily enter your electronic equipment. Cleaning them can help prevent corrosion. However, if you detect HDI corrosion, you can learn how to remove corrosion and use the following methods to avoid permanent damage.
Use compressed air
Compressed air is a fairly common tool for electronic cleaning. You can use compressed air by releasing short pulses to the inside of the vent. This cleaning method is recommended for routine electronic care, so if you want to deal with corrosion, you will need to open the electronic device and strike it at the source.
Use baking soda
Sodium bicarbonate is a highly effective ingredient for removing HDI corrosion. Not only that, your kitchen cabinet may already contain baking soda. Since baking soda is moderately abrasive, you can use it to scrub away corrosion and residues that will not be released by compressed air. Try using it with a mild brush and distilLED water.
Use distilled water
Speaking of distilled water, this product is also a safe and easy way to remove corrosion on circuit boards. The purest distilled water will not degrade or damage your electronic equipment.
Use household cleaners
Any household cleaner is a good solution to HDI corrosion, but it must be phOSPhate free. Phosphate can effectively prevent corrosion, but it is an important pollution source in all American lakes. However, there are so many phosphate free cleaners that can work properly. There are also special HDI corrosion cleaners on the MARKet.
Use a brush
When you clean the circuit board, the brush can be a super useful tool, because it can help you get into all the tiny components. It is important to choose a brush with soft bristles. Size is also important because you need to be able to achieve all the minimum space.
Most people like to use a toothbrush or paint brush. They are strong and gentle, and most people already have at least one of them.
The lint free microfiber cloth is also a good tool to wipe and dry the circuit board immediately after cleaning. PCB manufacturers, PCB designers and PCBA processors will explain the causes of welding cracks during SMT chip processing and how to remove the corrosion on HDI.
然后
聯(lián)系
電話熱線
13410863085Q Q
微信
- 郵箱